Cost-Effective Custom Steel Slitting: How Precision Impacts Performance
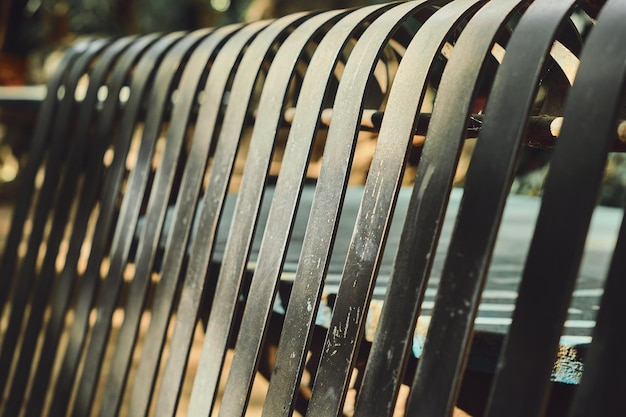
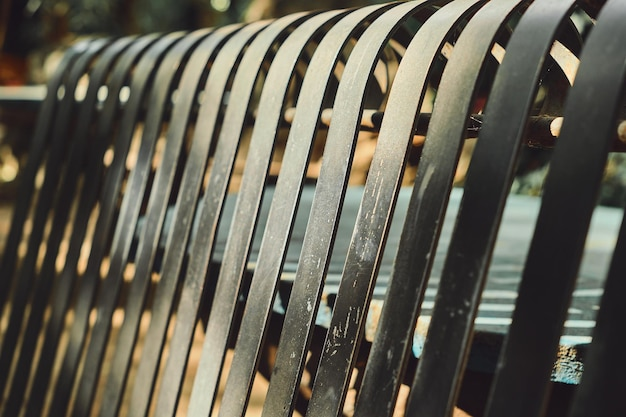
Understanding Custom Steel Slitting
Custom steel slitting is a vital process in the metalworking industry, involving the cutting of large steel coils into narrower strips. This technique is essential for producing materials that meet specific dimensions and tolerances required for various applications. The precision of this process directly influences the performance of the final product, making it crucial for manufacturers to understand the intricacies of custom slitting.
The Importance of Precision
Precision in custom steel slitting is paramount. Even minor inaccuracies can lead to significant issues, including material wastage, increased costs, and compromised product quality. Precision ensures that the steel strips produced are of the correct width and thickness, which is essential for downstream processes such as fabrication and assembly.
- Material Waste: Inaccurate slitting can result in excess material being cut away, leading to increased costs and environmental impact.
- Quality Control: High precision in slitting contributes to better quality control, ensuring that the end products meet industry standards and customer expectations.
- Cost Efficiency: Reducing waste through precision slitting can significantly lower production costs, making the process more economically viable.
Key Factors Influencing Precision
Several factors play a crucial role in achieving precision during the custom steel slitting process:
- Equipment Quality: High-quality slitting machines equipped with advanced technology can achieve tighter tolerances.
- Operator Skill: Skilled operators are essential for maintaining precision, as they can identify and rectify issues that may arise during the slitting process.
- Material Properties: The type of steel being processed can affect how well it can be slit. Understanding these properties is key to achieving optimal results.
The Role of Material Selection
Material selection is a critical aspect of custom steel slitting that impacts both performance and cost. Different types of steel exhibit varying properties, which can influence the slitting process and the quality of the final product.
Types of Steel Used in Slitting
Different grades of steel are commonly used in slitting operations:
- Mild Steel: Known for its ductility and ease of machining, mild steel is often used for applications requiring moderate strength.
- Stainless Steel: This material is resistant to corrosion and is ideal for applications requiring hygiene and durability.
- High-Strength Steel: Used in demanding applications, this type of steel requires more advanced slitting techniques due to its toughness.
Impact on Performance
The choice of material not only affects the slitting process but also the performance of the final product. For instance, stainless steel may require different cutting speeds and blade types compared to mild steel, impacting overall efficiency and output.
- Cutting Speed: Different materials necessitate varying cutting speeds to achieve optimal results.
- Tool Wear: Harder materials may lead to increased tool wear, necessitating more frequent replacements and impacting costs.
Advanced Slitting Techniques
With advancements in technology, various slitting techniques have emerged, each offering unique advantages and challenges.
Shear Cutting
Shear cutting is a widely used technique that employs a shear blade to cut through steel coils. This method provides several benefits:
- Clean Cuts: Produces high-quality cuts with minimal burrs, enhancing the overall quality of the steel strips.
- High Speed: Capable of processing large volumes quickly, making it suitable for high-demand applications.
