Optimizing Coil Thickness for Improved Steel Slitting Operations
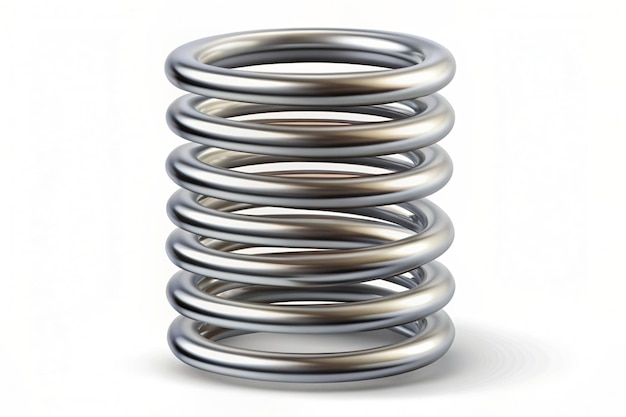
In the realm of metal processing, optimizing coil thickness is crucial for enhancing the efficiency and quality of steel slitting operations. Steel coil slitting machines are integral to various industries, including automotive, construction, and manufacturing. The ability to adjust and optimize the thickness of coils can lead to significant improvements in production outcomes, reducing waste and enhancing product quality. This article delves into the multifaceted aspects of optimizing coil thickness, providing insights and strategies for achieving superior results in steel slitting operations
Importance of Coil Thickness
Coil thickness plays a pivotal role in determining the performance of slitting operations. The thickness affects not only the cutting process but also the machine’s wear and tear, blade life, and overall efficiency. Selecting the appropriate coil thickness is essential for achieving the desired product specifications while minimizing operational challenges.
Factors Influencing Coil Thickness
Several factors can influence the optimal coil thickness for slitting:
- Material Properties: Different materials have varying strengths and ductility, which can affect how they respond to slitting.
- Machine Specifications: Each slitting machine has specific capabilities regarding the thickness it can handle effectively.
- End Product Requirements: The intended use of the slitted steel dictates the necessary thickness.
Understanding these factors is crucial for making informed decisions about coil thickness.
Selecting the Right Coil Thickness
Assessing Production Needs
Before determining the ideal coil thickness, it’s vital to assess production requirements. This involves understanding the end-use of the slitted material and the specifications demanded by clients or industry standards.
- Application-Specific Requirements: Different applications may require different thicknesses. For example, automotive components may necessitate thinner gauges compared to structural steel.
- Consulting with Stakeholders: Engaging with engineers and product designers can provide insights into the required thickness for optimal performance.
Evaluating Machine Capabilities
Not all slitting machines are created equal. Evaluating the capabilities of your equipment is essential for selecting the appropriate coil thickness.
- Manufacturer Specifications: Review the machine’s manual for recommended thickness ranges.
- Performance Testing: Conduct tests on various thicknesses to determine the machine’s efficiency and output quality.
By aligning production needs with machine capabilities, manufacturers can optimize coil thickness effectively.
Setting Up for Optimal Performance
Calibration and Alignment
Proper setup is vital for achieving the best results in steel slitting operations. This includes calibrating the machine and ensuring that all components are aligned correctly.
- Blade Alignment: Misaligned blades can lead to uneven cuts and increased wear.
- Tension Settings: Adjusting the tension on the coils can significantly impact the quality of cuts.
Regularly checking and calibrating these elements ensures that the machine operates at peak performance.
Routine Maintenance Practices
Regular maintenance is essential for keeping the slitting machine in optimal condition, especially when working with varying coil thicknesses.
- Blade Sharpening: Dull blades can compromise the quality of cuts, leading to increased scrap and rework.
- Lubrication: Proper lubrication reduces friction and wear, extending the life of the machine components.
Establishing a consistent maintenance schedule helps prevent unexpected breakdowns and maintains production efficiency.
Optimizing Cutting Parameters
Key Cutting Parameters
To achieve the best results in steel slitting, it’s important to optimize several cutting parameters:
- Blade Speed: The speed at which the blades operate can significantly affect the quality of the cut.
- Feed Rate: Adjusting the feed rate ensures that the material moves through the machine at an optimal speed for the given thickness.
- Tension: Maintaining appropriate tension is crucial for preventing material distortion during the cutting process.
Experimenting with these parameters can lead to improved cutting efficiency and product quality.
Monitoring Performance Metrics
Implementing a system for monitoring performance metrics is essential for optimizing cutting parameters.
- Quality Control: Regularly inspecting the output for defects can help identify issues with cutting parameters.
- Data Analysis: Collecting data on production runs can reveal trends and areas for improvement.
Utilizing performance metrics allows manufacturers to make informed adjustments to their processes.
