Heavy Gauge Steel Slitting Techniques for Enhanced Precision
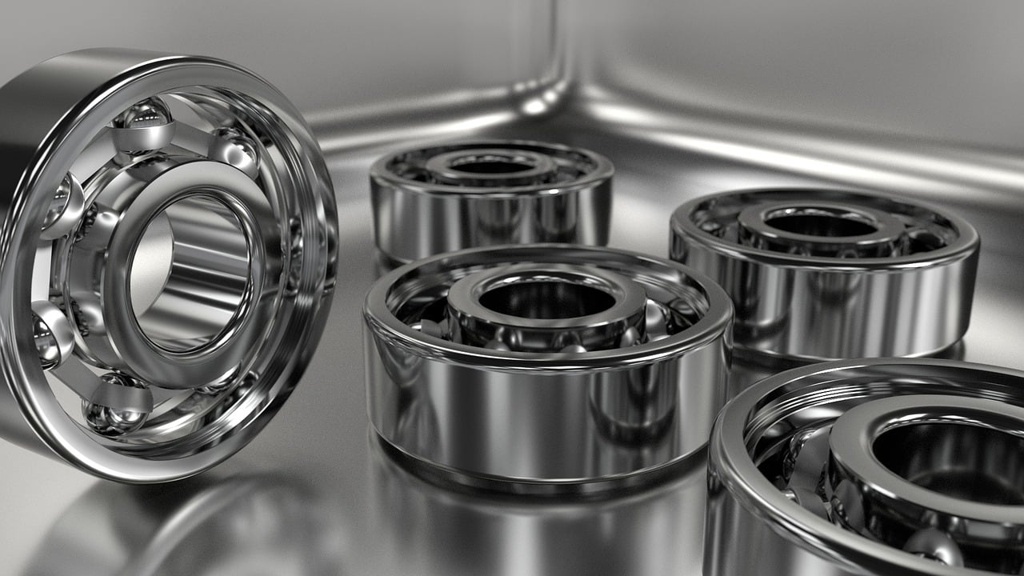
Understanding Heavy Gauge Steel Slitting
Heavy gauge steel slitting is a vital process in the manufacturing and metalworking industries, particularly for producing high-strength components. The method involves cutting large coils of steel into narrower strips, which can be used in various applications, including automotive, construction, and appliance manufacturing. The precision of this process is crucial, as it directly affects the quality of the final product.
Importance of Precision in Slitting
Precision in slitting ensures that the resulting strips meet specific tolerances for thickness and width. This is essential for maintaining the integrity of the material and ensuring that it can be effectively processed in subsequent manufacturing stages. Inaccuracies during slitting can lead to increased scrap rates, production delays, and ultimately, higher costs.
Key Factors Influencing Slitting Precision
Several factors contribute to the precision of heavy gauge steel slitting:
- Material Quality: The properties of the steel, including its thickness and alloy composition, significantly influence how it behaves during slitting. High-strength low-alloy (HSLA) steels are often preferred for their balance of strength and ductility.
- Slitting Equipment: The type and condition of the slitting machinery play a critical role. Advanced slitting lines equipped with sharp blades and proper setup can achieve tighter tolerances.
- Operator Skill: Experienced operators are crucial for achieving high precision. Their understanding of the machinery and material behavior can help mitigate issues like camber and burr formation.
Slitting Techniques Overview
When it comes to slitting heavy gauge steel, various techniques can be employed, each with its advantages and disadvantages. Understanding these methods is essential for selecting the right approach for specific applications.
Razor Blade Slitting
Razor blade slitting involves using a simple blade to cut through the material. This method is typically used for lighter and non-abrasive materials.
- Advantages:
- Economical and quick setup.
- Suitable for thin gauge materials.
- Disadvantages:
- Limited effectiveness on thicker, rigid, or abrasive materials.
- High speeds can lead to film burnishing, causing defects.
Shear Cutting
Shear cutting employs two rotary knives that create a cutting action similar to scissors. This method is ideal for heavier gauge materials, including thicker films, sheets, and laminates.
- Advantages:
- High accuracy in slit widths.
- Capable of achieving close tolerances.
- Disadvantages:
- Requires precise setup to ensure the correct blade angle.
- More complex machinery can lead to higher operational costs.
