How Coil Thickness Affects Metal Fabrication and Steel Slitting Efficiency
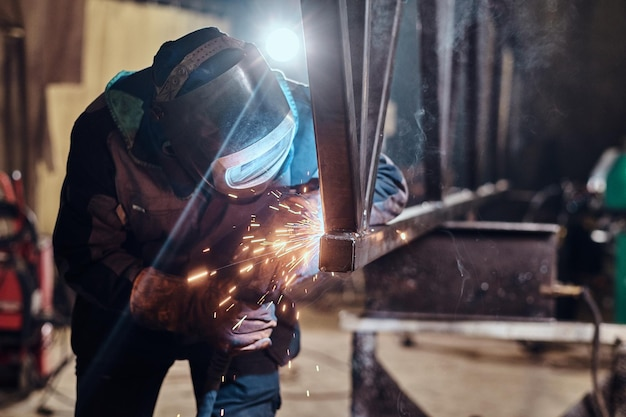
When it comes to metal fabrication and steel slitting, the thickness of the coil plays a pivotal role in determining the overall efficiency and effectiveness of the processes involved. Understanding how coil thickness influences various aspects of metalworking can significantly impact production quality, cost, and operational efficiency. This article delves into the multifaceted relationship between coil thickness and its effects on metal fabrication and steel slitting, exploring key concepts, processes, and applications
Coil thickness refers to the measurement of the metal material’s width, typically expressed in gauges or millimeters. This measurement is crucial as it affects the mechanical properties of the material, influencing its suitability for various applications.
Importance of Coil Thickness
- Mechanical Properties: The thickness of the coil directly affects its strength, flexibility, and durability. Thicker materials often provide greater strength but may sacrifice flexibility, making them less suitable for certain applications.
- Material Usage: Different industries require specific thicknesses for optimal performance. For instance, automotive applications may demand thinner sheets for body panels, while construction might favor thicker materials for structural components.
- Cost Implications: Thicker coils generally incur higher production and shipping costs due to the increased weight and material usage. Understanding the necessary thickness can help manufacturers optimize their budgets.
Measurement Techniques
Coil thickness is typically measured using various methods, including:
- Micrometers: A precision instrument that measures small distances, often used for precise thickness readings.
- Ultrasonic Thickness Gauges: Non-destructive testing tools that use sound waves to measure thickness without damaging the material.
- Calipers: A versatile tool that can measure internal and external dimensions, including thickness.
The Role of Coil Thickness in Metal Fabrication
Metal fabrication encompasses a range of processes, including cutting, bending, and assembling materials. The thickness of the coil significantly influences these operations.
Cutting Processes
- Shearing: For thinner coils, shearing is often the preferred method. The efficiency of this process relies on the material’s thickness, as thicker sheets may require specialized equipment to handle the increased resistance during cutting.
- Laser Cutting: This method offers precision and versatility. However, the thickness of the coil can limit the maximum cutting speed and the quality of the cut edges. Thinner materials generally yield cleaner cuts and faster processing times.
- Plasma Cutting: While effective for various thicknesses, plasma cutting is particularly advantageous for thicker materials, allowing for quick and efficient cuts without compromising the integrity of the material.
Bending and Forming
- Bending Techniques: The thickness of the coil influences the choice of bending techniques. Thicker materials may require more powerful machinery and specialized dies to achieve the desired bend radius.
- Roll Forming: This process is highly dependent on coil thickness. Thicker coils may necessitate adjustments in speed and pressure to ensure uniformity and prevent defects during the forming process.
- Stamping: The thickness of the coil impacts the stamping process, affecting the force required for successful forming. Thinner materials are often easier to stamp, while thicker sheets may require more complex setups.
Steel Slitting Efficiency and Coil Thickness
Steel slitting is a process that involves cutting wide coils into narrower strips, tailored to specific customer requirements. The efficiency of this process is heavily influenced by the thickness of the coil.
Customization and Precision
- Tailored Widths: Coil slitting allows for precise customization of strip widths. Thicker coils may limit the range of achievable widths, as the cutting equipment may not be designed to handle extreme variations.
- Tolerances: Achieving tight tolerances is essential in many applications. Thicker coils may pose challenges in maintaining consistent tolerances due to the increased difficulty in cutting and handling.
- Edge Quality: The quality of the edges produced during slitting is critical. Thicker materials may result in rougher edges, necessitating additional processing steps to achieve the desired finish.
Efficiency and Waste Reduction
- Material Utilization: Thinner coils can optimize material usage, reducing waste during the slitting process. Manufacturers can achieve more strips from a single coil, enhancing overall efficiency.
- Production Speed: The thickness of the coil can impact the speed of the slitting process. Thinner materials often allow for faster processing times, leading to improved turnaround for customers.
- Cost Efficiency: By minimizing waste and maximizing production speed, manufacturers can achieve significant cost savings. Understanding the ideal thickness for specific applications can lead to better financial outcomes.
