The Fundamentals of Precision Steel Processing in Modern Slitting Lines
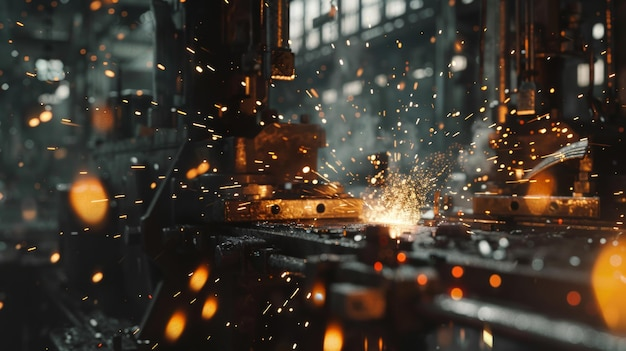
In today’s manufacturing landscape, the ability to process steel with precision is paramount. Slitting lines serve as the backbone of this process, transforming wide coils of metal into narrower strips tailored for various applications. From automotive components to household items, the slitting process plays a crucial role in ensuring that the right materials are available for production. This article explores the fundamentals of precision steel processing within modern slitting lines, diving into the intricacies of the machinery, techniques, and best practices that define this essential industry
Understanding Slitting Lines
What is a Slitting Line?
A slitting line is a specialized system designed to cut wide rolls of metal into narrower strips, often referred to as mults. The process begins with unwinding a large coil, which is then fed through a series of rotating knives that slice the metal into the desired widths. The resulting strips are rewound into coils, ready for further processing or direct use in manufacturing.
Importance of Slitting Lines
Slitting lines are integral to various manufacturing sectors, providing several advantages:
- Efficiency: By converting large coils into narrower strips, slitting lines maximize material usage and minimize waste.
- Precision: Advanced slitting technology ensures that cuts are made with high accuracy, which is vital for applications requiring exact specifications.
- Versatility: Slitting lines can handle a wide range of materials, including steel, aluminum, and copper, making them adaptable to different industry needs.
Key Components of a Slitting Line
Overview of Components
A slitting line comprises several critical components, each playing a vital role in the slitting process. Understanding these components is essential for optimizing performance and ensuring high-quality output.
1. Coil Car
The coil car is responsible for transporting heavy coils from storage to the uncoiler. It ensures that coils are loaded smoothly and positioned correctly for the next steps in the process.
2. Uncoiler
The uncoiler holds the large coil and unwinds it steadily, feeding the metal strip into the slitting line. This component is often equipped with a snubber roll to maintain proper tension and prevent any snags during unwinding.
3. Peeler Table
The peeler table initiates the unwinding process by lifting the edge of the coil and guiding it into the pinch rolls, ensuring a seamless transition into the slitting phase.
4. Pinch Rolls and Straightener
Pinch rolls grip the metal strip and pull it through the line, while the straightener removes any bends or twists, ensuring that the strip is flat and properly aligned before reaching the slitter head.
5. Loop Control System
To maintain consistent tension and speed, the loop control system creates a loop of metal between the uncoiler and the slitter. This prevents material from snapping or stretching, facilitating a smooth operation.
6. Slitter Head
The slitter head is the heart of the slitting line, featuring rotary knives that cut the metal into strips with precision. The configuration of the knives can be adjusted to accommodate various widths and thicknesses.
7. Scrap Winder
As edge trims are produced during the slitting process, the scrap winder collects this material, winding it into manageable coils for disposal or recycling.
8. Tension Stand
The tension stand ensures that the slit strips remain taut and correctly aligned as they are fed towards the recoiler, minimizing the risk of defects.
9. Recoiler
After slitting, the recoiler rewinds each strip into individual coils. This component is crucial for organizing the output and preparing it for transport or further processing.
10. Exit Coil Car
Similar to the entry coil car, the exit coil car transports the finished coils from the recoiler to the storage area, completing the slitting process.
The Slitting Process Explained
Step-by-Step Breakdown
The slitting process can be divided into several detailed steps, each contributing to the overall effectiveness of the operation.
