Edge Conditioning in Steel Slitting: Improving Safety and Reducing Downtime
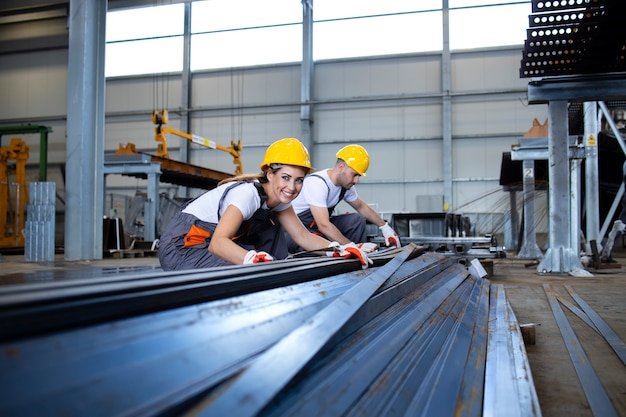
Edge conditioning is a crucial process in the metalworking industry, particularly in steel slitting. This procedure not only enhances the quality and functionality of metal strips but also plays a significant role in improving safety and minimizing downtime during manufacturing operations. By refining the edges of steel sheets, strips, or coils, edge conditioning ensures that the materials are prepared optimally for subsequent processes, thus driving efficiency and reliability in production.
In this article, we will delve into the intricacies of edge conditioning, its techniques, benefits, and applications in steel slitting, as well as the technological advancements that are reshaping this vital aspect of metal processing.
Understanding Edge Conditioning
Edge conditioning refers to the process of refining the edges of metal sheets, strips, or coils to enhance their quality and functionality. This initial step is critical for ensuring that the materials are suitable for various manufacturing processes such as forming, joining, or coating. The primary goals of edge conditioning include:
- Enhancing Safety: By removing sharp edges and burrs, edge conditioning reduces the risk of injuries during handling and assembly.
- Improving Performance: Smoother edges lead to better flow characteristics and reduce friction during subsequent operations.
- Facilitating Further Processing: Properly conditioned edges allow for seamless integration into further manufacturing processes.
Importance in Steel Slitting
In the context of steel slitting, edge conditioning is particularly vital. The slitting process involves cutting large coils of steel into narrower strips, which are then used in various applications. If the edges of these strips are not conditioned properly, it can lead to issues such as:
- Increased risk of injury during handling
- Compromised structural integrity
- Inefficiencies in downstream processes
By investing in effective edge conditioning practices, manufacturers can enhance the overall quality of their steel products and streamline their operations.
Techniques of Edge Conditioning
Several techniques are employed in edge conditioning, each tailored to meet specific requirements and desired edge characteristics. Below are some of the most common methods used in the industry.
Deburring
Deburring involves the removal of burrs—small, raised edges or protrusions that often form during cutting or shearing operations. This technique not only improves safety by eliminating sharp edges but also enhances the aesthetic appeal of the metal strips.
Edge Trimming
Edge trimming is the process of cutting away excess material from the edges of metal sheets or coils. This ensures that the edges are uniform and free from irregularities, which is essential for achieving consistent quality in the final products.
Edge Rolling
Edge rolling is a technique that involves bending or rolling the edges of steel strips to create a smoother, rounded profile. This method is particularly beneficial in reducing the risk of injury from sharp edges and facilitates easier handling during subsequent operations.
Edge Beveling
Beveling creates an angled edge on a metal surface, which is often necessary for specific applications such as welding. Beveled edges allow for better joint fit-up and improved penetration during the welding process.
Surface Preparation for Coating
Prior to applying coatings or paints, the edges of steel strips must be prepared to ensure proper adhesion. This may involve cleaning, etching, or applying surface treatments to enhance the bonding characteristics of the material.
Benefits of Edge Conditioning
The advantages of edge conditioning extend beyond mere aesthetics. Let’s explore some of the key benefits that this process offers.
Enhanced Durability
By refining the edges of steel components, edge conditioning reduces the risk of failure due to stress concentration and crack initiation. This leads to an overall increase in the durability and lifespan of the products.
Improved Strength
Conditioning the edges helps eliminate weak points in the material, thereby enhancing its overall strength. This is particularly crucial in applications where metal components are subjected to heavy loads or stress.
Increased Safety
The removal of sharp edges and burrs minimizes the risk of injuries to workers and end-users during handling and assembly processes. This not only protects personnel but also contributes to a safer workplace environment.
Optimized Performance
Smooth, rounded edges reduce friction and improve the functionality of steel components. By minimizing resistance, edge conditioning can enhance the overall performance of the material, particularly in applications involving fluid flow.
Reduced Friction and Wear
By smoothing out the edges, edge conditioning decreases friction between metal components, which in turn reduces wear and tear. This extends the product’s lifespan and lowers maintenance costs, resulting in significant savings for manufacturers.
