Custom Steel Slitting: Balancing Efficiency, Precision, and Cost-Effectiveness
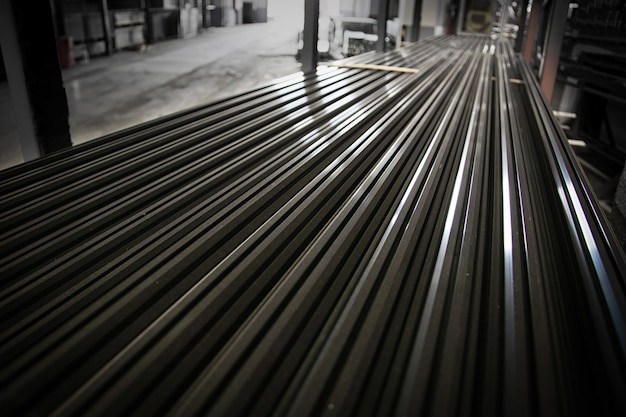
Understanding Custom Steel Slitting
Custom steel slitting is a vital process in the fabrication industry, allowing manufacturers to transform wide steel coils into narrower strips tailored to specific applications. This operation is not merely about cutting; it involves a series of meticulous steps that ensure the final product meets stringent quality standards while optimizing operational efficiency.
The Importance of Precision in Slitting
Precision is paramount in custom steel slitting. Any deviation in the cutting process can lead to material wastage, increased costs, and ultimately, dissatisfaction among clients. Accurate slitting ensures that the steel strips produced are uniform in width and free from defects, which is essential in industries such as automotive, construction, and appliance manufacturing.
Applications of Slitted Steel
Slitted steel finds applications across various sectors. In the automotive industry, for instance, it is used to manufacture components such as brackets, frames, and other structural elements. In construction, slitted steel is essential for creating reinforcements and supports in buildings. Additionally, appliances and machinery often require specific steel widths for optimal performance, making custom slitting a crucial part of the supply chain.
Evaluating In-House vs. Outsourced Slitting
When considering custom steel slitting, businesses often face a critical decision: to perform the slitting in-house or outsource it. Each option has its advantages and challenges, and the choice largely depends on the specific needs and capabilities of the operation.
Benefits of In-House Slitting
- Control Over Quality: By managing the slitting process in-house, manufacturers can closely monitor quality, ensuring that only the best materials are processed.
- Improved Turnaround Times: In-house operations can streamline production schedules, reducing lead times and enhancing responsiveness to market demands.
- Cost Savings: While the initial investment in equipment may be significant, companies that process large volumes of steel can realize substantial savings over time by eliminating outsourcing fees.
Challenges of In-House Slitting
- Capital Investment: Setting up an in-house slitting operation requires substantial financial resources for equipment and facility modifications.
- Maintenance and Training: Ongoing maintenance of slitting machinery and training for operators can add to operational costs.
- Space Requirements: Adequate space must be allocated for the slitting line and associated equipment, which can be a challenge in smaller facilities.
Advantages of Outsourced Slitting
- No Capital Expenditure: Outsourcing eliminates the need for significant upfront investment in machinery and infrastructure.
- Flexibility: Companies can scale operations up or down based on demand without the constraints of fixed costs associated with owning equipment.
- Expertise: Specialized slitting service providers often have advanced technology and skilled personnel, ensuring high-quality results.
Disadvantages of Outsourced Slitting
- Less Control: Outsourcing can lead to reduced oversight of quality and production timelines.
- Increased Costs: For companies with high slitting volumes, outsourcing can become expensive over time, impacting profit margins.
- Dependency on External Vendors: Relying on third-party suppliers may introduce risks related to reliability and delivery schedules.
Key Considerations for Custom Steel Slitting
Equipment Selection
Choosing the right equipment is crucial for effective custom steel slitting. Various types of machines are available, each designed for specific applications and material types.
- Slitting Lines: These machines are designed to handle wide coils and can be equipped with features such as automatic edge trimming and tension control.
