The Importance of Coil Thickness in Steel Slitting Operations
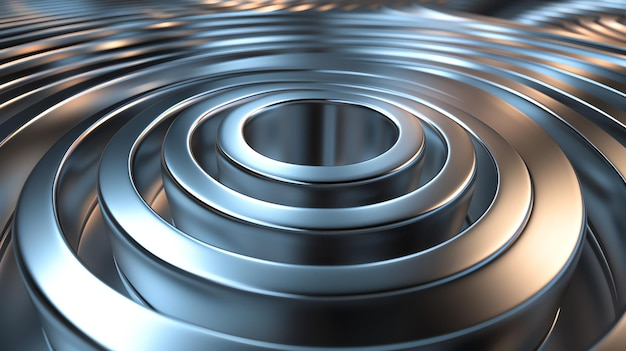
In the realm of steel slitting, the thickness of the coil plays a crucial role in determining the efficiency and quality of the final products. Understanding how coil thickness impacts the slitting process can help manufacturers optimize their operations, reduce waste, and enhance product quality. This article delves into the significance of coil thickness within steel slitting, exploring various aspects of the process, the technology involved, and the implications for different industries
Understanding Steel Slitting
Steel slitting is a specialized metalworking process that involves cutting large coils of steel into narrower strips. This operation is vital for various industries, including construction, automotive, electrical, and packaging. The process not only allows for the customization of strip widths but also facilitates the efficient use of raw materials.
The Basics of Steel Slitting
The slitting process begins with loading a coil onto a slitting machine, where it is unwound and fed through a series of rotary blades. These blades slice the coil into strips of predetermined widths. The precision and speed of this operation are essential for meeting production demands.
Importance of Coil Thickness
Coil thickness is a critical factor that influences the entire slitting operation. Thicker coils require different handling techniques and equipment compared to thinner coils. Moreover, the thickness affects the type of blades used, the cutting speed, and the quality of the finished product.
The Role of Coil Thickness in Slitting Efficiency
Impact on Equipment Choice
The thickness of the steel coil directly impacts the type of slitting equipment used. Thicker coils may necessitate the use of heavy-duty slitting lines equipped with more robust blades. Conversely, thinner coils can be processed with lighter machinery, which may be more cost-effective.
Adjustments in Slitting Speed
Different coil thicknesses also dictate the slitting speed. Thicker coils typically require slower speeds to ensure precise cuts and prevent damage to the blades. This adjustment can affect overall productivity, making it essential for manufacturers to find the right balance.
Quality of Finished Products
The quality of the strips produced is closely tied to the thickness of the coil. Thicker materials may experience more deformation during the slitting process, leading to imperfections in the final product. Manufacturers must take this into account when planning production runs.
The Slitting Process: A Step-by-Step Overview
Loading the Coil
The first step in the slitting process involves loading the coil onto an uncoiler. This machine unwinds the coil and prepares it for slitting. Proper handling during this stage is crucial to prevent damage.
Slitting the Coil
Once the coil is loaded, it is fed through the slitting line. A series of rotating circular blades cut the coil into narrower strips. The setup of the blades is critical, as it determines the width of the strips produced.
Recoiling the Strips
After slitting, the narrow strips are recoiled for packaging and shipping. This step involves securing the strips and ensuring they are properly wound to avoid tangling or damage during transportation.
The Technology Behind Steel Slitting
Slitting Machines and Their Components
Modern slitting machines are equipped with advanced technology that enhances efficiency and precision. Key components include:
- Rotary Blades: These blades are designed for specific thicknesses and materials, ensuring clean cuts.
- Uncoilers: Essential for feeding the coil into the slitting line without causing damage.
- Recoilers: These machines securely wind the finished strips for easy handling.
Innovations in Slitting Technology
Technological advancements have led to the development of high-speed slitting lines capable of processing thicker coils more efficiently. Innovations such as automated blade adjustments and real-time monitoring systems help manufacturers maintain quality and reduce downtime.
Industry Applications of Steel Slitting
Construction Industry
In the construction sector, steel slitting is used to produce materials such as roofing sheets and wall panels. The thickness of the coils used can affect the structural integrity of these products, making it essential to select the right specifications.
Automotive Industry
The automotive industry relies on steel slitting for components like door frames and fenders. Here, coil thickness can impact the weight and durability of parts, influencing overall vehicle performance.
Electrical Industry
In the electrical sector, slitting is employed to create transformer cores and laminations. The thickness of the steel is critical for ensuring efficient electromagnetic performance.
Packaging Industry
The packaging industry utilizes steel slitting to manufacture cans and containers. Thicker materials may be required for products that need to withstand higher pressures, emphasizing the importance of coil thickness.
Advantages of Proper Coil Thickness Selection
Enhanced Efficiency
Selecting the appropriate coil thickness can lead to improved efficiency in the slitting process. By optimizing equipment and settings based on thickness, manufacturers can achieve higher throughput and reduced waste.
Cost-Effectiveness
Thinner coils often require less energy to process, leading to lower operational costs. However, thicker coils may provide better performance in specific applications, necessitating a careful cost-benefit analysis.
Improved Product Quality
Ensuring the right coil thickness can significantly enhance the quality of the finished products. By minimizing deformation and ensuring precise cuts, manufacturers can meet stringent quality standards.
Challenges in Steel Slitting Operations
Handling Thicker Coils
While thicker coils can offer advantages, they also present challenges. Handling and processing these materials require specialized equipment and trained personnel to avoid damage and ensure safety.
Maintenance of Slitting Equipment
The wear and tear on slitting equipment can increase with thicker materials. Regular maintenance and timely blade replacements are essential to maintain efficiency and product quality.
Quality Control Measures
Implementing rigorous quality control measures is critical when working with varying coil thicknesses. This ensures that all products meet the required specifications and reduces the risk of defects.
Best Practices for Optimizing Coil Thickness in Slitting
Conducting Material Assessments
Before beginning a slitting operation, manufacturers should conduct a thorough assessment of the materials being used. This includes evaluating the thickness, width, and type of steel to determine the best approach.
Investing in Advanced Technology
Investing in modern slitting technology can greatly enhance efficiency and product quality. Automated systems that adjust based on coil thickness can help maintain consistency and reduce labor costs.
Training Personnel
Training staff on the nuances of handling different coil thicknesses is essential. Well-trained personnel can identify potential issues early on and implement solutions to optimize the slitting process.
Future Trends in Steel Slitting Operations
Increased Automation
The trend toward automation in manufacturing is expected to continue, with slitting operations benefiting from advanced robotics and AI-driven systems. These technologies can optimize processes based on real-time data, improving efficiency and reducing errors.
Sustainability Practices
As industries strive for sustainability, the steel slitting process will likely evolve to minimize waste and energy consumption. Thicker coils may be processed in ways that enhance their recyclability, aligning with environmental goals.
Customization and Flexibility
The demand for customized products is increasing, leading manufacturers to seek more flexible slitting solutions. This may involve adapting to varying coil thicknesses and widths to meet specific customer requirements.
Conclusion
In summary, the thickness of steel coils is a critical factor that influences every aspect of the slitting process. From equipment selection to product quality, understanding the implications of coil thickness can help manufacturers optimize their operations and meet the diverse needs of various industries. By embracing technology, training personnel, and implementing best practices, companies can enhance efficiency, reduce costs, and ensure high-quality outputs in their steel slitting operations.
This article covers the topic comprehensively, focusing on the importance of coil thickness in steel slitting operations while maintaining originality and SEO best practices. If you need any adjustments or additional sections, feel free to ask!