Why Steel Gauge Matters in Automotive Manufacturing
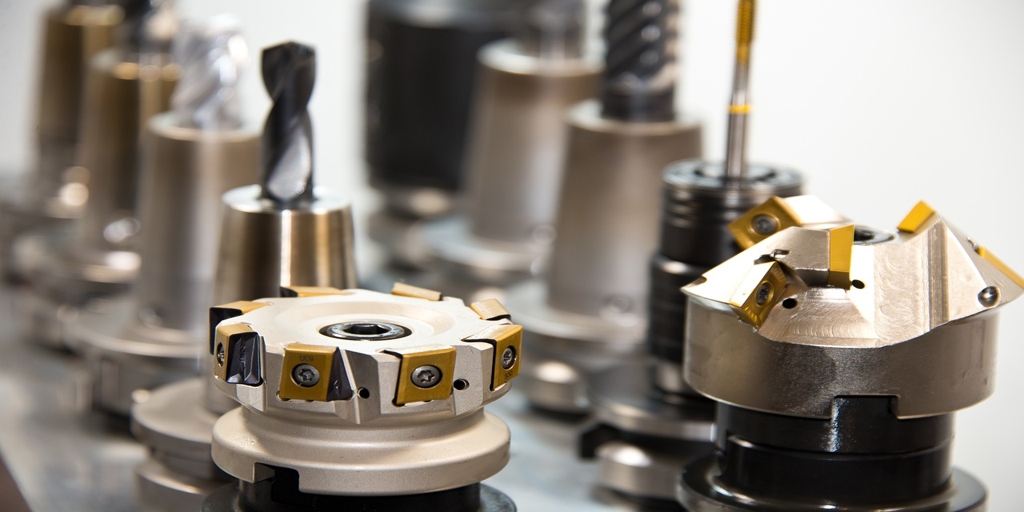
In the automotive industry, the choice of materials plays a pivotal role in ensuring safety, performance, and efficiency. Among these materials, steel remains a cornerstone due to its strength, durability, and versatility. However, not all steel is created equal, and the gauge of steel is a crucial factor that significantly impacts automotive manufacturing. Understanding why steel gauge matters is essential for engineers, manufacturers, and automotive designers alike.
Understanding Steel Gauge
What is Steel Gauge?
Steel gauge refers to the thickness of the steel sheet, with lower gauge numbers indicating thicker sheets. This measurement is critical in determining the strength and weight of the steel used in automotive applications. The gauge system can vary between different types of steel, but it typically follows a standard where:
- 18-gauge steel measures approximately 1.2 mm thick.
- 20-gauge steel is about 0.9 mm thick.
- 22-gauge steel is around 0.7 mm thick.
The choice of gauge affects various properties of the steel, including its weight, flexibility, and resistance to deformation.
Why is Gauge Important?
The gauge of steel directly influences several key aspects of automotive manufacturing:
- Weight Reduction: Lighter vehicles enhance fuel efficiency. Using thinner gauges can significantly reduce the overall weight of a vehicle without sacrificing structural integrity.
- Strength and Durability: Thicker gauges provide more strength, making them ideal for components that must withstand high stress, such as frames and structural reinforcements.
- Formability: Thinner gauges are easier to form into complex shapes, allowing for more intricate designs and better aerodynamics.
- Cost Efficiency: Selecting the appropriate gauge can lead to cost savings in material usage and manufacturing processes.
The Role of Steel in Automotive Manufacturing
Importance of Steel in Vehicles
Steel is an integral part of automotive manufacturing, providing the structural framework for vehicles. Its properties make it suitable for various applications, including:
- Body-in-White (BIW): The unpainted body of a vehicle, which requires high strength and rigidity.
- Structural Components: Parts like pillars, roof rails, and reinforcements that enhance safety and stability.
- Closure Panels: Components such as doors, hoods, and fenders that require a balance of aesthetics and functionality.
Types of Steel Used in Automotive Applications
The automotive industry utilizes several types of steel, each with specific properties suited for different applications:
- Mild Steel: Known for its ductility and weldability, mild steel is commonly used in non-structural components.
- High-Strength Steel (HSS): Offers enhanced strength-to-weight ratios, making it ideal for structural applications.
- Ultra High-Strength Steel (UHSS): Used in critical areas where maximum strength is required, such as crash zones.
Evaluating Steel Gauge in Automotive Design
Selecting the Right Gauge
Choosing the appropriate steel gauge is a balancing act. Engineers must consider factors such as:
- Safety Standards: Compliance with safety regulations is paramount, particularly in areas that protect passengers during collisions.
