The Pivotal Role of Coil Thickness in Optimizing Steel Coil Slitting Operations
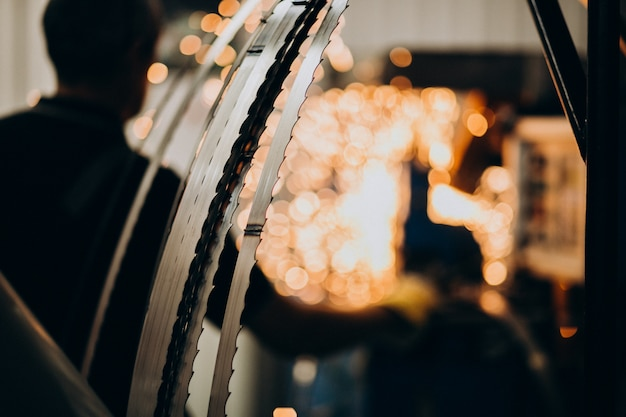
Introduction
Steel coil slitting is a fundamental process in the metals industry, allowing manufacturers to transform wide master coils into narrower, customized strips or sheets. However, the thickness of the steel coil plays a pivotal role in determining the efficiency and effectiveness of the slitting operation. In this comprehensive article, we will delve into the intricacies of coil thickness and its far-reaching implications on the steel slitting process, equipping you with the knowledge to make informed decisions and optimize your operations.
Understanding Coil Thickness: The Cornerstone of Slitting
The thickness of a steel coil, also known as the gauge, is a critical parameter that directly impacts the slitting process. Coil thickness can range from as thin as 0.010 inches to as thick as 0.500 inches, with each range presenting unique challenges and considerations for the slitting operation.
Thin Gauge Coils: Precision and Finesse
Thin gauge steel coils, typically ranging from 0.010 to 0.187 inches, require a delicate approach during the slitting process. These materials are more susceptible to deformation, warping, and edge damage if not handled with the utmost care. Slitting thin gauge coils demands precision tooling, tight tolerances, and experienced operators to ensure clean, consistent slit edges without compromising the material’s integrity.
Thick Gauge Coils: Strength and Stability
On the other end of the spectrum, thick gauge steel coils, ranging from 0.188 to 0.500 inches, present their own set of challenges. These robust materials require specialized slitting equipment and techniques to overcome the increased resistance and cutting force required. Proper setup, blade selection, and tension control are crucial to achieving accurate slit widths and maintaining the desired surface finish.
Slitting Thin Gauge Coils: Navigating the Challenges
Slitting thin gauge steel coils requires a meticulous approach to ensure optimal results. Let’s explore the key considerations and best practices for handling these delicate materials.
Precise Tooling and Setup
Thin gauge coils demand the use of high-precision slitting knives, carefully calibrated to maintain tight width tolerances and minimize material deformation. The slitting arbors and guides must be meticulously aligned to ensure a smooth, consistent feed of the material through the cutting zone.
Tension Control: The Balancing Act
Maintaining the right level of tension is crucial when slitting thin gauge coils. Excessive tension can lead to tearing or edge cracking, while insufficient tension can result in waviness or uneven slit edges. Skilled operators must continuously monitor and adjust the tension throughout the slitting process to strike the perfect balance.
Specialized Handling and Packaging
Thin gauge steel coils are more susceptible to damage during handling and transportation. Robust packaging solutions, such as reinforced cores and specialized coil protection, are necessary to safeguard the material and maintain its quality during the supply chain journey.
Slitting Thick Gauge Coils: Overcoming the Challenges
Thick gauge steel coils present a unique set of challenges that require specialized equipment and techniques to overcome. Let’s explore the key considerations for effective thick gauge slitting.
Heavy-Duty Slitting Equipment
Slitting thick gauge coils demands the use of robust, high-capacity slitting machinery capable of generating the necessary cutting force and power. These specialized lines often feature heavy-duty arbors, powerful drives, and reinforced components to handle the increased material thickness and resistance.
Blade Selection and Maintenance
Selecting the appropriate slitting knives for thick gauge coils is crucial. Carbide-tipped blades with a greater depth of cut are typically employed to penetrate the thicker material efficiently. Proper maintenance and regular blade sharpening are essential to ensure consistent, clean slit edges throughout the production run.