Industry-Specific Applications
Different industries utilize coil thickness in various ways, tailoring their processes to meet specific needs.
Automotive Industry
- Body Panels: Thinner coil sheets are often used for manufacturing body panels, where lightweight materials contribute to fuel efficiency without compromising safety.
- Chassis Components: Thicker materials are essential for structural components, providing the strength needed to withstand stresses and strains during operation.
- Customization: Automotive manufacturers often require precise thickness specifications to meet safety standards and performance requirements.
Construction Sector
- Structural Elements: In construction, thicker coil sheets are commonly used for beams, columns, and other load-bearing structures, ensuring durability and stability.
- Roofing and Siding: Thinner materials may be preferred for roofing and siding applications, where flexibility and ease of installation are paramount.
- Environmental Considerations: The choice of coil thickness can also be influenced by environmental factors, such as weather conditions and building codes.
Aerospace Applications
- Lightweight Materials: The aerospace industry often employs aluminum coil sheets due to their lightweight nature, enhancing fuel efficiency and performance.
- Corrosion Resistance: Stainless steel coil sheets are used in applications requiring high corrosion resistance, especially in harsh environments.
- Precision Engineering: Aerospace components demand high precision, making the choice of coil thickness critical to achieving the necessary tolerances.
Challenges and Considerations
While understanding coil thickness is essential, various challenges can arise during metal fabrication and steel slitting.
Material Selection
- Performance Requirements: Choosing the right thickness is crucial for ensuring optimal performance. Factors such as load-bearing capacity, environmental conditions, and application-specific requirements must be considered.
- Cost Implications: Thicker materials may incur higher costs, necessitating a balance between budget constraints and performance needs.
- Supplier Reliability: Working with reputable suppliers ensures access to high-quality materials that meet specific thickness requirements.
Precision in Fabrication
- Consistency: Achieving consistent thickness throughout the coil is vital for maintaining quality during fabrication. Variations can lead to defects and compromised structural integrity.
- Calibration: Regular calibration of cutting and forming equipment is necessary to accommodate variations in coil thickness, ensuring precision and efficiency.
- Training and Expertise: Skilled operators are essential for handling different thicknesses effectively, minimizing errors during the fabrication process.
Innovations in Coil Processing
Advancements in technology continue to shape the way manufacturers approach coil thickness and processing.
Automation and Robotics
- Automated Cutting Systems: The integration of automated cutting systems enhances precision and efficiency, allowing for faster processing of various coil thicknesses.
- Robotics in Bending: Robotic systems can adapt to different coil thicknesses, providing flexibility and consistency in bending operations.
- Data Analytics: Leveraging data analytics can help manufacturers optimize their processes, identifying the ideal thickness for specific applications based on historical performance.
Material Science Developments
- Advanced Alloys: Innovations in material science have led to the development of advanced alloys that offer improved strength-to-weight ratios, allowing for thinner materials without compromising performance.
- Surface Treatments: New surface treatments can enhance the properties of coil sheets, improving corrosion resistance and durability while maintaining desired thickness specifications.
- Sustainability Initiatives: The push for sustainable practices has led to the exploration of recycled materials, influencing the choice of coil thickness and its impact on environmental footprint.
Future Trends in Coil Thickness and Metal Fabrication
As industries evolve, so too will the considerations surrounding coil thickness and its impact on metal fabrication and steel slitting.
Sustainability and Eco-Friendly Practices
- Recycled Materials: The use of recycled coil sheets can influence thickness specifications, promoting sustainability while maintaining performance.
- Energy Efficiency: Manufacturers are increasingly focusing on energy-efficient processes, optimizing coil thickness to reduce energy consumption during fabrication.
- Regulatory Compliance: Adhering to environmental regulations will shape the future of coil thickness specifications, encouraging the use of eco-friendly materials.
Customization and Flexibility
- Tailored Solutions: The demand for customized products will drive the need for flexible coil thickness options, allowing manufacturers to meet specific customer requirements.
- Rapid Prototyping: Advances in prototyping technologies will enable quicker adjustments to coil thickness, streamlining the design and manufacturing process.
- Market Adaptability: Manufacturers must remain adaptable to changing market demands, ensuring their processes can accommodate varying coil thickness requirements.
Conclusion
Coil thickness significantly influences metal fabrication and steel slitting efficiency, impacting everything from production costs to product quality. By understanding the nuances of coil thickness and its implications across various processes and industries, manufacturers can optimize their operations, improve efficiency, and ultimately deliver superior products. As technology evolves and industries adapt, staying informed about the latest trends and innovations will be crucial for maintaining a competitive edge in the metalworking landscape.
This article provides a comprehensive overview of how coil thickness affects metal fabrication and steel slitting efficiency. If you have any specific requests for further details or sections, feel free to ask!