How Steel Slitting Lines Drive Efficiency in Metal Fabrication
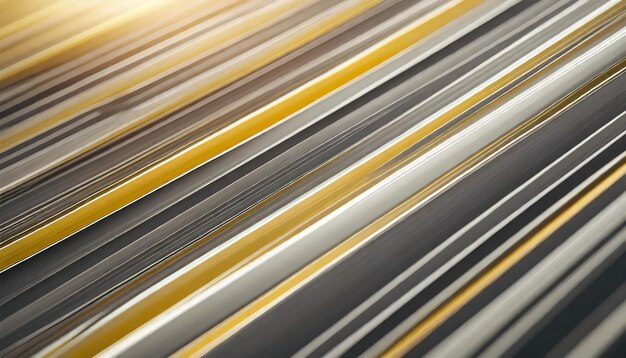
In the ever-evolving landscape of metal fabrication, the efficiency of production processes is paramount. Steel slitting lines have emerged as pivotal tools that not only enhance productivity but also ensure precision in processing steel coils. These machines are designed to transform wide steel coils into narrower strips, catering to various industrial needs. Understanding how steel slitting lines operate and their impact on production efficiency is crucial for manufacturers aiming to stay competitive in a demanding market
Understanding Steel Slitting Lines
Steel slitting lines consist of a series of machines that work in tandem to cut, process, and manage steel coils. At their core, these lines are engineered to deliver high-quality output with minimal waste. The process begins with loading the steel coil onto the line, where it is unwound and fed into the slitting machine.
Components of Steel Slitting Lines
- Uncoiler: This device unwinds the steel coil, preparing it for processing. It is crucial for maintaining tension and ensuring a smooth feed into subsequent machines.
- Slitting Machine: The heart of the operation, this machine cuts the coil into narrower strips. Advanced technology allows for precise cuts, ensuring uniformity in width and thickness.
- Re-coiler: After slitting, the strips are rewound into smaller coils. This component is essential for organizing the output for further processing or shipping.
- Shear and Edge Trim: These units remove any imperfections or excess material from the edges of the strips, enhancing the quality of the final product.
The Process Flow
The flow of the steel slitting line can be broken down into several stages:
- Loading: The steel coil is placed onto the uncoiler.
- Unwinding: The coil is unwound and fed into the slitting machine.
- Slitting: The slitting machine cuts the coil into specified widths.
- Trimming: Edge trimmers remove any excess material.
- Re-coiling: The finished strips are wound into smaller coils.
This streamlined process maximizes efficiency and minimizes downtime, allowing manufacturers to meet high production demands.
Enhancing Precision and Accuracy
One of the standout features of steel slitting lines is their ability to deliver exceptional precision. The integration of advanced technology and sensors ensures that each cut is executed with remarkable accuracy.
Advanced Cutting Technology
Modern slitting lines utilize cutting-edge technology, including laser-guided systems and high-speed blades, to achieve precise cuts. This technology minimizes deviations, producing strips that adhere to tight tolerances. The result is a reduction in the need for additional finishing operations, which can be time-consuming and costly.
Quality Control Mechanisms
To maintain high standards, steel slitting lines are equipped with quality control mechanisms. These systems monitor the cutting process in real-time, identifying any discrepancies and making necessary adjustments. This proactive approach not only enhances product quality but also reduces scrap rates.
Boosting Productivity
Steel slitting lines are designed for high-speed operations, which significantly boosts productivity in metal fabrication. The ability to process multiple coils simultaneously allows manufacturers to increase their output capacity.
Multi-Head Slitting Options
Many modern slitting lines feature multiple cutting heads that can operate concurrently. This capability enables the processing of several coils at once, effectively doubling or tripling production rates. As a result, manufacturers can fulfill larger orders without compromising quality.
Automation and Efficiency
Automation is a key factor in enhancing productivity. Steel slitting lines are increasingly equipped with automated loading, unloading, and scrap handling systems. This automation reduces the need for manual intervention, minimizing downtime and allowing operators to focus on other critical tasks.
Reducing Labor Costs
The integration of automation in steel slitting lines not only improves productivity but also contributes to significant cost savings. By minimizing the reliance on manual labor, manufacturers can reduce their operational expenses.
Ergonomic Designs
Modern slitting machines are designed with ergonomics in mind, reducing operator fatigue and enhancing safety. This focus on operator comfort leads to higher productivity levels and a decrease in workplace accidents.
