Metal Processing with Steel Slitting Lines: Best Practices for Success
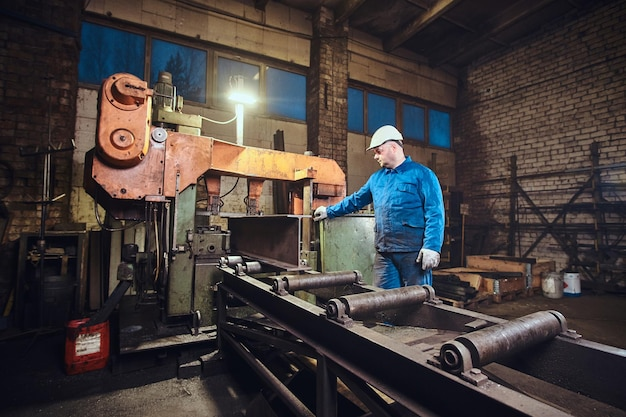
In the realm of metal processing, steel slitting plays a pivotal role in transforming raw materials into usable components. This process involves cutting wide steel coils into narrower strips or coils, tailored to the specific needs of various industries such as automotive, construction, and appliances. Understanding the intricacies of steel slitting lines is essential for manufacturers seeking efficiency, precision, and cost-effectiveness. This article explores the best practices for success in metal processing with steel slitting lines, providing insights into the process, equipment, and strategies that can enhance operational efficiency
Understanding Steel Slitting
Steel slitting is a manufacturing process that involves cutting large coils of steel into narrower strips. This operation is critical for fulfilling the diverse requirements of various applications. The slitting process not only improves the efficiency of metal utilization but also allows for customization in terms of width and gauge.
The Importance of Steel Slitting
- Customization: Steel slitting enables manufacturers to produce strips in specific widths, reducing the need for further processing.
- Efficiency: The process is faster and more cost-effective than traditional cutting methods, such as band saws or shearing.
- Versatility: Slit strips can be used across multiple industries, making them versatile for various applications.
The Steel Slitting Process
Understanding the steel slitting process is crucial for optimizing operations. It involves several steps, from loading the steel coil to packaging the finished strips.
Step-by-Step Breakdown
- Loading the Coil: A crane is used to load the steel coil onto a decoiler, which feeds it into the slitting line.
- Slitting: As the coil moves through the slitting line, rotary blades cut it into the desired widths. This step is done under tension to ensure precision.
- Finishing Touches: After slitting, the coil may undergo edge trimming, leveling, or recoiling before being packaged for shipment.
Key Equipment Used
The efficiency of the slitting process relies heavily on the equipment utilized. Different types of slitting lines cater to various materials and thicknesses:
- Light Gauge Slitting Lines: Designed for softer materials like aluminum and stainless steel.
- Medium Gauge Slitting Lines: Suitable for heavier materials and additional processing tasks.
- Heavy Gauge Slitting Lines: Built for high-strength metals and demanding industrial applications.
Best Practices for Steel Slitting Operations
To achieve optimal results in steel slitting, manufacturers should adhere to several best practices that enhance both efficiency and product quality.
1. Invest in Quality Equipment
High-quality slitting machinery is fundamental for achieving precision and speed. Investing in reliable equipment can significantly impact the operational efficiency of the slitting line.
2. Ensure Proper Maintenance
Regular maintenance of slitting machinery and tools is essential. Dull blades or poorly maintained equipment can lead to inferior edge quality and increased downtime.
- Routine Inspections: Schedule regular checks to assess the condition of blades and machinery.
- Tool Replacement: Replace worn-out tools promptly to maintain cutting quality.
3. Optimize Knife Clearance
Knife clearance is a critical factor in achieving precise slitting results. Proper adjustment of the knife clearance can lead to better edge quality and reduced material waste.
- Testing and Adjusting: Conduct tests to determine the optimal clearance for different materials and thicknesses.
- Documentation: Keep records of settings for future reference and consistency.
4. Train Skilled Operators
Having experienced operators is vital for the success of the slitting process. Operators should be well-trained in handling the machinery and understanding the nuances of different materials.
- Continuous Training: Implement ongoing training programs to keep operators updated on best practices and new technologies.
- Safety Protocols: Ensure that all operators are familiar with safety procedures to minimize accidents.
Types of Slitting Techniques
There are different slitting techniques employed in the industry, each serving specific purposes and applications.
Longitudinal Slitting
This is the most common technique, where wide coils are cut into narrower strips. The cutting direction is parallel to the length of the coil, allowing for continuous processing.