Score Cutting
Also known as crush cutting, score cutting is one of the oldest methods used in slitting. It involves pressing a dull blade against a hard surface to sever the material.
- Advantages:
- Quick setup and simple machinery.
- Effective for slitting pressure-sensitive adhesives without creating sticky edges.
- Disadvantages:
- Can generate dust, leading to equipment malfunctions.
- May cause defects in plastic films, such as stretching or cracking.
Material Specifications for Optimal Slitting
Selecting the right starting coil for slitting is crucial for ensuring quality outcomes. Various specifications should be considered when ordering steel coils.
Thickness Tolerance
Thickness consistency is vital for maintaining product quality. Variations in thickness can lead to difficulties in machining and stamping processes.
- Recommendation: Consider purchasing coils with half-standard thickness tolerance to enhance yield and minimize waste.
Width Tolerance
Width tolerance is another critical factor that should be discussed with suppliers during the engineering phase of the part.
- Importance: Proper width specifications help avoid tooling issues and reduce scrap.
Edge Condition
The condition of the coil edges influences the overall quality of the slitting process. Excessive burrs can lead to shape distortions in the final product.
- Tip: Specify edge conditions when placing orders to ensure optimal processing.
Managing Camber in Slitting
Camber refers to the deviation of the strip edges from a straight line, which can complicate feeding into dies and affect the final product’s quality.
Causes of Camber
- Unequal Clearance: If the slitting equipment has unbalanced clearance on either side of the strip, it can induce stress and curvature.
- Knife Condition: Using a combination of dull and sharp knives can lead to uneven shear/fracture ratios, exacerbating camber issues.
Preventing Camber
- Sharp Knives: Regular maintenance and replacement of dull blades can minimize camber.
- Balanced Setup: Ensure that slitting lines are correctly calibrated to prevent uneven pulling of the material.
Addressing Burr Formation
Burrs are unwanted projections that form on the edges of cut materials, often resulting from the slitting process. These can lead to defects in the final product.
Impact of Burrs
- Shape Distortion: Burrs can cause the strip to take on a convex or concave shape, affecting stamping accuracy.
- Edge Cracking: Heavy burrs can lead to cracking during tension leveling, increasing scrap rates.
Solutions for Burr Management
- Specify Edge Conditions: Clearly outline the required edge conditions when ordering materials.
- Regular Equipment Maintenance: Keeping slitting equipment in good condition can help reduce burr formation.
The Role of Tension Leveling
Tension leveling is a process applied after slitting to correct any shape distortions. However, if not performed correctly, it can lead to work hardening of the steel.
Benefits of Tension Leveling
- Shape Correction: Helps to achieve a flat strip that meets specifications.
- Material Consistency: Reduces variations in properties across the coil.
Risks of Improper Leveling
- Work Hardening: Inconsistent application of tension can lead to varying degrees of hardening, affecting the material’s performance in subsequent processes.
Quality Control in Slitting Operations
Implementing robust quality control measures is essential for ensuring that slitting operations meet industry standards.
Key Quality Control Measures
- Regular Inspections: Frequent checks of slitting equipment can help identify issues before they affect production.
- Material Testing: Conducting tests on incoming materials ensures they meet specified tolerances.
Importance of Documentation
Maintaining accurate records of slitting processes, including material specifications and equipment settings, can facilitate continuous improvement and troubleshooting.
Advanced Slitting Technologies
The evolution of slitting technologies continues to enhance precision and efficiency in heavy gauge steel processing.
Innovations in Machinery
- Automated Systems: Modern slitting lines often incorporate automation to improve accuracy and reduce labor costs.
- Smart Sensors: Integration of sensors can provide real-time feedback on material conditions, allowing for immediate adjustments.
Future Trends
- Sustainability: As industries move towards greener practices, slitting operations are also focusing on reducing waste and energy consumption.
- Digitalization: The adoption of digital technologies for monitoring and controlling slitting processes is on the rise.
Conclusion
Heavy gauge steel slitting is a complex process that requires careful attention to detail and a thorough understanding of the materials and techniques involved. By selecting the appropriate slitting method, managing material specifications, and implementing effective quality control measures, manufacturers can enhance precision and efficiency in their operations.
As technology continues to evolve, staying informed about advancements in slitting techniques will be essential for maintaining a competitive edge in the industry.