How to Calculate Load-Bearing Capacity of Flat Bars
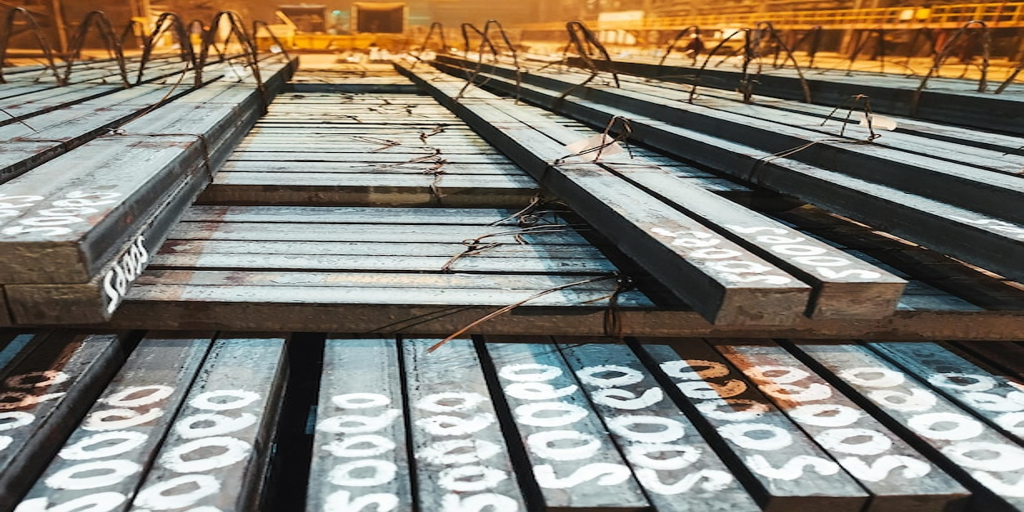
Calculating the load-bearing capacity of flat bars is a fundamental skill for engineers and designers involved in structural applications. A flat bar, typically made from materials such as steel or aluminum, is used in various construction and manufacturing settings due to its versatility and strength. Understanding how to accurately assess the load capacity of these bars is crucial for ensuring safety and performance in any project. This article will guide you through the essential concepts, calculations, and considerations involved in determining the load-bearing capacity of flat bars.
Understanding Flat Bars
What Are Flat Bars?
Flat bars are long, rectangular pieces of metal that have a uniform thickness. They are commonly used in construction, manufacturing, and various engineering applications. The dimensions of a flat bar are typically expressed in terms of width, thickness, and length, which play a significant role in determining their load-bearing capabilities.
Common Materials Used
Flat bars can be made from various materials, including:
- Steel: Known for its high tensile strength and durability, making it ideal for heavy-duty applications.
- Aluminum: Lightweight and resistant to corrosion, often used in applications where weight savings are critical.
- Stainless Steel: Offers excellent corrosion resistance and is commonly used in environments exposed to moisture or chemicals.
Applications of Flat Bars
Flat bars are utilized in a multitude of applications, such as:
- Structural Support: Used in beams, frames, and other load-bearing structures.
- Manufacturing: Employed in the production of machinery, tools, and equipment.
- Decorative Elements: Incorporated in architectural designs and furnishings.
Factors Affecting Load-Bearing Capacity
Material Properties
The load-bearing capacity of a flat bar is significantly influenced by the material it is made from. Key properties include:
- Yield Strength: The stress at which a material begins to deform plastically. It is crucial for determining the maximum load a bar can handle before permanent deformation occurs.
- Ultimate Tensile Strength: The maximum stress a material can withstand while being stretched or pulled before breaking.
Dimensions of the Flat Bar
The dimensions of a flat bar directly impact its load-bearing capacity. Key dimensions include:
- Width (b): The horizontal measurement of the bar.
- Thickness (t): The vertical measurement of the bar.
- Length (L): The distance between support points, which influences bending and deflection.
Support Conditions
The way a flat bar is supported plays a critical role in its load-bearing capacity. Common support conditions include:
- Simply Supported: The bar is supported at both ends, allowing for maximum deflection in the center.
- Cantilevered: One end of the bar is fixed while the other is free, resulting in different load distribution and deflection characteristics.
Calculating Load-Bearing Capacity
Basic Formula
To calculate the load-bearing capacity of a flat bar, a fundamental equation can be applied:
[ P = \frac{4 \cdot f \cdot S}{L} ]
Where:
- ( P ) = Concentrated load
- ( f ) = Strength of the material (yield or ultimate)
- ( S ) = Section modulus
- ( L ) = Distance between support points
Section Modulus Calculation
The section modulus (S) is a geometric property that reflects how a given cross-section resists bending. For a flat bar, it can be calculated as follows:
[ S = \frac{b \cdot t^2}{6} ]
Where:
- ( b ) = Width of the bar
- ( t ) = Thickness of the bar
Considerations for Deflection
Importance of Deflection
While calculating the load-bearing capacity is essential, it is equally important to consider deflection. Excessive deflection can lead to structural failure or compromise the integrity of the system.
Deflection Formula
The deflection (( \delta )) of a simply supported beam can be calculated using the following formula:
[ \delta = \frac{P \cdot L^3}{48 \cdot E \cdot I} ]
Where:
- ( E ) = Modulus of elasticity of the material
- ( I ) = Moment of inertia of the cross-section
Safety Factors
What Are Safety Factors?
A safety factor is a critical component in engineering design, providing a margin of safety against unforeseen loads, material defects, or miscalculations. It is expressed as a ratio of the maximum load a structure can support to the intended load.
Determining Safety Factors
Common safety factors for structural applications typically range from 1.5 to 3. The choice of safety factor depends on several factors, including:
- Material Properties: Higher safety factors may be necessary for materials with lower reliability.
- Load Variability: If loads are expected to fluctuate significantly, a higher safety factor is prudent.
- Consequences of Failure: In applications where failure could result in severe consequences, a higher safety factor is essential.
Incorporating Safety Factors into Calculations
To incorporate safety factors into load calculations, the design load (( P_d )) can be adjusted:
[ P_d = \frac{P_{max}}{SF} ]
Where:
- ( P_d ) = Design load
- ( P_{max} ) = Maximum load capacity
- ( SF ) = Safety factor
Real-World Applications
Construction Industry
In the construction sector, flat bars are frequently used in beams, frames, and structural supports. Understanding load-bearing capacity is vital for ensuring the safety and integrity of buildings and infrastructure.
Manufacturing Sector
Manufacturers utilize flat bars in machinery and equipment, where precise load calculations are necessary to avoid operational failures.
Automotive Industry
In automotive applications, flat bars are often used in chassis and frame designs, where weight reduction and strength are critical.
Conclusion
Calculating the load-bearing capacity of flat bars is an essential skill for engineers and designers. By understanding the factors that influence load capacity, utilizing the correct calculations, and considering safety factors, professionals can ensure the integrity and safety of their designs. Whether in construction, manufacturing, or automotive applications, mastering these concepts is crucial for successful engineering practices.