Enhancing Productivity in Steel Coil Slitting with Edge Conditioning
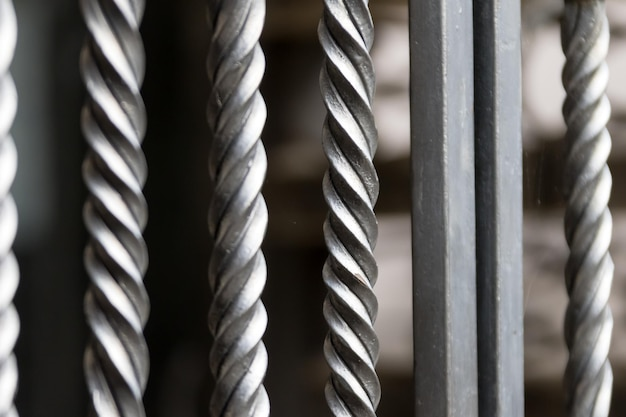
The steel processing industry has undergone significant transformations in recent years, driven by the need for efficiency and precision. Among the critical processes, steel coil slitting stands out as a vital operation that can greatly influence productivity and cost-effectiveness. One of the key enhancements in this domain is edge conditioning, which plays a crucial role in improving the quality and usability of slit coils. In this article, we will delve into the intricacies of steel coil slitting and edge conditioning, exploring their benefits, techniques, and applications
Understanding Steel Coil Slitting
Steel coil slitting is a process that involves cutting wide coils of steel into narrower strips. This procedure is essential for various applications across multiple industries, including automotive, aerospace, and construction. The slitting process not only reduces the material to desired widths but also ensures that the finished product meets specific tolerances and quality standards.
The Slitting Process Explained
The slitting operation typically involves feeding a large master coil into a slitting machine, where it is cut into narrower strips using sharp blades. The blades penetrate the coil, creating multiple strips that are then recoiled into smaller coils. This process is crucial for manufacturers who require precise dimensions for their products.
Benefits of Steel Coil Slitting
- Increased Efficiency: By producing narrower strips, manufacturers can optimize their production lines and reduce waste.
- Cost-Effectiveness: Slitting allows for better material utilization, which can lead to significant cost savings.
- Customization: Manufacturers can tailor the width and thickness of the strips to meet specific customer requirements.
The Role of Edge Conditioning
Edge conditioning, also referred to as edge rounding or deburring, is a vital step that follows the slitting process. This procedure involves smoothing or rounding the sharp edges of the slit strips to enhance their safety and usability.
Importance of Edge Conditioning
- Safety: Sharp edges can pose risks during handling and processing. Edge conditioning mitigates these hazards, making the material safer for workers.
- Quality Improvement: Smoother edges contribute to a higher-quality product, which is essential for applications that demand precision.
- Enhanced Performance: Conditioned edges can improve the performance of the final product, especially in applications requiring welding or further processing.
Techniques Used in Edge Conditioning
Several techniques are employed in edge conditioning, each tailored to specific materials and applications. Some of the most common methods include:
- Deburring: This technique involves removing sharp edges and burrs left after slitting, enhancing the overall finish of the metal.
- Rounding: The edges are rounded to prevent chipping and enhance safety during handling.
- Custom Shapes: Edge conditioning can also be customized to create specific shapes that suit particular applications.
Types of Steel Suitable for Slitting and Edge Conditioning
Not all steel types are created equal when it comes to slitting and edge conditioning. Different grades of steel exhibit varying properties that influence their compatibility with these processes.
Common Steel Grades
- Stainless Steel: Known for its corrosion resistance, stainless steel is often used in applications where hygiene is paramount.
- Nickel Alloys: These materials are favored for their strength and resistance to heat and corrosion.
- High Strength Low Alloy (HSLA): HSLA steels are designed to provide better mechanical properties and are often used in structural applications.
- High Carbon Steel: This type of steel is known for its strength and hardness, making it suitable for cutting tools and other applications.
- Low Carbon Cold Rolled Steel: This material is easy to work with and is commonly used in applications where formability is essential.
Enhancing Productivity through Edge Conditioning
Integrating edge conditioning into the slitting process can significantly enhance productivity. By ensuring that the edges of the slit coils are smooth and safe, manufacturers can streamline their operations and reduce downtime.
Streamlining Operations
- Reduced Handling Time: Smooth edges mean that workers can handle materials more quickly and safely, minimizing the time spent on each operation.
- Fewer Defects: Properly conditioned edges reduce the likelihood of defects in the final product, leading to higher quality and fewer returns.
- Improved Machine Performance: Edge conditioning can enhance the performance of downstream machinery, allowing for faster and more efficient processing.
Cost Savings
- Material Utilization: By minimizing waste during the slitting and conditioning processes, manufacturers can maximize their material utilization.
- Lower Labor Costs: Streamlined operations lead to reduced labor costs, as workers can accomplish more in less time.
- Enhanced Product Lifespan: Conditioned edges can prolong the lifespan of the final product, reducing the need for replacements and repairs.
Applications of Slit Coils with Edge Conditioning
The applications of slit coils that have undergone edge conditioning are vast and varied. From automotive components to medical devices, the benefits of high-quality slit coils are evident across multiple industries.
Key Industries Utilizing Slit Coils
- Automotive: Slit coils are used for various components, including brackets, frames, and body panels, where precision and safety are paramount.
- Aerospace: In this industry, high-quality materials are essential for ensuring the safety and reliability of aircraft components.
- Medical Devices: The medical field demands materials that are not only precise but also safe for use in sensitive applications, making edge conditioning crucial.
Specific Applications
- Surgical Instruments: Precision-cut and conditioned stainless steel strips are essential for manufacturing surgical tools that require high levels of accuracy.
- Flexible Metal Hoses: These products benefit from conditioned edges that enhance their durability and performance in various applications.
- Decorative Elements: In the automotive industry, conditioned coils can serve as design elements, contributing to both aesthetics and functionality.
The Future of Steel Coil Slitting and Edge Conditioning
As industries continue to evolve, so too will the processes involved in steel coil slitting and edge conditioning. Innovations in technology and materials will drive improvements in efficiency, safety, and product quality.
Technological Advancements
- Automation: The integration of automated systems in slitting and edge conditioning processes can enhance productivity and reduce human error.
- Advanced Materials: New steel grades and coatings may offer improved performance characteristics, further enhancing the benefits of slitting and conditioning.
- Data-Driven Insights: Utilizing data analytics can help manufacturers optimize their processes and make informed decisions regarding their operations.
Sustainability Considerations
- Waste Reduction: By improving material utilization and minimizing waste, manufacturers can contribute to more sustainable practices within the industry.
- Energy Efficiency: Innovations in machinery and processes can lead to reduced energy consumption, aligning with global sustainability goals.
Conclusion
The integration of edge conditioning into the steel coil slitting process represents a significant advancement in the industry. By enhancing productivity, improving safety, and ensuring high-quality products, manufacturers can better meet the demands of today’s competitive landscape. As technology continues to evolve, the future of steel coil processing looks promising, paving the way for further innovations and improvements.
This article provides an in-depth exploration of enhancing productivity in steel coil slitting through edge conditioning, highlighting the importance of these processes in various industries. By focusing on efficiency, safety, and quality, manufacturers can optimize their operations and remain competitive in a rapidly changing market.