Improved Aesthetics and Quality
Edge conditioning enhances the visual appeal of steel products, providing a clean and professional appearance. Consistent edge dimensions and the elimination of irregularities contribute to higher quality standards.
Facilitation of Further Manufacturing Processes
Properly conditioned edges streamline subsequent manufacturing processes such as forming, bending, welding, and joining. This allows for smoother and more precise operations, ultimately reducing production time and improving efficiency.
Applications of Edge Conditioning in Steel Slitting
Edge conditioning finds extensive applications across various industries, particularly in sectors that rely heavily on steel components. Here are some key industries where edge conditioning plays a crucial role.
Automotive Industry
In the automotive sector, edge conditioning is vital for ensuring the safety and performance of various components. For instance, the edges of body panels are often conditioned to eliminate sharp edges, thereby preventing injuries during handling. Additionally, engine components like crankshafts and camshafts benefit from edge conditioning to reduce stress concentrations.
Aerospace Industry
Precision and reliability are paramount in the aerospace industry. Edge conditioning ensures the integrity and performance of components such as turbine blades, where imperfections can lead to catastrophic failures. Conditioning the edges of structural components, like wing panels, enhances their strength and reduces the risk of fatigue failure.
Construction Industry
In construction, edge conditioning is essential for various metal components used in infrastructure projects. Structural steel beams and columns often undergo edge conditioning to remove sharp edges, ensuring a safe and secure fit during assembly. Additionally, metal roofing and cladding materials benefit from edge conditioning to improve aesthetics and longevity.
Electrical and Electronics Industry
Edge conditioning is also crucial in the electrical and electronics sectors, where metal strips are used in transformers, motors, and connectors. High-quality edges ensure reliability and safety in electrical systems, which is critical for preventing failures.
Appliance Manufacturing
In the appliance industry, edge conditioning provides metal strips used in the production of refrigerators, washing machines, and ovens. The precision achieved through edge conditioning facilitates proper fitting and functioning of parts within these appliances.
Technological Advancements in Edge Conditioning
The landscape of edge conditioning is continuously evolving, driven by technological advancements that enhance efficiency, precision, and safety. Here are some notable innovations reshaping this critical process.
Automation
Automation has revolutionized edge conditioning operations. Automated systems now control feeding, conditioning, and quality checks, eliminating the need for manual intervention. This enhances efficiency and reduces the likelihood of errors and accidents.
Computerized Controls
Modern edge conditioning systems are equipped with computerized controls that allow for precise monitoring and adjustment of process parameters. This capability enables manufacturers to optimize conditions for achieving the best results.
Advanced Materials
The development of advanced materials for tools and equipment used in edge conditioning has significantly improved durability and performance. High-strength alloys and specialized coatings extend the lifespan of conditioning tools, reducing downtime for maintenance.
Laser Alignment Systems
Laser alignment systems are increasingly being integrated into edge conditioning processes. These systems ensure that equipment components are perfectly aligned, minimizing the risk of miscuts and enhancing the quality of the finished product.
Safety Features
Modern edge conditioning setups incorporate advanced safety features, such as emergency stop systems, safety guards, and monitoring tools. These enhancements help mitigate risks and ensure a safer working environment for personnel.
Choosing the Right Edge Conditioning Service Provider
Selecting the right service provider for edge conditioning is crucial for achieving optimal results. Here are some factors to consider when making your choice:
Expertise and Experience
Assess the provider’s experience and technical expertise in edge conditioning. A reputable provider should have a skilled team capable of handling various metal types, thicknesses, and sizes.
Range of Services
Look for a provider that offers a comprehensive range of edge conditioning services. This ensures that all your needs can be met without the hassle of switching providers.
Quality Assurance
A reliable service provider will implement stringent quality assurance processes to ensure consistent and accurate edge conditioning results. They should adhere to industry standards and conduct thorough inspections to maintain high-quality outcomes.
Customer Testimonials
Reading customer reviews and testimonials can provide valuable insights into the provider’s reliability and quality of service. Look for feedback regarding their responsiveness, turnaround times, and overall satisfaction.
Technology and Equipment
Inquire about the technology and equipment used by the service provider. Advanced machinery and innovative techniques can significantly impact the quality and efficiency of edge conditioning processes.
Conclusion
Edge conditioning in steel slitting is a vital process that enhances safety, improves product quality, and reduces downtime in manufacturing operations. By employing various techniques to refine the edges of steel strips, manufacturers can ensure that their products meet the high standards required across multiple industries.
As technological advancements continue to reshape the landscape of edge conditioning, the importance of investing in effective practices and reliable service providers cannot be overstated. By prioritizing edge conditioning, manufacturers can enhance their operational efficiency and drive success in an increasingly competitive market.
This article provides a comprehensive overview of edge conditioning in steel slitting, emphasizing its significance in improving safety and reducing downtime. Each section is designed to offer valuable insights while maintaining a logical flow, ensuring that readers can easily grasp the importance of this critical process in the metalworking industry.