Heavy Gauge Steel Slitting: Maximizing Performance in Tough Environments
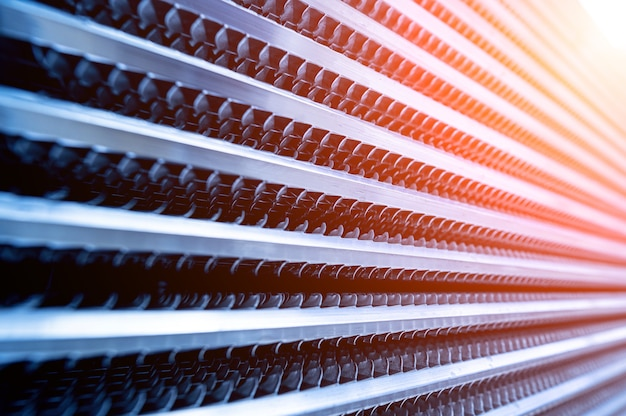
In the ever-evolving landscape of manufacturing, heavy gauge steel slitting has emerged as a critical process for achieving precision and efficiency. As industries demand higher quality standards and faster turnaround times, understanding the intricacies of slitting operations becomes paramount. This article delves into the essential factors that contribute to optimizing performance in heavy gauge steel slitting, exploring everything from blade technology to operational best practices
Understanding Heavy Gauge Steel Slitting
Heavy gauge steel slitting involves cutting wide coils of steel into narrower strips. This process is essential for various applications, including automotive, construction, and manufacturing sectors. The efficiency of slitting operations directly impacts production costs and product quality.
The Importance of Precision
Precision in slitting is crucial. Inaccurate cuts can lead to increased waste, higher costs, and potential delays in production. Manufacturers must invest in high-quality machinery and tools to ensure that each strip meets the required specifications.
Applications of Heavy Gauge Steel
Heavy gauge steel is utilized in multiple industries, including:
- Construction: Used for beams, columns, and reinforcements.
- Automotive: Essential for vehicle frames and components.
- Manufacturing: Critical in producing machinery and equipment.
Understanding the applications helps manufacturers tailor their slitting processes to meet specific industry needs.
Key Components of Heavy Gauge Steel Slitting
To maximize efficiency in heavy gauge steel slitting, several components must be considered. Each element plays a significant role in the overall effectiveness of the operation.
Blade Quality
The quality of the blades used in slitting is foundational to achieving clean cuts. High-grade blades reduce the frequency of replacements and minimize downtime.
- Material: Blades made from high-speed steel or carbide offer superior durability.
- Coatings: Advanced coatings can enhance blade longevity and reduce friction.
Tension Control
Maintaining optimal tension during the slitting process is essential for achieving uniform strip thickness. Advanced tension control systems help prevent defects and ensure consistent quality.
- Automatic Tension Adjustments: Implementing automated systems can significantly enhance precision.
- Monitoring Systems: Real-time monitoring ensures that tension remains stable throughout the process.
Edge Quality
The presence of burrs on the edges of slitted strips can compromise quality. Employing high-quality tooling and effective tension control can minimize burr formation.
- Tooling Selection: Choosing the right tooling is crucial for achieving smooth edges.
- Post-Slitting Processes: Implementing finishing processes can further refine edge quality.
Operational Best Practices
To achieve maximum efficiency in heavy gauge steel slitting, manufacturers must adopt a set of best practices that streamline operations.
Regular Maintenance
Regular maintenance of slitting equipment is vital for preventing breakdowns and ensuring optimal performance. A proactive maintenance schedule can extend the lifespan of machinery.
- Daily Checks: Operators should perform daily inspections to identify potential issues.
- Scheduled Overhauls: Regularly scheduled maintenance can prevent costly downtime.
Training and Skill Development
Investing in employee training ensures that operators are well-versed in the latest techniques and technologies. Skilled operators can identify and resolve issues more effectively.
- Workshops and Seminars: Regular training sessions can keep staff updated on industry advancements.
- Cross-Training: Encouraging cross-training can enhance flexibility within the workforce.
Quality Control Measures
Implementing robust quality control measures is essential for maintaining high standards in slitting operations. Automated inspection systems can provide real-time feedback on product quality.
- Statistical Process Control (SPC): Utilizing SPC can help identify trends and variations in the slitting process.
- Feedback Loops: Establishing feedback loops ensures continuous improvement in quality.
