Steel Gauge Standards: Ensuring Quality and Consistency
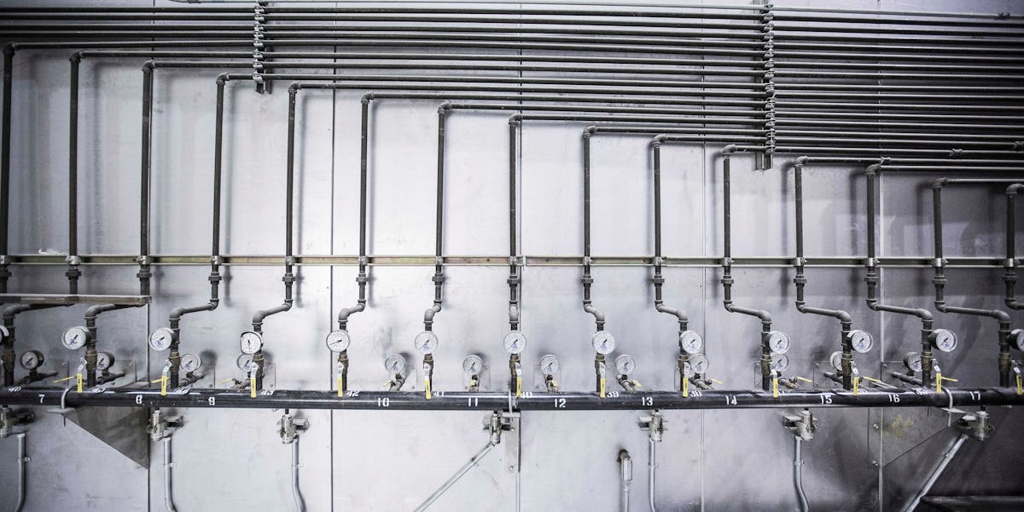
Understanding steel gauge standards is crucial for professionals in manufacturing, construction, and engineering. These standards provide essential information regarding the thickness of steel materials, which directly impacts the quality and integrity of the finished product. This article delves into the intricacies of steel gauge standards, exploring their importance, different types of gauge systems, and how to effectively utilize gauge charts for optimal results.
The Importance of Steel Gauge Standards
Steel gauge standards serve as a universal reference point for measuring the thickness of steel sheets, plates, and wires. These standards play a pivotal role in ensuring quality and consistency across various industries, including automotive, aerospace, and construction. By adhering to established gauge standards, manufacturers can achieve the following:
- Quality Assurance: Consistency in material thickness is vital for the performance and safety of products. Steel gauge standards help maintain uniformity, ensuring that components meet specified tolerances.
- Cost Efficiency: Understanding gauge standards can lead to more efficient material usage, reducing waste and optimizing production processes. This, in turn, can result in significant cost savings.
- Design Compatibility: Many engineering designs rely on precise material specifications. By adhering to gauge standards, manufacturers can ensure compatibility with existing designs and components.
- Regulatory Compliance: Many industries are subject to strict regulations regarding material specifications. Familiarity with gauge standards helps companies comply with these regulations, avoiding potential legal issues.
Overview of Gauge Systems
The gauge system is a method used to quantify the thickness of steel and other metals. It is essential to understand that the gauge number does not directly correlate with thickness; rather, it operates on a reverse scale. As the gauge number increases, the thickness of the material decreases. This counterintuitive relationship is critical for professionals working with metal materials.
Common Gauge Systems
- American Wire Gauge (AWG): Primarily used for electrical wiring, the AWG system measures wire thickness. It is essential for ensuring safe and efficient electrical installations.
- Birmingham Wire Gauge (BWG): This system is commonly used for measuring the thickness of metal sheets and wires, particularly in the UK. Like AWG, BWG operates on a reverse scale.
- Standard Steel Gauge: This system is widely used in the manufacturing and construction industries. It provides a standardized method for measuring the thickness of steel sheets and plates.
Understanding Gauge Numbers
Gauge numbers vary across different materials and systems. For instance, a 16-gauge steel sheet is thicker than a 20-gauge sheet, but the same gauge number may represent different thicknesses in other materials, such as aluminum or copper. Understanding these nuances is crucial for selecting the appropriate material for specific applications.
Reading Steel Gauge Charts
Steel gauge charts are invaluable tools that provide detailed information about the thickness of various steel materials. These charts typically include the gauge number, thickness in inches and millimeters, and weight per square foot. Familiarity with reading gauge charts is essential for ensuring accurate measurements and material selection.
Components of a Gauge Chart
- Gauge Number: The number assigned to the thickness of the material. Lower numbers indicate thicker materials.
- Thickness: The actual measurement of the material’s thickness, usually presented in both inches and millimeters.
- Weight per Square Foot: This figure represents the weight of one square foot of the material, providing insight into the material’s density and suitability for specific applications.
