Key Components of Precision Steel Processing: An In-Depth Look at Slitting Lines
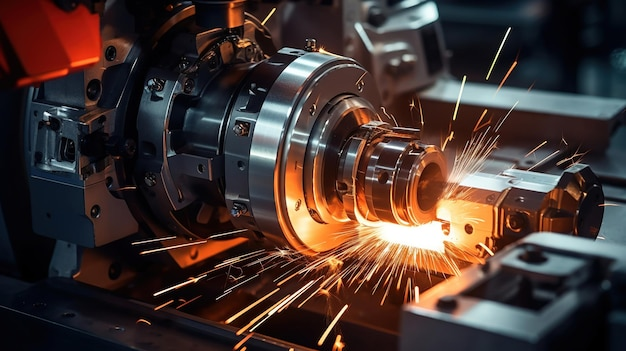
In the world of metal fabrication, precision is paramount, especially when it comes to processing steel. Steel slitting lines are essential machinery designed to cut steel coils into narrower strips, allowing for a variety of applications across numerous industries. This article delves into the intricate components and operations of slitting lines, elucidating their significance in modern manufacturing
Understanding Steel Slitting Lines
Steel slitting lines are sophisticated systems that transform large coils of steel into precise strips. These machines employ a series of components working together to ensure accuracy and efficiency throughout the cutting process.
Definition and Purpose
At its core, a steel slitting line serves the purpose of slicing wide coils of steel into narrower strips. This process is crucial for industries that require specific dimensions for their products, such as automotive, construction, and HVAC sectors.
Importance in Manufacturing
The significance of slitting lines extends beyond mere cutting. They enhance productivity, reduce waste, and improve the quality of the final product. By utilizing advanced technology, manufacturers can achieve high levels of precision, meeting stringent industry standards.
Key Components of Steel Slitting Lines
Understanding the key components of a slitting line is essential for grasping how these machines operate. Each element plays a vital role in ensuring smooth and accurate processing.
Uncoiler
The uncoiler is the first component in the slitting line process. It is responsible for unwinding the steel coil from its reel.
- Functionality: The uncoiler uses hydraulic systems to grip the coil and allow it to rotate freely. This ensures a steady feed into the slitting line.
- Types: There are various types of uncoilers, including single and double mandrel systems, designed to accommodate different coil sizes and weights.
Slitter
The slitter is the heart of the slitting line, where the actual cutting takes place.
- Design: Comprising multiple rotating circular blades, the slitter can cut the steel into varying widths based on predetermined specifications.
- Adjustability: Modern slitters often feature adjustable blade positions, allowing for quick changes in strip width without extensive downtime.
Tension Leveler
Maintaining consistent tension during the slitting process is crucial for achieving high-quality cuts.
- Role: The tension leveler ensures that the steel strip is held under uniform tension, preventing deformation and ensuring precision.
- Mechanism: It employs a series of rollers and sensors to monitor and adjust the tension as needed throughout the cutting process.
Rewinder
After slitting, the processed strips need to be collected and coiled for storage or further processing.
- Functionality: The rewinder collects the slit strips and coils them onto reels, ready for transportation or additional handling.
- Tension Control: Similar to the uncoiler, the rewinder also incorporates tension control mechanisms to ensure the quality of the coiled strips.
Types of Steel Slitting Lines
Different applications require different types of slitting lines. Understanding these variations can help manufacturers choose the right equipment for their needs.
Cut-to-Length Lines
These lines are designed to cut steel strips to precise lengths after the slitting process.
- Applications: Commonly used in industries where specific lengths are required, such as automotive manufacturing.
High-Speed Lines
High-speed slitting lines are engineered for rapid processing, allowing manufacturers to handle large volumes of steel efficiently.
- Benefits: Increased throughput and reduced operational costs make these lines ideal for high-demand environments.
Tension Leveling Lines
Primarily used for leveling and improving the flatness of processed steel, these lines incorporate advanced leveling technology.
- Importance: Ensuring the flatness of steel strips is crucial for applications where dimensional accuracy is critical.
Operation of Steel Slitting Lines
The operation of steel slitting lines follows a sequential process, ensuring that each step is executed with precision.
Uncoiling
The process begins with the uncoiling of the steel coil, where the uncoiler unwinds the material and feeds it into the slitting line.
Slitting
As the steel strip moves through the slitter, the rotating knives cut it into narrower strips based on predetermined dimensions.
Tension Leveling
During this phase, the tension leveler maintains consistent tension to prevent any deformation of the material.
Rewinding
Finally, the rewinder collects the processed strips and coils them for easy handling and storage.
Applications of Steel Slitting Lines
Steel slitting lines find applications across various industries, each benefiting from the precision and efficiency these machines offer.
Construction
In the construction sector, slitting lines are used to produce steel strips for roofing, siding, and framing applications.
- Versatility: The ability to create strips of various widths and thicknesses allows construction companies to meet specific project requirements.
Automotive
The automotive industry relies heavily on slitting lines for cutting steel strips used in body panels, chassis components, and exhaust systems.
- Quality Assurance: High precision in cutting ensures that components fit correctly, enhancing the overall quality of the vehicle.
HVAC
Heating, ventilation, and air conditioning (HVAC) systems also benefit from slitting lines, producing steel strips for ductwork and ventilation systems.
- Efficiency: The ability to produce strips tailored to specific dimensions improves the efficiency of HVAC installations.
Benefits of Steel Slitting Lines
Utilizing steel slitting lines offers numerous advantages that can significantly enhance manufacturing processes.
High Precision
One of the primary benefits of steel slitting lines is their ability to produce precisely cut strips with minimal tolerance deviations.
Increased Efficiency
Automated processes reduce labor requirements and improve overall productivity, allowing manufacturers to meet high demand without compromising quality.
Flexibility
Steel slitting lines can accommodate various types and thicknesses of steel, providing manufacturers with the flexibility to meet diverse customer needs.
Cost Savings
By reducing waste and improving the utilization of raw materials, slitting lines contribute to significant cost savings in the manufacturing process.
Enhanced Safety
The automation of operations minimizes operator exposure to hazards, promoting a safer working environment.
Maintenance and Troubleshooting
Proper maintenance and troubleshooting are crucial for ensuring the optimal performance of steel slitting lines.
Regular Inspection
Routine inspections of key components can help identify wear and tear, allowing for timely repairs and replacements.
Lubrication
Regular lubrication of moving parts is essential to reduce friction and extend the lifespan of the equipment.
Calibration
Calibrating the slitting system is necessary to ensure accurate cuts and maintain the quality of the processed strips.
Troubleshooting Common Issues
Common issues such as misalignment, excessive noise, and equipment malfunctions should be diagnosed and resolved promptly to minimize downtime.
Conclusion
Steel slitting lines are indispensable in the metal processing industry, providing manufacturers with the tools necessary for efficient and precise cutting of steel strips. By understanding the components, types, operations, applications, benefits, and maintenance requirements of these machines, manufacturers can optimize their production processes and enhance product quality. The evolution of steel slitting technology continues to empower industries, ensuring that they meet the ever-growing demands of the market.