Custom Steel Slitting for Specialized Applications: Efficiency and Precision
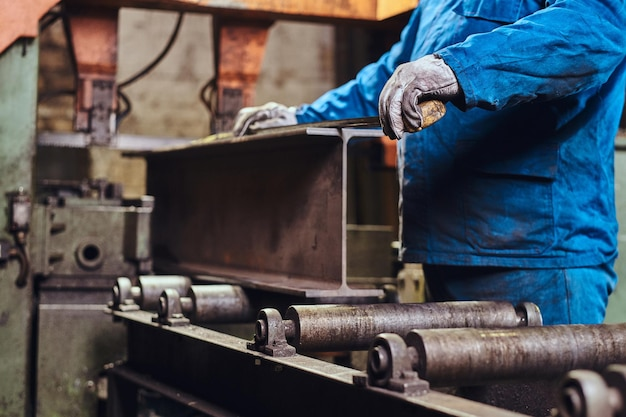
In the world of metal processing, the slitting of steel coils has emerged as a critical operation, serving various industries with tailored solutions. Custom steel slitting is not merely about cutting metal; it’s a sophisticated process that combines precision, efficiency, and adaptability to meet specific customer needs. Whether in construction, automotive, or electrical applications, the ability to produce narrow strips of steel with exact specifications can significantly impact the quality and performance of the final products. This article delves into the intricacies of custom steel slitting, emphasizing its importance and the steps involved in achieving high-quality outputs
Understanding the Steel Slitting Process
What is Steel Slitting?
Steel slitting is a metalworking technique that involves cutting large rolls of steel into narrower strips. This process is essential for industries that require specific widths and thicknesses of steel for their products. The slitting operation employs specialized equipment, including slitting machines equipped with sharp blades designed to ensure clean and precise cuts.
Importance of Customization
The customization aspect of steel slitting is vital. Different industries have unique requirements regarding the dimensions and characteristics of the steel strips they need. Custom steel slitting allows manufacturers to tailor their products to meet these specific demands, enhancing the overall functionality and performance of the final applications.
Key Applications of Steel Slitting
- Construction Industry: Steel slitting is extensively used to produce components such as roofing sheets, wall panels, and structural elements. The narrow strips created through slitting can be transformed into flat sheets suitable for various construction applications.
- Automotive Sector: Within the automotive industry, slitting is crucial for fabricating parts like door frames, brackets, and fenders. The precision of the slitting process ensures that the components fit seamlessly during assembly.
- Electrical Applications: Steel slitting finds its role in manufacturing transformer cores and motor laminations. The narrow strips produced are ideal for stacking and assembling, making them essential for electrical components.
- Packaging Solutions: In the packaging sector, steel slitting is used to create metal containers and cans. The ability to form and weld narrow strips allows for the efficient production of these packaging products.
The Benefits of Custom Steel Slitting
Enhanced Efficiency
Custom steel slitting significantly boosts manufacturing efficiency. By allowing for precise cuts tailored to specific requirements, manufacturers can minimize waste and optimize the use of raw materials. This efficiency translates into cost savings and improved production timelines.
Versatility in Specifications
One of the standout features of custom slitting is its versatility. Manufacturers can produce strips of varying widths and thicknesses, enabling them to meet diverse customer specifications. This adaptability is crucial for industries that require a wide range of steel products.
Precision and Quality Control
Precision is paramount in steel slitting. The process ensures consistent dimensions and quality across all products. Rigorous quality control measures are implemented throughout the slitting operation to verify that each strip meets the required specifications, thereby reducing the likelihood of defects.
Cost-Effectiveness
Custom steel slitting is also a cost-effective solution. By streamlining the production process and reducing material waste, manufacturers can offer competitive pricing on their products. This affordability makes high-quality steel strips accessible to a broader range of industries.
Steps Involved in the Custom Steel Slitting Process
Initial Inquiry and Specification Gathering
The slitting process begins with an inquiry from the customer. Manufacturers gather detailed specifications, including the type of steel, desired width, thickness, and any coating requirements. Understanding these parameters is crucial for ensuring that the final product aligns with the customer’s needs.
