Unlocking the Secrets of Precision Steel Processing: Exploring the Key Components of a Slitting Line
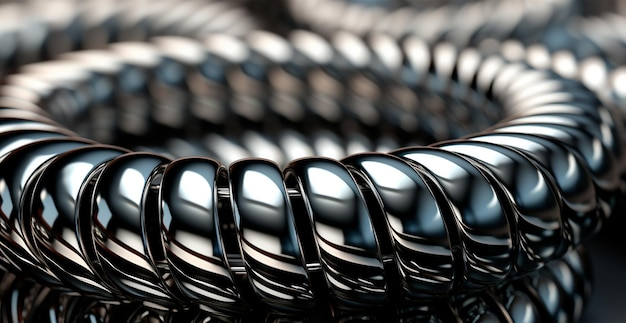
In the dynamic world of metal manufacturing, the ability to transform wide coils of steel into precisely slit strips is a critical capability. This intricate process is facilitated by the remarkable machinery known as a steel coil slitting line. These sophisticated systems play a pivotal role in ensuring the efficient and accurate conversion of raw materials into components ready for diverse industrial applications.
Understanding the Steel Coil Slitting Process
At the heart of the steel processing industry lies the slitting line, a complex assembly of interconnected components that work in harmony to transform wide metal coils into narrower, more manageable strips. This process begins with the careful loading and positioning of the coil, followed by a series of meticulously orchestrated steps that culminate in the production of precisely slit steel mults, or individual coils.
The Coil Car: Transporting the Raw Material
The first crucial component of a slitting line is the coil car, a specialized piece of equipment responsible for the safe and efficient transportation of heavy steel coils from the storage area to the uncoiler. This coil car ensures that the coils are positioned correctly and loaded smoothly onto the uncoiler, setting the stage for the subsequent steps in the slitting process.
The Uncoiler: Unwinding the Metal
Once the coil is securely in place, the uncoiler takes center stage. This component is tasked with gradually unwinding the coil, feeding the metal strip into the slitting line with a consistent and controlled motion. Equipped with features like snubber rolls, the uncoiler helps maintain the proper tension and alignment of the material, preparing it for the next phase of the process.
The Peeler Table: Initiating the Unwinding
Complementing the uncoiler’s role is the peeler table, a device that helps to initiate the unwinding of the coil. By lifting the edge of the coil and guiding it into the pinch rolls, the peeler table ensures a smooth and seamless transition from the coil to the slitting line.
Pinch Rolls and Straightener: Ensuring Alignment
As the metal strip enters the slitting line, it encounters the pinch rolls and straightener, two critical components that work in tandem to maintain the integrity of the material. The pinch rolls grip the strip and pull it through the line, while the straightener removes any bends or twists, ensuring the strip is flat and properly aligned for the slitting process.
The Loop Control System: Maintaining Tension
To prevent the material from snapping or stretching during the slitting process, the loop control system plays a vital role. This system creates a loop of metal between the uncoiler and the slitter head, absorbing any fluctuations in speed or tension and maintaining a consistent, stress-free flow of the material.
The Slitter Head: The Heart of the Operation
The slitter head is undoubtedly the most crucial component of the slitting line. This intricate assembly houses the rotary knives that precisely cut the metal strip into narrower mults or strips. The configuration and positioning of these knives can be adjusted to accommodate various width and thickness requirements, ensuring the production of slit coils that meet the specific needs of the end-user.
The Scrap Winder: Recycling the Waste
As the slitting process unfolds, the creation of edge trims or scrap is an inevitable byproduct. The scrap winder, a dedicated component of the slitting line, collects these trimmings and winds them into manageable coils, facilitating their efficient disposal or recycling, thereby minimizing waste and promoting sustainable practices.
The Tension Stand: Maintaining Alignment
After the metal has been slit into individual strips, the tension stand plays a critical role in ensuring their continued alignment and tension. This component keeps the slit strips taut and properly oriented as they are fed towards the recoiler, preparing them for the final stage of the process.
The Recoiler: Winding the Finished Coils
The recoiler is the final piece of the puzzle, responsible for rewinding the slit strips into individual coils. This component ensures that the finished mults are neatly and securely wound, ready for the next stage of production or distribution. The recoiler’s precise control over the winding process is essential for maintaining the integrity and quality of the slit steel coils.
The Exit Coil Car: Transporting the Finished Product
Much like the coil car that transported the raw material to the slitting line, the exit coil car plays a crucial role in the final stage of the process. This component is tasked with moving the finished coils from the recoiler to the storage area, ensuring the safe and efficient handling of the end product.
Technological Advancements in Slitting Line Design
In the ever-evolving world of metal processing, the design and engineering of slitting lines have undergone significant advancements. Leading steel processing companies like National Material Company (NMC) have invested heavily in developing robust, precision-engineered slitting machines equipped with cutting-edge software, tooling practices, and hardware. These technological innovations have enabled steel processors to streamline their production, reduce scrap, and deliver high-quality slit steel coils to their clients with unparalleled efficiency.
Conclusion
The steel coil slitting line is a marvel of engineering, a complex and interconnected system of components that work in harmony to transform wide metal coils into precisely slit strips. From the coil car to the recoiler, each component plays a vital role in ensuring the accuracy, efficiency, and sustainability of the steel processing industry. By understanding the intricacies of a slitting line and the technological advancements that drive its evolution, we can appreciate the crucial role these systems play in supporting the diverse manufacturing needs of modern industries.