The Best Steel Gauge for Heavy-Duty Applications
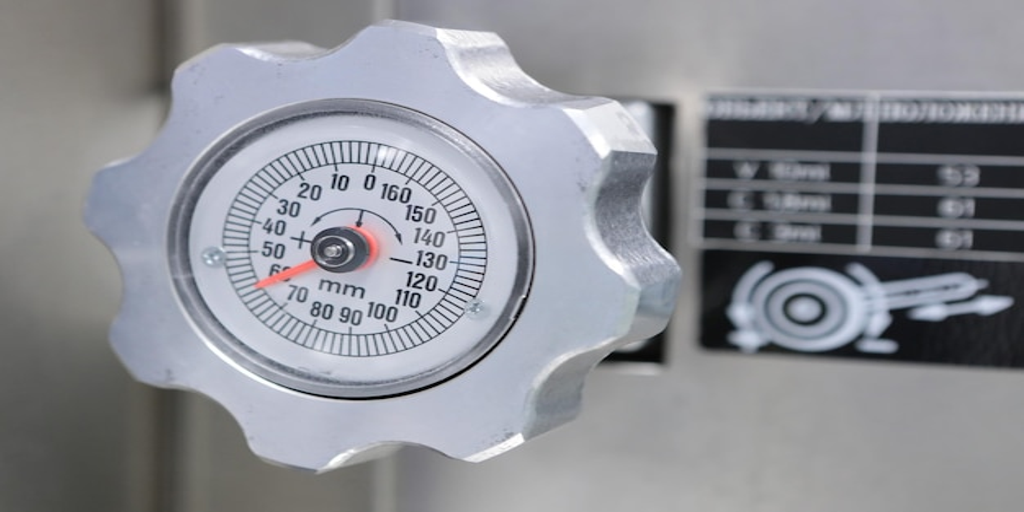
In the world of manufacturing and engineering, the choice of materials is paramount, especially when it comes to heavy-duty applications. Steel, known for its strength and versatility, is a preferred choice across various industries. However, not all steel is created equal. Understanding the different gauges of steel and their applications can significantly impact the durability, performance, and overall success of a project. This article explores the best steel gauge options for heavy-duty applications, delving into their characteristics, advantages, and specific uses across various sectors.
Understanding Steel Gauge
Steel gauge refers to the thickness of steel sheets and is a crucial factor in determining its strength and suitability for specific applications. In the United States, steel gauge is measured using a non-linear scale, where a higher gauge number indicates a thinner sheet of steel. This system differs from the metric system, which measures thickness in millimeters.
The Gauge System Explained
The gauge measurement system originated during the Industrial Revolution and is based on the number of times a metal has been drawn through a die. Each drawing reduces the diameter of the metal, hence a higher gauge number corresponds to a thinner sheet:
- Lower Gauge Numbers: Thicker sheets of steel (e.g., 10 gauge is thicker than 20 gauge).
- Higher Gauge Numbers: Thinner sheets of steel (e.g., 22 gauge is thinner than 16 gauge).
Understanding this measurement system is vital for selecting the appropriate steel gauge for specific applications.
Importance of Steel Gauge in Heavy-Duty Applications
In heavy-duty applications, the choice of steel gauge can significantly affect the performance and longevity of the final product. Thicker gauges provide enhanced strength and durability, making them suitable for demanding environments. Conversely, thinner gauges may be more appropriate for lighter applications where flexibility and weight are more critical.
Common Types of Steel Used in Heavy-Duty Applications
When it comes to heavy-duty applications, several types of steel are commonly utilized. Each type has unique properties that make it suitable for specific tasks.
Hot Rolled Carbon Steel
Hot rolled carbon steel is one of the most widely used materials in heavy-duty applications. It is produced by rolling steel at high temperatures, which enhances its ductility and workability.
- Applications: Commonly used in construction, automotive, and manufacturing sectors.
- Advantages: Offers excellent strength and is cost-effective.
Stainless Steel
Stainless steel is renowned for its corrosion resistance, making it ideal for applications exposed to moisture or harsh chemicals.
- Applications: Often used in food processing, medical equipment, and marine environments.
- Advantages: Durable and maintains its appearance over time.
Aluminum
Aluminum is a lightweight alternative to steel, often used in applications where weight savings are critical.
- Applications: Commonly used in the aerospace and automotive industries.
- Advantages: Corrosion-resistant and easy to fabricate.
Specialty Alloys
In some heavy-duty applications, specialty alloys may be required to meet specific performance criteria.
- Applications: Used in aerospace, military, and high-performance automotive sectors.