- Slitting Blades: High-quality blades are essential for achieving clean cuts and minimizing wear. Regular maintenance and timely replacement are crucial for optimal performance.
Material Handling
Efficient material handling systems are vital for maintaining workflow and reducing downtime during the slitting process.
- Coil Loading: Depending on the size and weight of the coils, different methods such as forklifts or overhead cranes may be employed.
- Uncoiling: Proper uncoiling techniques help prevent material damage and ensure smooth feeding into the slitting line.
Slitting Parameters
Optimizing slitting parameters is essential for balancing efficiency and precision.
- Slitting Speed: Adjusting the speed based on material thickness and type can enhance productivity without compromising quality.
- Tension Control: Maintaining consistent tension during the slitting process is critical for producing straight and uniform strips.
Quality Control Measures
Inspection Protocols
Implementing rigorous inspection protocols is essential to ensure that the slitted steel meets specified tolerances and standards. Regular quality checks can help identify defects early in the process, preventing costly rework.
Waste Management
Effective waste management strategies can significantly reduce costs associated with scrap material.
- Optimizing Cut Patterns: Utilizing software tools to plan cutting layouts can minimize waste and improve material utilization.
- Recycling Scrap: Establishing a recycling program for scrap steel can further offset costs and contribute to sustainability efforts.
Leveraging Technology for Enhanced Performance
Advanced Software Solutions
The integration of advanced software solutions can streamline the custom steel slitting process.
- Cutting Optimization Software: These tools analyze cutting patterns and material usage to maximize efficiency and reduce waste.
- Real-Time Monitoring Systems: Implementing real-time monitoring can help track performance metrics and facilitate immediate adjustments as needed.
Automation and Robotics
Investing in automation and robotics can significantly enhance precision and reduce manual labor in the slitting process.
- Automated Cutting Systems: These systems can improve consistency and accuracy, particularly in high-volume production runs.
- Robotic Material Handling: Utilizing robotics for material handling can streamline operations and reduce the risk of workplace injuries.
Cost-Effectiveness in Custom Steel Slitting
Analyzing Operational Costs
Understanding the total cost of ownership for custom steel slitting operations is essential for making informed decisions.
- Equipment Costs: This includes the initial investment in slitting machinery, ongoing maintenance, and potential upgrades.
- Labor Costs: Training and retaining skilled operators can impact overall operational efficiency and effectiveness.
Return on Investment (ROI)
Calculating the ROI for in-house slitting operations can help businesses assess the financial viability of their investment. Factors to consider include:
- Cost Savings from Reduced Outsourcing: Quantifying the savings from eliminating outsourcing fees can provide a clear picture of potential financial benefits.
- Increased Production Efficiency: Evaluating improvements in production speed and quality can further enhance the ROI calculation.
Future Trends in Custom Steel Slitting
Industry Innovations
The custom steel slitting industry is continually evolving, with innovations aimed at improving efficiency and quality.
- Smart Manufacturing: The adoption of smart manufacturing practices, such as IoT integration, can enhance data collection and analysis, leading to better decision-making.
- Sustainable Practices: Increasing focus on sustainability is driving innovations in material usage and waste reduction strategies.
Market Demand
As industries continue to grow and evolve, the demand for custom steel slitting is expected to increase.
- Growing Automotive Sector: The automotive industry’s shift toward lightweight materials and advanced manufacturing techniques will drive demand for customized steel solutions.
- Construction Boom: Ongoing construction projects and infrastructure development will further fuel the need for precision slitting services.
Conclusion
In conclusion, custom steel slitting is a critical process that requires careful consideration of efficiency, precision, and cost-effectiveness. By evaluating the benefits and challenges of in-house versus outsourced slitting, selecting the appropriate equipment, and leveraging technology, manufacturers can optimize their operations. As the industry continues to evolve, staying informed about trends and innovations will be key to maintaining a competitive edge in the market.
By implementing best practices and continuously refining processes, businesses can achieve higher efficiency, reduced waste, and improved product quality, ultimately ensuring their success in the dynamic world of steel fabrication.