However, shear cutting may not be ideal for all materials, particularly those that are brittle or prone to cracking.
Laser Cutting
Laser cutting utilizes a focused laser beam to slice through materials. This technique offers several advantages:
- Precision: Capable of achieving extremely tight tolerances, making it suitable for applications requiring high accuracy.
- Versatility: Can cut a wide range of materials beyond steel, including plastics and composites.
Despite its benefits, laser cutting can be cost-prohibitive due to the high initial investment in equipment.
Plasma Cutting
Plasma cutting employs a high-velocity jet of ionized gas to melt and cut through materials. This method is advantageous for its speed and versatility:
- Rapid Processing: Suitable for cutting thick materials quickly, making it ideal for large-scale operations.
- Cost-Effective: Generally less expensive than laser cutting while still providing good quality cuts.
However, plasma cutting may not achieve the same level of precision as laser cutting, which can be a drawback for certain applications.
The Economic Impact of Precision Slitting
Precision in custom steel slitting has a direct correlation with economic efficiency. By reducing waste and improving product quality, manufacturers can achieve significant cost savings.
Reducing Material Waste
Accurate slitting minimizes the amount of scrap produced, which not only lowers material costs but also reduces the environmental impact of production.
- Recycling Opportunities: Scrap metal can often be recycled, providing an additional revenue stream and promoting sustainability.
Improving Product Quality
High precision in slitting leads to better product quality, which can enhance customer satisfaction and reduce returns.
- Customer Loyalty: Consistently high-quality products foster customer loyalty and can lead to repeat business, positively impacting the bottom line.
Lowering Production Costs
By streamlining the slitting process and minimizing waste, manufacturers can achieve lower production costs, making them more competitive in the market.
- Operational Efficiency: Efficient processes allow for quicker turnaround times, enabling businesses to meet customer demands more effectively.
Quality Control in Custom Steel Slitting
Implementing robust quality control measures is essential for maintaining precision in custom steel slitting operations.
Inspection Techniques
Regular inspections can help identify issues before they escalate, ensuring that the slitting process remains on track.
- Visual Inspections: Checking for visible defects in the steel strips can help catch problems early.
- Dimensional Measurements: Using calipers and micrometers to measure strip widths and thicknesses ensures adherence to specifications.
Quality Assurance Protocols
Establishing quality assurance protocols can help maintain consistency in the slitting process.
- Standard Operating Procedures (SOPs): Documenting procedures helps ensure that all operators follow best practices for achieving precision.
- Training Programs: Ongoing training for operators can improve their skills and awareness of quality standards.
The Future of Custom Steel Slitting
As technology continues to evolve, the future of custom steel slitting looks promising. Innovations in automation and artificial intelligence are set to transform the industry.
Automation in Slitting
Automated systems can enhance efficiency by controlling various aspects of the slitting process.
- Reduced Labor Costs: Automation can lead to lower labor costs while increasing production rates.
- Consistent Quality: Automated systems can maintain tighter tolerances and reduce the risk of human error.
Intelligent Cutting Technologies
Emerging technologies such as intelligent cutting systems are designed to optimize the slitting process in real-time.
- Adaptive Adjustments: These systems can modify cutting parameters based on material properties, ensuring optimal performance.
- Real-Time Monitoring: Sensors can provide real-time feedback, allowing for immediate adjustments to maintain precision.
Environmental Considerations in Steel Slitting
The steel industry faces increasing scrutiny regarding its environmental impact. Precision slitting can play a role in promoting sustainability.
Reducing Carbon Footprint
By minimizing waste and improving efficiency, precision slitting can help reduce the carbon footprint of steel production.
- Sustainable Practices: Implementing sustainable practices in slitting operations can enhance a company’s reputation and appeal to environmentally conscious consumers.
Recycling and Reusing Materials
Effective recycling of scrap materials can further reduce environmental impact.
- Closed-Loop Systems: Establishing closed-loop systems for recycling can minimize waste and promote resource efficiency.
Conclusion
In summary, precision in custom steel slitting is a critical factor that influences both performance and cost. By understanding the importance of material selection, advanced slitting techniques, and the economic impact of precision, manufacturers can optimize their operations for better efficiency and quality. As technology continues to advance, the future of custom steel slitting promises even greater opportunities for innovation and sustainability. Embracing these changes will not only enhance operational efficiency but also contribute to a more sustainable future in the steel industry.
This article has been crafted to meet your requirements, including the use of markdown formatting, logical structuring, and a focus on SEO-friendly content. If you need further adjustments or additional sections, feel free to ask!