A Closer Look at Slitting Lines for Steel Coils
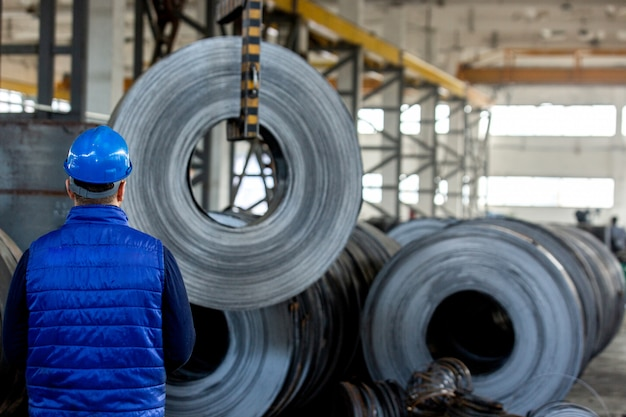
Steel is an indispensable material that forms the backbone of numerous industries, from automotive manufacturing to infrastructure development. At the heart of steel’s versatility lies the steel slitting process, a critical step in transforming raw steel coils into the precise dimensions required by end-users. In this comprehensive article, we’ll delve into the intricacies of steel slitting lines, exploring their various types, the importance of experienced operators, and the key factors that ensure top-notch precision and quality.
Understanding the Steel Slitting Process
The steel slitting process is a crucial manufacturing step that involves cutting large steel coils into narrower strips or “mults” of specific widths and lengths. This process is carried out using specialized machinery known as slitting lines, which are equipped with a decoiler, slitter, and recoiler. The decoiler unwinds the master coil, feeding it into the slitter, where rotary knives precisely slice the steel into the desired widths. The individual mults then travel through a looping pit to ensure stress-free and camber-free recoiling before being packaged and delivered to the customer.
Types of Slitting Lines: Accommodating Diverse Steel Needs
Slitting lines come in a variety of configurations, each designed to handle specific steel grades and thicknesses. These can be broadly categorized into three main types:
Light Gauge Slitting Lines
These machines are engineered to process lighter materials, such as stainless steel, aluminum, and tin plates. Their specialized design and precise cutting mechanisms ensure a smooth and efficient slitting process for these delicate metals.
Medium Gauge Slitting Lines
Handling heavier materials, medium gauge slitting lines often incorporate additional features, such as scrap winding and balling, to accommodate the increased demands of the slitting process.
Heavy Gauge Slitting Lines
At the upper end of the spectrum, heavy gauge slitting lines are the most powerful machines, designed to handle high-strength, thick-gauge metals commonly used in heavy-duty industrial applications.
The Importance of Experienced Operators
Successful steel slitting operations are heavily reliant on the expertise and diligence of the machine operators. These individuals must possess a deep understanding of the slitting process, including the importance of knife clearance, edge condition, and material specifications. Constant inspection and adjustment of the slitting parameters are essential to ensure the final mults meet the customer’s precise requirements.
Knife Clearance: The Key to Precision Slitting
One of the most critical factors in the steel slitting process is the proper maintenance and adjustment of knife clearance. Horizontal clearance, in particular, plays a crucial role in determining the quality of the slit edges. Experienced operators must carefully monitor and adjust the knife clearance to achieve the desired results, as the optimal clearance can vary depending on the specific project and material being processed.
Ensuring Quality through Machine and Material Selection
To deliver consistent, high-quality slit steel coils, it is essential to invest in top-notch slitting machinery and source premium-grade steel. Robust, precision-engineered slitting lines equipped with advanced software, tooling practices, and hardware can streamline production, reduce scrap, and minimize delivery times. Equally important is the quality of the raw steel coils, as poor-quality material can compromise the final product, regardless of the slitting equipment used.
Maintenance and Tooling: The Foundation of Consistent Performance
Proper maintenance of the slitting line’s components, including the knives, spacers, and other tooling, is paramount to ensuring consistent, high-quality output. Regular inspections, calibrations, and replacements of worn parts help maintain the machine’s precision and efficiency, minimizing the risk of defects or inconsistencies in the slit steel coils.
Optimizing Production through Automation and Advanced Technologies
In the ever-evolving landscape of steel processing, leading companies are leveraging the power of automation and advanced technologies to enhance their slitting operations. Sophisticated software, sensor-driven monitoring systems, and data-driven analytics can help streamline production, improve decision-making, and reduce waste, ultimately delivering greater value to their customers.
Customization and Flexibility: Meeting Diverse Customer Needs
The steel industry is characterized by a wide range of end-user requirements, from automotive manufacturers to construction firms. Successful steel processors must be able to adapt their slitting capabilities to accommodate these diverse needs. Offering a versatile range of slitting services, from custom widths and lengths to specialized coatings or surface treatments, enables steel processors to cater to the unique demands of their clients.
Sustainability and Environmental Considerations
As the global focus on sustainability intensifies, steel processors are increasingly incorporating eco-friendly practices into their operations. This includes optimizing material usage, minimizing waste, and exploring renewable energy sources to power their slitting lines. By embracing sustainable approaches, steel processors can contribute to the industry’s overall environmental stewardship while delivering high-quality products to their customers.
The Role of Steel Processors in the Supply Chain
Steel processors, such as National Material Company, play a crucial role in the broader steel supply chain. By providing manufacturers with the right steel materials for their specific applications, these processors act as a vital link between raw steel producers and end-users. Their expertise in steel slitting, along with their commitment to quality and customer service, helps to ensure the smooth flow of materials and the timely delivery of finished products.
Continuous Improvement and Innovation
The steel industry is constantly evolving, driven by technological advancements, changing market demands, and the need for greater efficiency and sustainability. Successful steel processors must embrace a culture of continuous improvement, actively seeking out new technologies, processes, and best practices to stay ahead of the curve. By investing in research and development, collaborating with industry partners, and fostering a culture of innovation, steel processors can continuously enhance their slitting capabilities and deliver greater value to their customers.
Conclusion
The steel slitting process is a critical component of the steel industry, enabling the transformation of raw coils into the precise dimensions required by a wide range of end-users. By understanding the various types of slitting lines, the importance of experienced operators, and the key factors that ensure quality and consistency, steel processors can optimize their operations and deliver exceptional products to their customers. As the industry continues to evolve, embracing new technologies, sustainable practices, and a commitment to innovation will be the hallmarks of success for steel processors in the years to come.