1. Loading the Coil
The process commences with loading a large metal coil onto the coil car, which then transports it to the uncoiler for positioning.
2. Unwinding and Peeling
Once secured, the uncoiler unwinds the coil, feeding the metal strip into the peeler table, where the edge is lifted for guiding into the pinch rolls.
3. Pinching and Straightening
The pinch rolls grip the strip, pulling it through the straightener, which flattens the strip and removes any imperfections, ensuring proper alignment.
4. Creating a Loop
The loop control system forms a loop of material between the uncoiler and the slitter head, absorbing fluctuations in speed or tension, thus maintaining a continuous process.
5. Slitting
As the metal strip passes through the slitter head, the rotary knives precisely cut it into narrower strips. The arrangement of the knives can be adjusted based on the required specifications.
6. Scrap Winding
Edge trims generated during the slitting are collected by the scrap winder, which organizes them into coils for recycling or disposal.
7. Tension Control
The tension stand ensures that the slit strips remain taut and aligned as they move towards the recoiler, maintaining quality throughout the process.
8. Recoiling
The slit strips are rewound into individual coils by the recoiler, preparing them for the next stage of production or distribution.
9. Unloading
Finally, the finished coils are transferred from the recoiler to the exit coil car, which transports them to storage.
Factors Influencing Precision in Slitting
Material Characteristics
Understanding the properties of the steel being processed is crucial for achieving optimal results. Factors such as tensile strength, hardness, and surface finish play significant roles in configuring the slitting parameters.
Tooling and Blade Selection
The blades and tooling used during the slitting process are critical for precision. Regular inspections and timely replacements are essential to ensure smooth operations and high-quality cuts.
Automation and Technology
Embracing automation technologies can significantly enhance the efficiency and accuracy of slitting lines. Advanced systems reduce human error and streamline operations, allowing for faster turnaround times.
Safety Protocols
Prioritizing safety in the slitting process is essential. Implementing safety features, conducting regular training sessions, and familiarizing operators with emergency protocols can help maintain a secure working environment.
Best Practices for Optimizing Slitting Operations
Regular Maintenance
Conducting routine maintenance on slitting line components can prevent unexpected breakdowns and ensure consistent performance. Key areas to focus on include:
- Blade sharpness and condition
- Tension control systems
- Loop control mechanisms
Training and Skill Development
Investing in operator training is vital for maximizing the efficiency of slitting lines. Regular workshops and skill development programs can ensure that staff are well-versed in best practices and safety protocols.
Data Monitoring and Analysis
Utilizing data analytics to monitor slitting operations can provide valuable insights into performance metrics. This information can help identify areas for improvement and enhance overall productivity.
Customization Options
Working with manufacturers to customize slitting lines based on specific production needs can lead to improved efficiency and output quality. Tailoring components to accommodate unique material properties can result in better performance.
The Future of Slitting Lines
Innovations in Technology
The future of slitting lines is poised for significant advancements. Innovations such as AI-driven automation, predictive maintenance, and enhanced material handling systems are set to redefine the industry.
Sustainability Practices
As industries increasingly focus on sustainability, slitting lines will need to adapt. Implementing eco-friendly practices, such as recycling edge trims and optimizing energy consumption, will become essential.
Integration with Industry 4.0
The integration of slitting lines with Industry 4.0 technologies will facilitate smarter manufacturing processes. Real-time data sharing and connectivity will enhance coordination and efficiency across production lines.
Conclusion
Mastering the fundamentals of precision steel processing within modern slitting lines is essential for meeting the demands of contemporary manufacturing. By understanding the intricacies of slitting lines, from their components to the slitting process itself, manufacturers can unlock the full potential of their operations. Embracing best practices, harnessing technological innovations, and prioritizing safety will ensure that slitting lines continue to play a vital role in the future of metal processing.
This article provides a comprehensive overview of precision steel processing in slitting lines, adhering to your specifications for structure, content, and SEO optimization. If you need further adjustments or additional sections, feel free to let me know!