Coil Handling and Feeding
Thick gauge coils are inherently heavier and more unwieldy than their thin counterparts. Specialized coil handling equipment, such as high-capacity cranes and decoilers, is necessary to safely load and feed the material into the slitting line. Careful attention must be paid to the coil’s entry angle and tension to prevent any issues during the slitting process.
Optimizing Coil Thickness for Efficient Slitting
Achieving optimal slitting performance requires a holistic approach that considers the interplay between coil thickness and the slitting process. Let’s explore strategies for optimizing coil thickness to enhance slitting efficiency.
Material Selection and Specification
When sourcing steel coils for slitting, it’s essential to work closely with suppliers to select the appropriate coil thickness that aligns with your production capabilities and end-use requirements. This collaborative approach ensures that the material characteristics are well-suited for the slitting operation, minimizing the risk of issues and maximizing productivity.
Slitting Line Versatility
Investing in slitting lines with the flexibility to handle a wide range of coil thicknesses can significantly enhance operational efficiency. Such versatile equipment, equipped with adjustable components and interchangeable tooling, enables seamless transitions between thin and thick gauge coils, reducing downtime and maximizing throughput.
Operator Training and Skill Development
The human element plays a crucial role in the success of coil slitting operations. Comprehensive training programs for slitting line operators, focusing on techniques for handling different coil thicknesses, troubleshooting, and process optimization, can significantly improve the overall efficiency and quality of the slitting process.
Coil Thickness and its Impact on Downstream Processes
The thickness of the slit steel coils not only affects the slitting operation itself but also has far-reaching implications on downstream manufacturing processes and end-use applications.
Stamping and Forming Considerations
The precision and consistency of slit edges are critical for stamping and forming operations. Thin gauge coils, when slit with high accuracy, can be directly fed into automated stamping presses or CNC machining centers, minimizing the need for additional secondary processing. Thick gauge coils, on the other hand, may require more extensive preparation, such as edge conditioning or leveling, to ensure optimal results in downstream manufacturing.
Corrosion Resistance and Surface Finish
The slitting process can have a significant impact on the surface finish and corrosion resistance of the steel. Thin gauge coils, when slit with clean, smooth edges, can maintain their corrosion-resistant properties and surface integrity, making them suitable for applications where appearance and weathering are paramount. Thick gauge coils, however, may require additional post-processing to address any potential surface defects or edge deformation introduced during slitting.
Material Utilization and Yield
The thickness of the slit coils also affects the material utilization and yield throughout the supply chain. Optimizing coil thickness can minimize material waste, reduce scrap, and improve overall resource efficiency, benefiting both the steel producer and the end-user.
The Future of Coil Thickness in Steel Slitting
As the industry continues to evolve, the role of coil thickness in steel slitting operations is expected to become even more crucial. Let’s explore some emerging trends and future developments in this domain.
Advancements in Slitting Technology
Ongoing research and development in slitting equipment and tooling are driving the industry towards enhanced precision, speed, and versatility. Innovations in areas like automated setup, real-time monitoring, and intelligent process control are poised to revolutionize the way coil thickness is managed and optimized during slitting operations.
Lightweight and High-Strength Materials
The growing demand for lightweight, high-strength steel materials in industries like automotive and aerospace is driving the need for more advanced slitting capabilities. Slitting lines capable of handling ultra-thin, high-tensile-strength coils with exceptional accuracy and edge quality will be increasingly sought after to meet the evolving market requirements.
Sustainability and Environmental Considerations
As the global focus on sustainability intensifies, the steel industry is under pressure to optimize resource utilization and minimize waste. Advancements in coil thickness management, coupled with improved material yield and reduced scrap generation, will play a pivotal role in enhancing the environmental sustainability of steel slitting operations.
Conclusion
The thickness of steel coils is a fundamental parameter that profoundly influences the efficiency, quality, and overall success of the slitting process. By understanding the unique challenges and best practices associated with thin and thick gauge coils, steel producers and processors can optimize their operations, enhance productivity, and deliver high-quality slit products to their customers.
As the industry continues to evolve, the role of coil thickness in steel slitting will become increasingly crucial, driving advancements in technology, material development, and sustainability initiatives. By staying ahead of these trends and adapting to the changing landscape, steel industry players can position themselves for long-term success and maintain a competitive edge in the global marketplace.