Efficient Coil Handling Techniques
Streamlining Coil Loading and Unloading
Effective coil handling is critical for maximizing productivity in steel slitting operations. Streamlining loading and unloading processes can reduce downtime and improve workflow.
- Automated Handling Systems: Implementing automated systems for loading and unloading can significantly enhance efficiency.
- Operator Training: Ensuring that operators are well-trained in handling coils reduces the risk of accidents and material damage.
Improving coil handling techniques directly impacts overall production efficiency.
Implementing In-Line Quality Control
Integrating in-line quality control measures can help identify defects early in the process, minimizing waste and rework.
- Edge Detection Systems: Automated edge detection can catch misaligned coils before they enter the cutting phase.
- Thickness Measurement: Using sensors to measure the coil thickness in real-time ensures that only materials meeting specifications are processed.
In-line quality control is an effective strategy for maintaining high standards in production.
Reducing Scrap and Rework
Strategies for Minimizing Waste
Minimizing scrap and rework is essential for improving the cost-effectiveness of steel slitting operations. Implementing the following strategies can help achieve this goal:
- Precision Cutting: Ensuring that cutting parameters are optimized reduces the likelihood of producing scrap material.
- Proper Handling: Careful handling of coils throughout the process prevents damage that could lead to waste.
By focusing on waste reduction, manufacturers can enhance their bottom line.
Continuous Improvement Practices
Establishing a culture of continuous improvement is vital for long-term success in steel slitting operations.
- Feedback Loops: Encouraging feedback from operators can lead to valuable insights for process enhancements.
- Regular Training: Ongoing training ensures that staff remain knowledgeable about best practices and new technologies.
Continuous improvement fosters an environment of efficiency and quality.
Safety Protocols in Steel Slitting Operations
Importance of Safety Measures
Safety should always be a priority in steel slitting operations. Implementing stringent safety protocols protects employees and minimizes the risk of accidents.
- Protective Gear: Ensuring that operators wear appropriate protective equipment is essential for preventing injuries.
- Clean Work Environment: Maintaining a tidy workspace reduces the risk of accidents and improves overall efficiency.
A strong safety culture contributes to a more productive work environment.
Training and Compliance
Regular training sessions on safety procedures are crucial for ensuring compliance and fostering a safe workplace.
- Emergency Procedures: Training employees on how to respond in emergencies can save lives and minimize damage.
- Lockout/Tagout Protocols: Ensuring that all employees are familiar with these protocols prevents accidental machine startups during maintenance.
Prioritizing safety through training and compliance measures creates a safer workplace.
Upgrading Technology for Enhanced Performance
Benefits of Technological Advancements
Investing in advanced technology can significantly enhance the performance of steel slitting operations. Upgrading to modern machines with advanced features can lead to numerous benefits:
- Increased Accuracy: Newer machines often come equipped with precision cutting technology that improves accuracy.
- Reduced Downtime: Advanced monitoring systems can identify potential issues before they lead to breakdowns.
Evaluating the potential return on investment for technology upgrades is essential for making informed decisions.
Features to Consider
When considering upgrades, it’s important to assess which features will provide the most benefit to your operations.
- Automated Adjustments: Machines that offer automated blade adjustments can significantly reduce setup time.
- Real-Time Monitoring: Systems that provide real-time data on machine performance can help identify areas for improvement.
Selecting the right technology can lead to substantial gains in efficiency and productivity.
Training Operators for Optimal Performance
Comprehensive Training Programs
Investing in operator training is crucial for maximizing the effectiveness of steel slitting operations. Comprehensive training programs should cover:
- Machine Operation: Ensuring that operators understand how to use the equipment effectively is essential for preventing errors.
- Maintenance Procedures: Training operators on routine maintenance tasks helps prolong the life of the machinery.
A well-trained workforce is key to achieving optimal performance in steel slitting operations.
Promoting a Culture of Learning
Fostering a culture of continuous learning encourages operators to seek out new knowledge and skills.
- Workshops and Seminars: Regular workshops can provide operators with insights into the latest industry trends and best practices.
- Mentorship Programs: Pairing experienced operators with newer employees can facilitate knowledge transfer and skill development.
A culture of learning contributes to overall operational excellence.
Conclusion
Optimizing coil thickness for improved steel slitting operations is a multifaceted process that encompasses various aspects, from selecting the right materials to implementing effective training programs. By understanding the importance of coil thickness, evaluating machine capabilities, and focusing on continuous improvement, manufacturers can enhance productivity, minimize waste, and ensure high-quality outputs. Prioritizing safety and investing in advanced technology further contribute to the long-term success of steel slitting operations. Through these strategies, businesses can position themselves for sustained growth and profitability in the competitive metal processing industry.