Understanding Steel Slitting Lines: Key Processes in Metal Processing
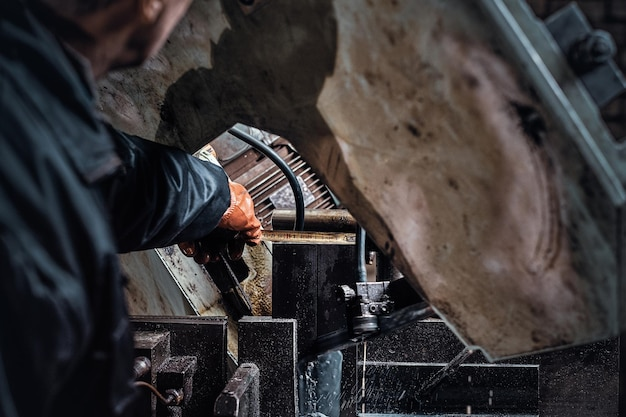
Steel slitting is an essential manufacturing process that plays a pivotal role in various industries, including automotive, construction, and appliance production. This intricate method involves slicing large coils of steel into narrower strips, known as mults, tailored to specific dimensions required by end-users. The entire operation hinges on a series of specialized machines and skilled operators, making it crucial for manufacturers to comprehend the nuances of steel slitting lines
What is Steel Slitting?
Steel slitting is a precise process where wide coils of steel are cut into narrower strips. This operation is vital for producing materials that meet specific requirements for various applications. The slitting process involves several key components, including decoilers, slitters, and recoilers, which work together to convert large rolls of steel into manageable, usable widths.
The Importance of Steel Slitting
Understanding steel slitting is essential for manufacturers, as it directly impacts the quality and efficiency of production. By mastering this process, companies can ensure that their metal components meet the necessary standards for strength and durability. Additionally, effective slitting can minimize waste and reduce costs, contributing to a more sustainable operation.
Applications of Slit Steel
Slit steel finds its way into numerous applications across various sectors. Some of the most common uses include:
- Automotive Components: Parts such as brackets, frames, and reinforcements.
- Construction Materials: Steel sheets and strips used in structural applications.
- Appliance Manufacturing: Components for refrigerators, ovens, and HVAC systems.
Types of Slitting Lines
Slitting lines come in various configurations, each designed to handle different materials and thicknesses. Understanding the types of slitting lines is crucial for selecting the right equipment for specific manufacturing needs.
Light Gauge Slitting Lines
Light gauge slitting lines are designed for processing thinner materials, such as stainless steel, aluminum, and tin plates. These machines are ideal for applications that require precision and finesse, allowing manufacturers to produce high-quality strips without compromising on performance.
Medium Gauge Slitting Lines
Medium gauge slitting lines cater to heavier materials and are equipped with additional features such as scrap winding and balling. These machines provide enhanced versatility, enabling manufacturers to handle a broader range of materials while maintaining quality.
Heavy Gauge Slitting Lines
Heavy gauge slitting lines are the most robust machines available, designed for heavy-duty industrial applications. These lines are capable of cutting high-strength metals and are essential for industries that require substantial material processing capabilities.
The Steel Slitting Process
The steel slitting process is a complex series of steps that require careful execution to ensure quality results. Here’s a breakdown of the key stages involved in the slitting operation.
1. Uncoiling the Steel Coil
The first step in the slitting process involves feeding the master coil onto the decoiler mandrel. The decoiler unwinds the coil, preparing it for the subsequent cutting stage. This step is critical as it sets the foundation for the entire operation.
2. Slitting the Steel
Once the coil is unwound, it is sent to the slitter head, where rotary knives slice the steel into narrow strips. The precision of this cutting process is paramount, as any deviations can lead to material waste and quality issues.
3. Inspection of Mults
After slitting, operators inspect the individual mults to ensure they meet the required specifications. This inspection involves checking the gauge width and edge condition, which are crucial for ensuring the strips are suitable for their intended applications.
4. Recoiling and Packaging
The slit strips then travel through a looping pit, which helps prevent stress and camber during recoiling. Once recoiled, the individual mults are banded and packaged according to customer requirements, ready for delivery.
