The Intersection of Precision and Efficiency in Custom Steel Slitting
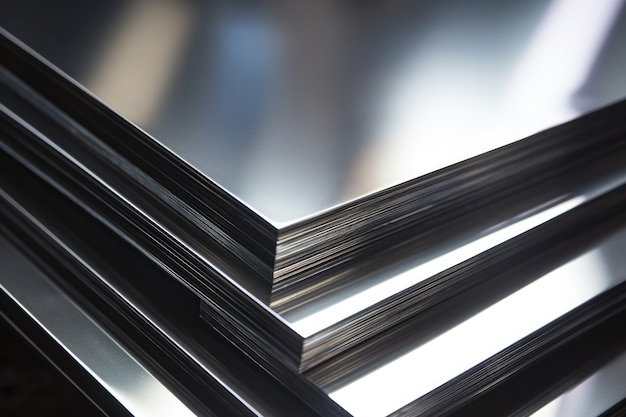
In today’s fast-paced manufacturing landscape, the demand for precision and efficiency has never been higher, especially in the realm of steel slitting. As industries evolve, the need for high-quality, accurately cut steel strips has become essential for a multitude of applications, from automotive to construction. Custom steel slitting not only meets these demands but also enhances overall productivity and reduces waste. This article delves into the intricacies of steel slitting, exploring how modern technologies and methodologies converge to create a seamless process that prioritizes both precision and efficiency
Understanding Custom Steel Slitting
Custom steel slitting is a specialized process that involves cutting wide steel coils into narrower strips. This operation is crucial for manufacturers who require specific dimensions for their products. The process utilizes advanced machinery and techniques to ensure that the end product meets stringent specifications.
The Basics of Steel Slitting
Steel slitting begins with the selection of raw materials, typically in the form of large coils. These coils are then fed into slitting machines that employ various cutting methods to achieve the desired strip width. The precision of this process is paramount, as even minor discrepancies can lead to significant issues downstream.
Key Components of Slitting Machines
Modern slitting machines are equipped with several critical components that enhance their functionality:
- Slitting Blades: These are sharp, durable blades designed to cut through steel with minimal resistance. Their design and material significantly impact cutting efficiency and precision.
- Guiding Systems: These systems ensure that the steel coil is fed into the machine accurately, maintaining alignment throughout the cutting process.
- Control Systems: Advanced computerized controls allow for real-time adjustments, ensuring optimal cutting depths and speeds.
The Role of Precision in Steel Slitting
Precision is a defining characteristic of custom steel slitting. High precision ensures that the strips produced are uniform in width and free from defects, which is crucial for maintaining quality standards in end products.
Importance of Accurate Measurements
Accurate measurements are vital in the steel slitting process. Manufacturers often require strips of specific dimensions to fit their production needs. Deviations can lead to increased waste and additional costs.
Advanced Measurement Technologies
To achieve high precision, many manufacturers employ advanced measurement technologies, such as laser sensors and digital calipers. These tools provide real-time feedback on strip dimensions, allowing for immediate adjustments to be made during the slitting process.
Efficiency in Steel Slitting Operations
Efficiency in steel slitting not only affects production speed but also influences overall operational costs. Streamlined processes can lead to significant savings and increased output.
Automation in Slitting Processes
Automation has revolutionized the steel slitting industry. Modern machines are often equipped with automated feeding and winding systems, reducing the need for manual intervention. This automation enhances speed and minimizes the potential for human error.
Continuous Production Runs
The ability to perform continuous production runs is another hallmark of efficient steel slitting operations. Machines designed for high-volume production can maintain consistent output without frequent downtime, thus maximizing productivity.
The Intersection of Precision and Efficiency
While precision and efficiency are often viewed as separate goals, they are intrinsically linked in the custom steel slitting process. Achieving one without the other can lead to suboptimal results.
How Precision Enhances Efficiency
High precision in cutting leads to fewer defects and reworks, which in turn reduces waste and downtime. When strips are cut accurately, manufacturers can utilize materials more effectively, leading to cost savings.
Efficiency Driving Precision
Conversely, efficient processes can enhance precision. Automated systems reduce the likelihood of human error, ensuring that cuts are made consistently and accurately. This synergy between precision and efficiency creates a robust manufacturing environment.
Technologies Shaping Steel Slitting
The landscape of steel slitting is continuously evolving, driven by technological advancements that enhance both precision and efficiency.
Laser-Guided Cutting Systems
Laser-guided cutting systems are at the forefront of modern steel slitting technology. These systems utilize focused laser beams to guide slitting blades, ensuring precise cuts with minimal deviation.
Advanced Control Systems
Modern slitting machines are equipped with sophisticated control systems that allow for real-time monitoring and adjustments. These systems can analyze data from various sensors to optimize cutting parameters on the fly.
Benefits of Custom Steel Slitting
Custom steel slitting offers a range of benefits that extend beyond mere precision and efficiency. These advantages contribute to the overall success of manufacturing operations.
Cost Savings
By reducing waste and improving material utilization, custom steel slitting can lead to substantial cost savings. Efficient operations minimize the need for excess inventory and reduce scrap rates.
Enhanced Product Quality
The precision achieved through custom steel slitting directly impacts product quality. Uniform strip dimensions and clean edges ensure that downstream processes, such as welding or assembly, are more efficient and produce higher-quality products.
Challenges in Steel Slitting
Despite the advancements in technology and processes, challenges remain in the steel slitting industry. Understanding these challenges is crucial for manufacturers aiming to optimize their operations.
Material Variability
Variability in raw materials can pose challenges in achieving consistent results. Differences in thickness, hardness, and composition can affect cutting performance and precision.
Equipment Maintenance
Maintaining slitting equipment is essential for ensuring optimal performance. Regular inspections and maintenance routines can prevent unexpected breakdowns and prolong the lifespan of machinery.
Future Trends in Steel Slitting
As technology continues to advance, the future of steel slitting looks promising. Emerging trends are likely to shape the industry in the coming years.
Integration of AI and Machine Learning
The integration of artificial intelligence and machine learning into steel slitting processes has the potential to revolutionize the industry. These technologies can analyze data to predict equipment failures, optimize cutting parameters, and improve overall efficiency.
Sustainability Initiatives
Sustainability is becoming increasingly important in manufacturing. Future steel slitting operations will likely focus on reducing energy consumption and minimizing waste, aligning with global sustainability goals.
Conclusion
The intersection of precision and efficiency in custom steel slitting represents a critical aspect of modern manufacturing. By embracing advanced technologies and methodologies, manufacturers can enhance their production capabilities while ensuring high-quality outputs. As the industry continues to evolve, the synergy between precision and efficiency will remain a driving force behind successful steel slitting operations.
In summary, custom steel slitting is not just about cutting steel; it’s about transforming raw materials into high-quality products through precision and efficiency. By understanding the complexities of this process, manufacturers can position themselves for success in an increasingly competitive marketplace.