Future Trends in Steel Coil Slitting Technology
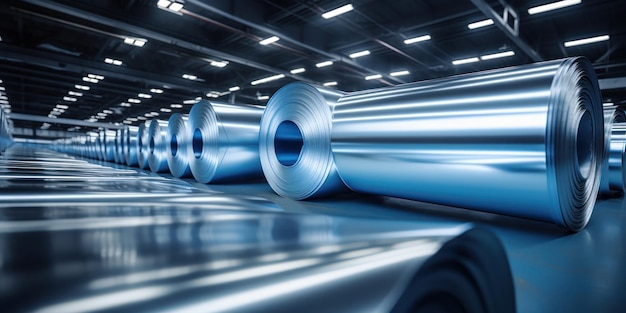
The steel coil slitting industry is on the cusp of a transformative phase, driven by technological advancements and evolving market demands. As manufacturers seek greater efficiency, precision, and sustainability, several key trends are emerging that will reshape the landscape of steel coil slitting technology. This article delves into these trends, examining their implications for the industry and offering insights into the future of steel processing
Automation and Smart Technologies
Embracing Advanced Automation
The integration of automation in steel coil slitting technology is revolutionizing operations. Automated systems streamline processes, enhancing efficiency and reducing human error. These systems can dynamically adjust cutting parameters, ensuring optimal performance across various materials and thicknesses.
- Increased Precision: Automated machines utilize advanced algorithms to control cutting speeds and blade angles, resulting in more accurate cuts.
- Reduced Downtime: With automated setups, changeovers between different coil specifications can be executed swiftly, minimizing production halts.
- Enhanced Monitoring: Operators can leverage real-time data analytics for better decision-making and proactive maintenance.
The Role of Smart Technologies
The advent of Industry 4.0 has ushered in a new era of smart steel processing. By integrating IoT devices and cloud computing, manufacturers can monitor their operations remotely, analyze data in real-time, and implement predictive maintenance strategies.
- Remote Monitoring: Operators can track machine performance from anywhere, allowing for immediate interventions when issues arise.
- Data-Driven Insights: Advanced analytics provide manufacturers with insights into production trends, enabling them to optimize processes continually.
- Predictive Maintenance: By analyzing data patterns, potential equipment failures can be identified before they occur, reducing unplanned downtime.
Enhanced Blade Technology
Innovations in Blade Design
The development of high-performance blades is critical for improving the efficiency and quality of slitting operations. New materials and designs are being utilized to enhance cutting performance and durability.
- Material Advancements: Blades made from high-speed steel and carbide offer superior longevity and resistance to wear.
- Precision Cutting: Innovative geometries in blade design minimize burr formation and improve edge quality, reducing the need for secondary processing.
- Cost Efficiency: Longer-lasting blades result in lower replacement costs and reduced waste, enhancing overall production efficiency.
Laser-Guided Slitting Techniques
Laser technology is making waves in the steel slitting sector, allowing for unparalleled precision and minimal material loss. Laser-guided slitting systems can achieve intricate cuts that traditional methods struggle to replicate.
- Minimal Heat Affected Zone: Laser cutting generates less heat, preserving the integrity of the material and reducing post-processing requirements.
- Complex Shapes: The flexibility of laser technology allows for the creation of complex geometries that expand design possibilities in product development.
Sustainability and Eco-Friendly Practices
Rising Environmental Concerns
The steel industry is increasingly aware of its environmental impact. As sustainability becomes a priority, manufacturers are adopting eco-friendly practices in their operations.
- Energy Efficiency: New machinery designs focus on reducing energy consumption, contributing to lower carbon footprints.
- Waste Reduction: Advanced slitting technologies aim to minimize scrap and optimize material usage, leading to more sustainable production practices.
- Recycling Initiatives: Many manufacturers are implementing recycling programs for scrap materials generated during slitting, further enhancing their sustainability efforts.
Regulatory Compliance
With stricter environmental regulations being enforced globally, steel manufacturers must adapt to comply with these standards. This includes investing in cleaner technologies and practices that align with regulatory requirements.
- Emission Controls: Advanced filtration systems are being integrated into slitting lines to reduce airborne pollutants.
- Sustainable Materials: The use of recycled steel and other sustainable materials is becoming more common, aligning with industry trends toward circular economy practices.
Flexibility and Customization
Adapting to Market Demands
The ability to adapt quickly to changing market demands is crucial for manufacturers. Modern steel coil slitting machines are designed with flexibility in mind, allowing for rapid adjustments to accommodate various coil sizes, thicknesses, and materials.
- Quick Changeover Systems: These systems enable operators to switch between different product specifications with minimal downtime, enhancing overall productivity.
- Modular Designs: Many machines now feature modular components that can be easily upgraded or replaced, ensuring longevity and adaptability.
Custom Solutions for Diverse Applications
As industries evolve, the need for customized solutions becomes more pronounced. Manufacturers are increasingly offering tailored slitting machines that cater to specific customer requirements.