- Applications: Used in roofing, automotive components, and more.
- Benefits: Provides customized widths for various applications.
Crosscut Slitting
In this method, sheets or coils are cut into shorter lengths, with the cutting direction being perpendicular to the coil’s length.
- Applications: Ideal for packaging and manufacturing smaller parts.
- Benefits: Produces individual sheets or shorter strips for specific requirements.
The Role of Quality Assurance
Quality assurance is paramount in ensuring that the slitting process yields high-quality products. Implementing strict quality control measures can help maintain standards.
Quality Control Measures
- Regular Inspections: Conduct thorough inspections of slit strips to ensure they meet specified tolerances.
- Testing Procedures: Implement testing protocols to assess the mechanical properties of the steel post-slitting.
- Documentation: Maintain detailed records of quality checks to track performance over time.
Benefits of Quality Assurance
- Consistency: Ensures that every batch meets quality standards.
- Customer Satisfaction: High-quality products lead to increased customer trust and satisfaction.
Cost-Efficiency in Steel Slitting
Achieving cost-efficiency in steel slitting operations is essential for maintaining competitiveness in the market. Several factors contribute to the overall cost-effectiveness of the process.
1. Streamlined Operations
Optimizing the slitting line for speed and efficiency can significantly reduce operational costs.
- Minimize Downtime: Implement strategies to reduce machine downtime and improve productivity.
- Efficient Layout: Design the workflow to minimize handling and transportation of materials.
2. Material Utilization
Maximizing material utilization reduces waste and lowers costs.
- Custom Widths: Offer customized widths to meet specific client needs, minimizing scrap.
- Recycling Scrap: Implement a recycling program for any leftover materials to recoup costs.
3. Labor Costs
Investing in skilled labor can lead to more efficient operations, ultimately lowering costs.
- Training Programs: Provide comprehensive training to enhance operator skills.
- Performance Incentives: Implement incentive programs to motivate employees to work efficiently.
Choosing the Right Slitting Service Provider
Selecting a reputable slitting service provider is crucial for ensuring quality and reliability. Here are some factors to consider when making this decision.
1. Expertise and Experience
Evaluate the provider’s experience in the industry and their technical capabilities.
- Track Record: Look for providers with a proven history of delivering quality slitting services.
- Specialization: Consider whether they specialize in the specific materials and thicknesses you require.
2. Range of Services
A provider that offers a comprehensive range of services can better meet your needs.
- Customization Options: Ensure they can accommodate custom widths and lengths.
- Additional Services: Look for providers that offer value-added services such as recoiling or deburring.
3. Quality Assurance Practices
Inquire about the quality assurance measures the provider has in place.
- Inspection Protocols: Ask about their inspection procedures and how they maintain quality standards.
- Certifications: Check if they adhere to industry certifications and standards.
Future Trends in Steel Slitting
As technology evolves, the steel slitting industry is also undergoing significant changes. Staying informed about emerging trends can help manufacturers remain competitive.
1. Automation in Slitting Lines
Automation is becoming increasingly prevalent in steel slitting operations. Automated slitting lines offer several advantages:
- Increased Efficiency: Automation can enhance speed and reduce labor costs.
- Consistency: Automated systems provide consistent results, minimizing the risk of human error.
2. Advanced Materials
The demand for advanced materials is growing, and slitting lines must adapt to handle these new challenges.
- High-Strength Steels: Slitting lines will need to accommodate high-strength steels and other innovative materials.
- Sustainability: There is a growing emphasis on sustainable practices, including the use of recycled materials.
3. Data-Driven Decision Making
Data analytics is playing a more significant role in optimizing slitting operations.
- Performance Monitoring: Implementing data analytics can help monitor machine performance and identify areas for improvement.
- Predictive Maintenance: Using data to predict maintenance needs can reduce downtime and enhance productivity.
Conclusion
In conclusion, mastering the steel slitting process is essential for manufacturers aiming to enhance their metal processing capabilities. By investing in quality equipment, training skilled operators, and implementing best practices, companies can achieve significant improvements in efficiency and product quality. As the industry evolves, staying abreast of emerging trends and technologies will be crucial for maintaining a competitive edge. With the right strategies in place, steel slitting can serve as a powerful tool in the metal processing supply chain, enabling manufacturers to meet the demands of a dynamic market.
This article provides a comprehensive overview of the best practices for success in metal processing with steel slitting lines. Each section delves into critical aspects of the process, ensuring that readers gain a thorough understanding of how to optimize their operations effectively.