Streamlined Operations
With automated systems in place, the need for extensive labor is diminished. Operators can oversee multiple processes simultaneously, allowing for a more streamlined operation. This efficiency translates into lower labor costs and improved profit margins.
Optimizing Material Utilization
Effective material utilization is crucial in metal fabrication, and steel slitting lines excel in this area. Advanced algorithms and nesting techniques ensure that raw materials are used efficiently, minimizing waste.
Nesting Algorithms
Steel slitting lines employ sophisticated nesting algorithms that calculate optimal cutting patterns. By determining the best way to cut the steel coils, these algorithms reduce scrap and maximize the yield of usable strips. This efficient use of materials not only lowers costs but also has positive environmental implications.
Waste Management
In addition to optimizing cuts, modern slitting lines incorporate waste management systems that efficiently handle scrap material. This approach not only reduces environmental impact but also allows for the recycling of materials, contributing to a more sustainable manufacturing process.
Flexibility and Versatility
One of the most significant advantages of steel slitting lines is their versatility. These machines can accommodate a wide range of steel thicknesses, widths, and grades, making them suitable for various applications.
Customization Options
Manufacturers can easily adjust machine settings and change cutting tools to meet specific product requirements. This flexibility allows companies to respond quickly to changing market demands, ensuring they can produce a diverse range of products without extensive downtime.
Multi-Product Capability
Steel slitting lines are designed to handle multiple products efficiently. Whether it’s different steel grades or varying widths, these machines can switch between tasks seamlessly, maximizing their utilization and reducing idle time.
Integration with Downstream Processes
Modern steel slitting lines are not standalone machines; they can be integrated into broader production systems. This integration enhances overall efficiency by streamlining workflows and reducing handling times.
Inline Processing
By integrating slitting lines with other processes such as leveling, edge trimming, and packaging, manufacturers can create a continuous flow of operations. This inline processing eliminates the need for multiple handling steps, saving time and increasing overall production efficiency.
Data Exchange and Communication
Advanced steel slitting lines are equipped with automated data exchange capabilities. This feature ensures seamless communication between machines, allowing for better process control and real-time monitoring. As a result, manufacturers can quickly identify and address any issues, further enhancing efficiency.
Quality Assurance and Consistency
Quality assurance is a critical aspect of metal fabrication, and steel slitting lines play a vital role in maintaining consistent product quality. The integration of quality control measures ensures that each strip produced meets stringent standards.
Continuous Monitoring
Steel slitting lines are equipped with sensors that continuously monitor the cutting process. This real-time monitoring allows for immediate adjustments, ensuring that any deviations are corrected promptly. The result is a consistent output that meets customer specifications.
Rigorous Testing Protocols
Before being deployed, slitting machines undergo rigorous testing to ensure their reliability and performance. Quality controllers assess each machine against a series of parameters, guaranteeing that they can deliver consistent results in production environments.
Environmental Considerations
As industries strive for sustainability, steel slitting lines contribute to eco-friendly practices in metal fabrication. By optimizing material utilization and reducing waste, these machines play a key role in minimizing environmental impact.
Waste Reduction Strategies
The advanced algorithms used in steel slitting lines not only optimize cuts but also contribute to waste reduction strategies. By producing less scrap, manufacturers can decrease their environmental footprint while also saving on material costs.
Recycling Initiatives
Many manufacturers have implemented recycling initiatives for scrap material generated during the slitting process. This approach not only supports sustainability efforts but also turns waste into a valuable resource, further enhancing the efficiency of operations.
Future Trends in Steel Slitting Technology
The landscape of steel slitting technology is continually evolving, with innovations that promise to further enhance efficiency and productivity. As manufacturers seek to remain competitive, staying abreast of these trends is essential.
Automation Advancements
The future of steel slitting lines will likely see increased automation, with advancements in robotics and artificial intelligence. These technologies will enable even greater efficiency, reducing human intervention and enhancing precision.
Smart Manufacturing
The integration of smart manufacturing concepts into steel slitting lines will revolutionize the industry. By leveraging data analytics and IoT technologies, manufacturers can optimize operations, improve decision-making, and enhance overall productivity.
Conclusion
Steel slitting lines are indispensable tools in the metal fabrication industry, driving efficiency and precision in production processes. Their ability to enhance productivity, reduce labor costs, and optimize material utilization makes them essential for manufacturers looking to thrive in a competitive market. As technology continues to advance, the capabilities of steel slitting lines will only improve, ensuring they remain at the forefront of metal processing innovation. By embracing these advancements, manufacturers can position themselves for success in an ever-changing landscape.