How to Use a Gauge Chart
To effectively use a gauge chart, follow these steps:
- Identify the Required Gauge: Determine the gauge number needed for your project based on design specifications and material requirements.
- Locate the Corresponding Thickness: Find the gauge number on the chart and note the associated thickness in both inches and millimeters.
- Check the Weight: Review the weight per square foot to ensure the material meets your project’s weight requirements.
- Select the Appropriate Material: Based on the gauge chart, choose the correct steel type (e.g., stainless steel, galvanized steel) that aligns with your project’s needs.
Types of Steel Gauge Charts
Different types of steel gauge charts exist, each tailored to specific materials and applications. Understanding these variations is essential for selecting the right chart for your project.
Stainless Steel Gauge Chart
Stainless steel gauge charts provide information specific to stainless steel materials, which are known for their corrosion resistance and durability. Below is a sample of a stainless steel gauge chart:
Gauge Number Thickness (inches) Thickness (mm) Weight per Square Foot (lbs) 0 0.3125 7.9375 12.5 1 0.28125 7.14375 11.25 2 0.265625 6.746875 10.625 3 0.25 6.35 10 4 0.234375 5.953125 9.375 Standard Steel Gauge Chart
Standard steel gauge charts are widely used in various industries. They provide a comprehensive overview of the thickness and weight of standard steel sheets. Here’s a sample chart:
Gauge Number Thickness (inches) Thickness (mm) Weight per Square Foot (lbs) 3 0.2391 6.073 9.754 4 0.2242 5.695 9.146 5 0.2092 5.314 8.534 6 0.1943 4.935 7.927 7 0.1793 4.554 7.315 Galvanized Steel Gauge Chart
Galvanized steel gauge charts are essential for projects involving galvanized materials, which are coated to prevent corrosion. Below is a sample galvanized steel gauge chart:
Gauge Number Thickness (inches) Thickness (mm) Weight per Square Foot (lbs) 8 0.168 4.270 9.754 9 0.153 3.891 6.406 10 0.138 3.510 5.781 11 0.132 3.353 5.156 12 0.108 2.753 4.531 Factors Affecting Gauge Selection
When selecting the appropriate gauge for a project, several factors must be considered to ensure optimal performance and safety.
Material Type
Different materials have unique properties that affect gauge selection. For instance, stainless steel is more durable than mild steel, allowing for thinner gauges without compromising strength. Understanding the material’s characteristics is crucial for making informed decisions.
Application Requirements
The intended application of the steel material significantly influences gauge selection. For structural applications, thicker gauges may be necessary to support heavier loads, while aesthetic applications may allow for thinner materials.
Environmental Conditions
Consider the environmental conditions the material will be exposed to. For example, materials used in corrosive environments may require thicker gauges or specialized coatings to ensure longevity.
Common Misconceptions About Gauge Standards
Several misconceptions surrounding steel gauge standards can lead to confusion and errors in material selection. Addressing these misunderstandings is essential for ensuring quality and consistency.
Higher Gauge Equals Thicker Material
One of the most common misconceptions is that a higher gauge number indicates a thicker material. In reality, as the gauge number increases, the thickness decreases. Professionals must be aware of this relationship to avoid selecting the wrong material.
Gauge Standards Are Universal
While many gauge systems exist, not all are interchangeable. For instance, the American Wire Gauge (AWG) system differs from the Birmingham Wire Gauge (BWG) system. Understanding the specific gauge system applicable to your project is crucial for accurate measurements.
All Materials Use the Same Gauge System
Different materials have unique gauge systems. For example, aluminum uses a different gauge standard than steel. It is essential to reference the appropriate gauge chart for the specific material being used.
Best Practices for Ensuring Gauge Accuracy
To maintain quality and consistency in steel gauge measurements, professionals should adopt best practices throughout the measurement and selection process.
Regular Calibration of Measurement Tools
Ensure that all measuring tools, such as calipers and micrometers, are regularly calibrated to maintain accuracy. This practice helps prevent errors in gauge selection and ensures compliance with industry standards.
Utilize Reliable Gauge Charts
Always reference reliable and up-to-date gauge charts specific to the material being used. These charts provide essential information regarding thickness and weight, aiding in accurate material selection.
Conduct Thorough Inspections
Before finalizing material selection, conduct thorough inspections of the steel sheets or plates to confirm that they meet the specified gauge requirements. This step helps identify any discrepancies that may affect the quality of the final product.
Conclusion
Steel gauge standards are fundamental to achieving quality and consistency in various industries. Understanding the intricacies of gauge systems, reading gauge charts accurately, and adhering to best practices can significantly enhance the manufacturing process. By focusing on these aspects, professionals can ensure optimal material selection, reduce waste, and maintain compliance with industry regulations.