Advanced Technologies in Steel Slitting
Embracing advanced technologies can significantly enhance the efficiency of heavy gauge steel slitting.
Automation
Automation in slitting operations can streamline processes and reduce labor costs. Automated systems can handle material loading, cutting, and packaging.
- Robotic Systems: Robotic arms can assist in loading and unloading materials, enhancing speed and safety.
- Automated Quality Checks: Integrating automated inspection systems can ensure consistent quality throughout the process.
Real-Time Monitoring
Implementing real-time monitoring systems allows manufacturers to track performance metrics and make adjustments on the fly. This capability can lead to significant improvements in efficiency.
- Data Analytics: Utilizing data analytics can provide insights into operational performance and identify areas for improvement.
- Predictive Maintenance: Monitoring equipment conditions can help predict failures before they occur, reducing downtime.
Material Selection and Its Impact
The choice of materials used in heavy gauge steel slitting can significantly affect the process’s efficiency and quality.
Collaborating with Reputable Suppliers
Partnering with trusted suppliers ensures that manufacturers receive high-quality materials tailored to their specific needs.
- Material Specifications: Understanding the properties of the steel being processed can help optimize slitting parameters.
- Supplier Relationships: Strong relationships with suppliers can lead to better pricing and availability of materials.
Understanding Material Properties
Different types of steel have varying properties that affect slitting performance. Knowledge of these properties allows manufacturers to adjust their processes accordingly.
- Ductility and Hardness: Understanding these characteristics can help in selecting appropriate slitting speeds and blade types.
- Thickness Variations: Adjusting processes based on thickness variations can prevent defects and improve efficiency.
Safety Considerations in Steel Slitting
Prioritizing safety in heavy gauge steel slitting operations is essential for protecting personnel and ensuring uninterrupted production.
Implementing Safety Protocols
Establishing comprehensive safety protocols can minimize risks associated with slitting operations.
- Personal Protective Equipment (PPE): Ensuring that all personnel are equipped with appropriate PPE can reduce the likelihood of injuries.
- Emergency Procedures: Clearly defined emergency procedures can enhance response times in critical situations.
Ergonomics in Equipment Design
Designing equipment with ergonomics in mind can reduce strain on operators and improve overall safety.
- Adjustable Workstations: Providing adjustable workstations can enhance comfort for operators.
- User-Friendly Controls: Intuitive control systems can reduce operator fatigue and improve efficiency.
Environmental Considerations
As sustainability becomes increasingly important, manufacturers must consider the environmental impact of heavy gauge steel slitting operations.
Waste Management
Implementing effective waste management strategies can minimize environmental impact and reduce costs.
- Recycling Scrap: Establishing recycling programs for scrap metal can contribute to sustainability efforts.
- Efficient Material Usage: Optimizing slitting processes to minimize waste can enhance profitability.
Energy Efficiency
Investing in energy-efficient machinery can reduce operational costs and lower the carbon footprint of slitting operations.
- Energy Monitoring Systems: Implementing systems to monitor energy usage can identify areas for improvement.
- Upgrading Equipment: Replacing outdated machinery with energy-efficient models can lead to significant savings.
Future Trends in Heavy Gauge Steel Slitting
As technology continues to evolve, several trends are shaping the future of heavy gauge steel slitting.
Industry 4.0
The integration of Industry 4.0 principles is revolutionizing manufacturing processes, including steel slitting.
- Smart Manufacturing: Utilizing IoT devices can enhance connectivity and data sharing across operations.
- Predictive Analytics: Leveraging predictive analytics can optimize maintenance schedules and improve efficiency.
Advanced Materials
The development of advanced materials, such as high-strength steels, is changing the landscape of slitting operations.
- Material Innovations: Understanding the properties of new materials can help manufacturers adapt their processes.
- Customization: The ability to customize slitting processes for different materials will become increasingly important.
Conclusion
Maximizing performance in heavy gauge steel slitting requires a comprehensive understanding of various factors, from blade quality to operational best practices. By embracing advanced technologies, prioritizing safety, and focusing on sustainability, manufacturers can enhance efficiency and product quality. As the industry continues to evolve, staying informed about emerging trends and technologies will be essential for maintaining a competitive edge.
By implementing these strategies, manufacturers can ensure that their heavy gauge steel slitting operations are not only efficient but also capable of meeting the demands of an ever-changing market. Investing in quality, training, and technology is the key to success in this critical area of manufacturing.