The Role of Operators in Steel Slitting
Operators play a vital role in the steel slitting process. Their expertise and attention to detail are essential for ensuring that the machinery operates smoothly and that the final products meet quality standards.
Training and Experience
To effectively operate slitting lines, personnel must undergo extensive training. This training covers everything from machine operation to quality inspection, ensuring that operators are well-equipped to handle the complexities of the slitting process.
Safety Protocols
Safety is a top priority in steel processing facilities. Operators must adhere to strict safety protocols to minimize the risk of accidents. Regular safety training and equipment checks are essential for maintaining a secure working environment.
Knife Clearance and Precision
Knife clearance is a critical factor in achieving precise results in steel slitting. Understanding the importance of this parameter can significantly enhance the quality of the final product.
What is Knife Clearance?
Knife clearance refers to the space between the cutting edges of the rotary knives. Proper clearance is essential for ensuring that the knives cut through the material efficiently without causing damage or excessive wear.
Adjusting Knife Clearance
Each slitting project is unique, and operators may need to adjust knife clearance based on the specific material being processed. This adjustment often requires testing and fine-tuning to achieve optimal results.
Quality Control in Steel Slitting
Quality control is integral to the steel slitting process. Implementing rigorous quality assurance measures can help manufacturers maintain high standards and reduce material waste.
Inspection Procedures
Regular inspections of both the machinery and the finished products are crucial for identifying potential issues early in the process. Operators should be trained to recognize signs of wear or misalignment in the equipment, as well as defects in the slit strips.
Continuous Improvement
Manufacturers should adopt a culture of continuous improvement when it comes to quality control. By regularly reviewing processes and seeking feedback from operators, companies can identify areas for enhancement and implement changes that lead to better outcomes.
The Importance of Machinery Quality
Investing in high-quality slitting machinery is essential for ensuring precision and efficiency in the slitting process. The right equipment can make a significant difference in production outcomes.
Features to Look For
When selecting slitting machinery, manufacturers should consider several key features, including:
- Precision Cutting: Machines should be capable of delivering consistent, accurate cuts.
- Durability: Equipment should be built to withstand the rigors of industrial use.
- Ease of Maintenance: Machines that are easy to maintain can help minimize downtime.
Long-Term Benefits
Investing in quality machinery can lead to long-term benefits, including reduced scrap rates, improved production efficiency, and enhanced product quality.
Tool Maintenance and Care
Proper maintenance of tooling is crucial for ensuring the longevity and effectiveness of slitting machines. Neglecting this aspect can lead to performance issues and increased production costs.
Regular Inspections
Operators should conduct regular inspections of cutting tools to identify signs of wear or damage. Dull knives can lead to poor quality cuts and increased material waste, making it essential to address maintenance needs promptly.
Maintenance Practices
Implementing a routine maintenance schedule can help keep machinery and tooling in optimal condition. This schedule should include cleaning, sharpening, and replacing worn components as needed.
The Future of Steel Slitting
As technology continues to advance, the steel slitting process is likely to evolve. Manufacturers must stay abreast of industry trends to remain competitive.
Automation and Technology
The integration of automation and advanced technology in steel slitting lines has the potential to enhance production efficiency and reduce human error. Manufacturers should explore opportunities to incorporate these innovations into their operations.
Sustainability Initiatives
The push for sustainability is influencing the steel processing industry. Companies are increasingly seeking ways to reduce waste and energy consumption in their slitting operations, aligning with broader environmental goals.
Conclusion
Understanding the intricacies of steel slitting lines is essential for manufacturers aiming to optimize their production processes. By investing in quality machinery, ensuring proper operator training, and implementing rigorous quality control measures, companies can enhance their efficiency and deliver high-quality products. As the industry continues to evolve, staying informed about technological advancements and sustainability initiatives will be key to maintaining a competitive edge in the market.
This article provides a comprehensive overview of the steel slitting process, highlighting its importance and the factors that contribute to successful operations. By following best practices and embracing innovation, manufacturers can ensure they meet the demands of their respective industries while maintaining high standards of quality and efficiency.