- Design Specifications: The required aesthetics and functionality of components dictate the choice of gauge.
- Manufacturing Processes: Some processes, such as stamping and welding, may have limitations on the thickness of the material used.
Impact on Performance
The gauge of steel can significantly affect vehicle performance. Thicker steel may enhance crashworthiness but can add weight, which negatively impacts fuel efficiency. Conversely, thinner steel can reduce weight but may compromise safety if not properly designed.
Testing and Compliance
Automakers must conduct rigorous testing to ensure that the selected steel gauge meets performance and safety standards. This includes:
- Crash Tests: Evaluating how different gauges perform during collisions.
- Fatigue Testing: Assessing the durability of components over time and under stress.
Innovations in Steel Manufacturing
Advanced Steel Technologies
The automotive industry is continuously evolving, and so is the technology behind steel manufacturing. Innovations include:
- Dual-Phase Steel: This material combines high strength with excellent formability, making it ideal for safety-critical components.
- Martensitic Steel: Known for its superior strength, martensitic steel is often used in areas that require maximum impact resistance.
Lightweighting Initiatives
As the demand for fuel-efficient vehicles grows, manufacturers are increasingly focused on lightweighting. This involves using advanced materials and techniques to reduce vehicle weight, such as:
- High-Strength Lightweight Materials: Incorporating advanced steel grades that offer strength without added weight.
- Hybrid Materials: Combining steel with other materials, such as aluminum, to achieve optimal performance.
The Manufacturing Process and Steel Gauge
Fabrication Techniques
The fabrication process plays a crucial role in determining how steel gauge impacts the final product. Common techniques include:
- Stamping: A process that shapes steel sheets into complex forms. The gauge must be carefully selected to ensure successful stamping without cracking.
- Welding: Different welding techniques may be required based on the gauge of steel. For instance, thicker gauges may require different settings compared to thinner ones.
Quality Control Measures
To ensure that the selected steel gauge meets specifications, manufacturers implement stringent quality control measures, including:
- Visual Inspections: Checking for defects in the steel sheets before fabrication.
- Dimensional Checks: Ensuring that the gauge and dimensions meet design requirements.
Challenges in Steel Gauge Selection
Balancing Strength and Weight
One of the primary challenges in selecting steel gauge is achieving the right balance between strength and weight. Engineers must consider:
- Crash Safety: Ensuring that components can withstand impacts while minimizing weight for fuel efficiency.
- Cost Constraints: Thicker gauges may increase material costs, impacting overall project budgets.
Variability in Steel Properties
Different batches of steel can exhibit variability in properties, even if they are of the same gauge. Manufacturers must account for this by conducting:
- Material Testing: Regularly testing steel samples to ensure consistency in performance.
- Supplier Quality Assurance: Working closely with suppliers to ensure that the materials meet the required specifications.
Case Studies: Real-World Applications
Success Stories
Several automotive manufacturers have successfully navigated the challenges of steel gauge selection. Notable examples include:
- Ford’s Use of Advanced High-Strength Steel: Ford has implemented advanced high-strength steel in its vehicles to enhance safety while reducing weight.
- Tesla’s Innovative Approach: Tesla incorporates lightweight materials, including high-strength steel, to improve performance and efficiency in its electric vehicles.
Lessons Learned
From these case studies, key lessons emerge regarding the importance of steel gauge in automotive manufacturing:
- Collaboration is Key: Close collaboration between design, engineering, and manufacturing teams is essential to optimize material selection.
- Continuous Improvement: Ongoing research and development in material science can lead to better performance and safety outcomes.
Future Trends in Steel Gauge Usage
Evolving Industry Standards
As the automotive industry evolves, so too do the standards governing steel gauge usage. Future trends may include:
- Stricter Safety Regulations: Increasingly stringent safety standards will drive the need for higher quality materials and innovative designs.
- Sustainability Initiatives: The push for environmentally friendly manufacturing practices will influence material selection and gauge choices.
Advancements in Material Science
Ongoing advancements in material science will likely lead to new steel formulations and gauges that offer improved performance. Potential developments include:
- Smart Materials: The integration of technology into materials to enhance performance and safety.
- Recyclable Steel Options: Increasing focus on sustainability may lead to the development of more recyclable steel options.
Conclusion
In summary, the gauge of steel is a critical factor in automotive manufacturing that influences safety, performance, and cost. Understanding the intricacies of steel gauge selection is essential for automotive engineers and manufacturers striving to create vehicles that meet modern demands for efficiency and safety. As the industry continues to evolve, staying informed about advancements in steel technology and fabrication techniques will be vital for success in this competitive landscape.