Material Sourcing
Once the specifications are confirmed, the next step involves sourcing the appropriate steel coils. Manufacturers often have established relationships with various suppliers, allowing them to select high-quality materials that meet the required standards.
Pricing and Quotation
After sourcing the material, manufacturers calculate the pricing based on several factors, including material costs, processing fees, and market conditions. A detailed quotation is then provided to the customer, ensuring transparency and alignment with their budget.
Coil Inspection
Before proceeding with the slitting operation, a thorough inspection of the steel coil is conducted. This step ensures that the material meets the specified quality and condition requirements. Any discrepancies are addressed before moving forward.
Slitter Head Setup
The setup of the slitter head is a critical phase in the process. Skilled technicians configure the slitter to accommodate the required strip sizes, maintaining the appropriate clearances for the specific gauge of steel being processed. This setup is pivotal for achieving consistent results.
Recoiling Arbor Preparation
The recoiling arbor is prepared to handle the slit strips. Operators configure the arbor to ensure efficient recoiling, which is vital for maintaining the integrity of the strips during the process.
Coil Loading and Over Arm Placement
To initiate the slitting process, the coil is loaded onto the uncoiler machine. An overhead crane is typically employed for this task. The overarm is positioned to secure the coil, preventing any unwinding during slitting.
The Slitting Operation
With everything in place, the slitting process begins. The coil is fed through the slitter head, where rotating blades cut it into narrower strips. The precision of the blades ensures clean cuts, resulting in uniform steel strips.
Scrap Management
During slitting, scrap material is often generated. An efficient scrap management system is implemented to handle this waste, ensuring a clean work environment and maximizing material utilization.
Feeding Slit Steel to Recoiler
After slitting, the strips are fed into the recoiler, which winds them into individual coils. This step is crucial for maintaining the quality and consistency of the final product.
Quality Control Measures
Quality control is a continuous process throughout the slitting operation. Measurements of gauge, width, and surface quality are taken to ensure that the final products meet the specified standards.
Packaging and Delivery
Once the coils pass quality checks, they are packaged according to customer specifications. Proper packaging is essential for protecting the steel during transportation. Finally, the coils are shipped using reliable logistics partners to ensure timely delivery.
Advanced Technologies in Steel Slitting
Automation in Slitting Processes
The integration of automation technology in steel slitting has revolutionized the industry. Automated systems enhance precision and efficiency, reducing the potential for human error. This advancement allows for faster production rates while maintaining high-quality standards.
State-of-the-Art Equipment
Modern slitting lines are equipped with advanced machinery designed to handle various materials and thicknesses. These machines are capable of producing high-quality strips with minimal burr, ensuring that the finished products meet exact specifications.
Data-Driven Decision Making
Utilizing data analytics in the slitting process enables manufacturers to monitor performance metrics and identify areas for improvement. This approach enhances operational efficiency and helps in making informed decisions regarding production strategies.
The Future of Custom Steel Slitting
Industry Trends
As industries continue to evolve, the demand for customized steel products is expected to grow. Manufacturers will need to adapt to these changes by investing in advanced technologies and refining their processes to meet ever-changing customer needs.
Sustainability Practices
Sustainability is becoming increasingly important in metal processing. Custom steel slitting operations are likely to adopt more eco-friendly practices, such as reducing waste and optimizing energy consumption, to align with global sustainability goals.
Expanding Market Opportunities
The versatility of custom steel slitting opens up new market opportunities across various sectors. As industries seek specialized solutions, manufacturers who can provide high-quality, customized products will find themselves in a favorable position.
Conclusion
Custom steel slitting is a vital process that enhances efficiency and precision across multiple industries. By understanding the intricacies of the slitting process and the benefits it offers, manufacturers can deliver tailored solutions that meet the specific needs of their customers. As technology continues to advance and market demands evolve, the future of custom steel slitting looks promising, paving the way for innovation and growth in the metal processing industry.
This article provides a comprehensive overview of custom steel slitting, emphasizing its significance, processes, and future trends. By focusing on efficiency and precision, manufacturers can navigate the complexities of the industry while meeting the diverse needs of their clients.