- Specialized Configurations: Custom-built machines can be designed to handle unique materials or specific cutting processes, ensuring optimal performance.
- Client Collaboration: Engaging with clients to understand their unique needs fosters innovation and drives the development of bespoke solutions.
Integration with Industry 4.0 Technologies
The Smart Factory Concept
The integration of Industry 4.0 technologies is transforming traditional manufacturing processes into smart factories. Steel coil slitting operations are no exception, with many manufacturers embracing this trend.
- Connected Devices: IoT-enabled machines can communicate with each other, sharing data that enhances overall operational efficiency.
- Real-Time Analytics: Data collected from various processes can be analyzed in real-time to identify bottlenecks and optimize workflows.
Enhanced Supply Chain Management
Smart technologies facilitate better supply chain management by providing visibility and control over the entire production process.
- Inventory Management: Real-time tracking of materials and products allows manufacturers to maintain optimal inventory levels, reducing waste and costs.
- Demand Forecasting: Advanced analytics can predict market trends, enabling manufacturers to adjust production schedules accordingly.
Operator Safety and Ergonomics
Prioritizing Worker Safety
As technology advances, so does the focus on operator safety. Modern steel coil slitting machines are designed with safety features that protect workers from potential hazards.
- Automated Safety Systems: Sensors and emergency stop buttons are integrated into machines to prevent accidents and injuries.
- Ergonomic Designs: Workstations are designed with ergonomics in mind, reducing strain on operators and enhancing comfort during long shifts.
Training and Skill Development
With the introduction of sophisticated machinery, ongoing training and skill development for operators are essential.
- Comprehensive Training Programs: Manufacturers are investing in training programs that equip operators with the skills needed to operate advanced machinery safely and efficiently.
- Continuous Learning: Encouraging a culture of continuous learning ensures that employees stay up-to-date with the latest technologies and best practices.
Data-Driven Decision Making
Leveraging Big Data
The use of big data analytics is becoming increasingly important in the steel industry. By harnessing data from various sources, manufacturers can make informed decisions that drive efficiency and productivity.
- Performance Monitoring: Data collected from machines can be analyzed to monitor performance and identify areas for improvement.
- Quality Control: Advanced analytics can help detect defects and inconsistencies in real-time, ensuring that only high-quality products reach the market.
Predictive Maintenance
Predictive maintenance strategies are gaining traction in the steel coil slitting industry, allowing manufacturers to anticipate and address maintenance needs before they become critical.
- Condition Monitoring: Sensors can track the condition of machinery, providing insights into when maintenance is required.
- Cost Savings: By preventing unexpected breakdowns, manufacturers can save on repair costs and minimize downtime.
Increased Versatility in Material Handling
Handling Diverse Materials
Modern steel coil slitting machines are designed to handle a wider variety of materials, including high-strength and lightweight alloys. This versatility enables manufacturers to cater to diverse customer needs.
- Multi-Material Processing: Machines can be configured to handle different materials without extensive modifications, enhancing operational flexibility.
- Adaptable Tooling: Tooling can be easily changed to accommodate various material types and thicknesses, ensuring optimal cutting performance.
Improved Material Flow
Efficient material handling is crucial for maintaining productivity in steel processing operations. Innovations in material flow systems are enhancing the efficiency of slitting lines.
- Automated Material Handling: Automated systems for loading and unloading coils reduce manual labor and improve safety.
- Streamlined Processes: Enhanced material flow systems minimize delays and ensure a smooth transition between processes.
Customization and Modular Design
Tailored Solutions for Unique Needs
As industries evolve, the demand for customized solutions is increasing. Manufacturers are offering tailored slitting machines that meet specific customer requirements.
- Modular Components: Many machines now feature modular components that can be easily upgraded or replaced, ensuring longevity and adaptability.
- Client Collaboration: Engaging with clients to understand their unique needs fosters innovation and drives the development of bespoke solutions.
Expanding Capabilities
The modular design of modern slitting machines allows manufacturers to expand their capabilities without the need for significant capital investment.
- Scalability: As production demands increase, manufacturers can easily add new modules or features to existing machines.
- Future-Proofing: Investing in modular technology ensures that manufacturers can adapt to changing market conditions and customer needs.
Conclusion
The future of steel coil slitting technology is bright, characterized by advancements in automation, blade technology, sustainability, and data-driven decision-making. As manufacturers embrace these trends, they position themselves to meet the evolving demands of the market while enhancing efficiency and productivity. By investing in innovative technologies and prioritizing safety and customization, the steel industry can look forward to a future that is not only more efficient but also more sustainable.
With these trends paving the way, the steel coil slitting industry is set to undergo a significant transformation, ensuring that it remains competitive in an ever-changing landscape. As we move forward, the integration of these advancements will be crucial for manufacturers looking to thrive in the modern manufacturing environment.