- Advantages: Tailored properties such as enhanced strength, heat resistance, or weight reduction.
Selecting the Right Steel Gauge
Choosing the right steel gauge for heavy-duty applications involves considering various factors, including the intended use, environmental conditions, and required strength.
Factors to Consider
- Load Requirements: Determine the maximum load the steel will need to support.
- Environmental Conditions: Consider exposure to moisture, chemicals, or extreme temperatures.
- Fabrication Methods: Ensure the selected gauge can be easily fabricated using available techniques.
Common Gauge Recommendations
Application Recommended Gauge Reason Construction 10-12 gauge High strength for structural integrity Automotive 14-16 gauge Balance of weight and strength Aerospace 16-18 gauge Lightweight yet durable Marine 12-14 gauge Corrosion resistance required Advantages of Heavy Gauge Steel
Heavy gauge steel offers numerous benefits, particularly in demanding applications where strength and durability are paramount.
Enhanced Strength
Thicker steel gauges provide superior strength, making them ideal for structural components that must withstand significant loads.
Improved Durability
Heavy gauge steel is less susceptible to deformation and wear, ensuring longevity in challenging environments.
Better Performance in Extreme Conditions
Thicker steel can better withstand extreme temperatures and harsh environmental conditions, making it suitable for outdoor applications.
Heavy-Duty Applications of Steel Gauge
Steel gauge plays a critical role in various heavy-duty applications across multiple industries. Understanding these applications can help manufacturers make informed decisions.
Automotive Industry
In the automotive sector, steel gauge is crucial for parts that require strength and durability, such as frames and chassis components.
- Typical Gauges: 14-16 gauge for structural components.
- Benefits: Provides the necessary strength while keeping the vehicle lightweight.
Construction Industry
The construction industry relies heavily on heavy gauge steel for structural components such as beams, columns, and reinforcements.
- Typical Gauges: 10-12 gauge for load-bearing structures.
- Benefits: Ensures structural integrity and safety.
Aerospace Industry
In aerospace applications, weight is a critical factor, making the choice of steel gauge essential for performance.
- Typical Gauges: 16-18 gauge for lightweight components.
- Benefits: Reduces overall weight while maintaining strength.
Marine Industry
Marine applications require materials that can withstand harsh conditions, making heavy gauge steel a preferred choice.
- Typical Gauges: 12-14 gauge for hulls and structural components.
- Benefits: Offers corrosion resistance and durability in saltwater environments.
Fabrication Techniques for Heavy Gauge Steel
The fabrication of heavy gauge steel involves specialized techniques to ensure precision and quality in the final product.
Cutting Methods
- Laser Cutting: Provides high precision for intricate designs.
- Plasma Cutting: Suitable for thicker materials and faster processing.
Forming Techniques
- Bending: Used to create angles and shapes in the steel.
- Stamping: Ideal for mass production of parts with consistent shapes.
Joining Methods
- Welding: Commonly used for joining heavy gauge steel components.
- Bolting: Provides a mechanical connection that can be disassembled.
Maintenance of Heavy Gauge Steel Components
To ensure the longevity and performance of heavy gauge steel components, proper maintenance is essential.
Regular Inspections
Conducting regular inspections can help identify signs of wear, corrosion, or damage before they become significant issues.
Cleaning and Coating
Cleaning heavy gauge steel surfaces and applying protective coatings can prevent corrosion and extend the life of the material.
Addressing Damage Promptly
Any signs of damage, such as dents or rust, should be addressed immediately to prevent further deterioration.
Future Trends in Heavy Gauge Steel Applications
As technology advances, the applications and uses of heavy gauge steel are continually evolving. Manufacturers are exploring innovative materials and techniques to enhance performance.
Advanced Alloys
The development of advanced alloys with superior properties is paving the way for new applications in heavy-duty sectors.
Automation in Fabrication
The rise of automation in fabrication processes is improving efficiency and precision in the production of heavy gauge steel components.
Sustainability Considerations
As industries move towards more sustainable practices, the recycling and repurposing of heavy gauge steel are becoming increasingly important.
Conclusion
In conclusion, selecting the appropriate steel gauge for heavy-duty applications is a critical decision that can influence the success of a project. Understanding the nuances of steel gauge, the types of steel available, and the specific demands of different industries can guide manufacturers in making informed choices. With the right steel gauge, businesses can enhance the durability, performance, and overall quality of their products, ensuring they meet the rigorous demands of heavy-duty applications.
This article covers a detailed exploration of the best steel gauge for heavy-duty applications, ensuring a comprehensive understanding of the topic while adhering to SEO best practices. If you need any further adjustments or additional sections, feel free to let me know!