Heavy Gauge Steel Slitting: Meeting Demands for High Efficiency and Accuracy
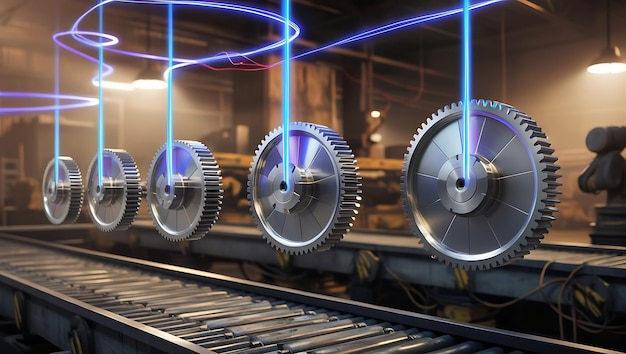
In the competitive landscape of metal processing, the demand for precision and efficiency has never been higher, particularly in the realm of heavy gauge steel slitting. Manufacturers are increasingly reliant on advanced technologies that not only meet but exceed their rigorous specifications. This article delves into the intricacies of heavy gauge steel slitting, examining the latest innovations, methodologies, and the critical role of automation in enhancing productivity and quality
Understanding Heavy Gauge Steel Slitting
Heavy gauge steel slitting is a specialized process that involves cutting large coils of steel into narrower strips with exceptional accuracy. The thickness of the material can vary significantly, typically ranging from 0.006 inches to 0.75 inches. The slitting process is crucial for industries that require specific dimensions for further processing, such as automotive, construction, and manufacturing.
The Importance of Precision
Precision is paramount in heavy gauge steel slitting. Even minor deviations in width or gauge can lead to significant issues downstream, including material rejection and increased costs. Manufacturers expect their raw materials to arrive with clean edges and consistent dimensions, minimizing the need for additional processing.
Key Challenges
The slitting process faces several challenges, including:
- Material Variability: Variations in material properties can affect cutting performance.
- Tooling Wear: The wear and tear of slitting blades can compromise edge quality.
- Downtime: Manual setups and adjustments can lead to inefficient operations.
Technological Innovations in Slitting
Recent advancements in slitting technology have transformed the industry, enabling manufacturers to achieve higher levels of efficiency and accuracy.
Automated Slitting Systems
Automated slitting systems have emerged as game-changers. These systems utilize robotics and advanced software to streamline the setup and operation of slitting lines. By automating the tooling assembly, manufacturers can significantly reduce downtime and minimize human error.
Double Eccentric Slitting Heads
One of the most notable innovations is the introduction of double eccentric slitting heads. These heads allow for precise cutting of materials with varying tensile strengths, ensuring that edge quality is maintained even under challenging conditions. The design enables consistent penetration and reduces the risk of strip burrs.
Hydraulic Locking Systems
Hydraulic systems have been integrated into slitting machinery to provide consistent pressure during the cutting process. This technology ensures that tooling remains securely in place, enhancing the overall accuracy of the cuts. The ability to adjust pressure settings remotely allows for greater flexibility in handling different materials.
The Role of Automation in Enhancing Efficiency
Automation plays a pivotal role in modern slitting operations. By reducing manual intervention, companies can achieve higher throughput and lower operational costs.
Preprogrammed Setups
Preprogrammed setups allow operators to switch between different slitting configurations quickly. This feature is particularly beneficial in environments where multiple materials are processed, as it minimizes the time spent on retooling.
Real-Time Monitoring
Advanced monitoring systems provide real-time data on the performance of slitting lines. By analyzing metrics such as speed, pressure, and blade wear, manufacturers can make informed decisions to optimize their processes.
Robotics in Tooling Assembly
Robotic arms are increasingly being used to handle tooling assembly and disassembly. This innovation not only speeds up the process but also reduces the risk of injuries associated with manual handling.
Quality Control Measures
Maintaining high-quality standards is essential in heavy gauge steel slitting. Manufacturers must implement rigorous quality control measures to ensure that the final product meets customer specifications.
Edge Quality Assessment
Regular assessments of edge quality are crucial. This can involve visual inspections and measurements to ensure that the edges are clean and free from defects. Automated systems can assist in this process by providing consistent evaluations.
Tolerance Management
Tolerance management is critical in slitting operations. Advanced machinery can achieve tolerances as tight as 0.002 millimeters, ensuring that each strip meets the exact requirements for further processing.
Feedback Loops
Implementing feedback loops allows manufacturers to continuously improve their processes. By analyzing production data, companies can identify areas for enhancement and implement corrective measures promptly.
Benefits of High Efficiency in Slitting Operations
Achieving high efficiency in slitting operations offers numerous benefits, ranging from cost savings to improved product quality.
Cost Reduction
By minimizing downtime and optimizing material usage, manufacturers can significantly reduce operational costs. Efficient slitting processes lead to less waste and lower energy consumption.
Enhanced Productivity
Automated systems and advanced technologies contribute to higher productivity levels. Manufacturers can achieve greater output without compromising on quality, enabling them to meet increasing market demands.
Improved Customer Satisfaction
Delivering high-quality products on time is essential for customer satisfaction. Efficient slitting operations allow manufacturers to fulfill orders more reliably, fostering long-term relationships with clients.
Future Trends in Heavy Gauge Steel Slitting
As technology continues to evolve, several trends are shaping the future of heavy gauge steel slitting.
Integration of AI and Machine Learning
Artificial intelligence and machine learning are set to revolutionize slitting operations. These technologies can analyze vast amounts of data to optimize processes and predict maintenance needs, leading to even greater efficiencies.
Sustainable Practices
Sustainability is becoming a focal point for manufacturers. Implementing eco-friendly practices, such as reducing waste and energy consumption, is essential in meeting regulatory requirements and consumer expectations.
Customization of Solutions
The demand for customized solutions is on the rise. Manufacturers are increasingly looking for slitting systems that can handle a variety of materials and thicknesses, allowing for greater flexibility in production.
Conclusion
The landscape of heavy gauge steel slitting is rapidly evolving, driven by technological advancements and the relentless pursuit of efficiency and accuracy. As manufacturers embrace automation and innovative solutions, they are better equipped to meet the demands of an ever-changing market. By focusing on quality control, operational efficiency, and future trends, the industry is poised for continued growth and success.
This article provides a comprehensive overview of heavy gauge steel slitting, emphasizing the importance of precision, the role of automation, and the benefits of high efficiency. Each section is crafted to enhance readability and engagement, ensuring that readers gain valuable insights into the topic.