Metal Fabrication Efficiency: Maximizing Productivity with Proper Coil Thickness
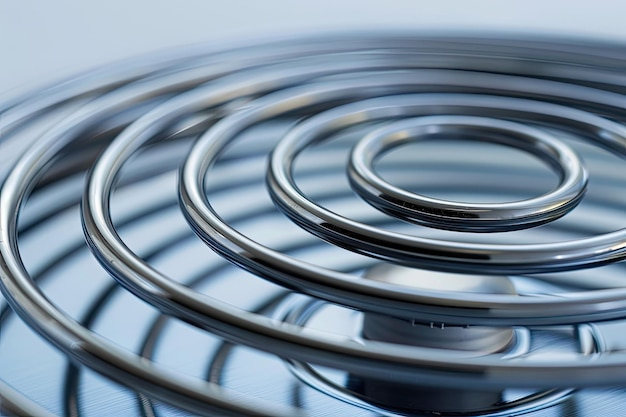
In the realm of metal fabrication, the efficiency of production processes is crucial for maintaining competitiveness. One of the pivotal factors influencing this efficiency is the thickness of metal coils used during fabrication. Understanding how coil thickness impacts productivity can lead to enhanced operational performance and cost savings. This article explores various aspects of metal fabrication efficiency, focusing on maximizing productivity through the optimal selection of coil thickness.
Understanding Coil Thickness in Metal Fabrication
Coil thickness refers to the gauge of the metal used in manufacturing processes such as roll forming, stamping, and cutting. The thickness of the coil significantly affects the mechanical properties of the final product, influencing everything from strength to flexibility.
Importance of Coil Thickness
- Mechanical Properties: The thickness of the coil directly correlates with the strength and durability of the finished product. Thicker coils generally provide greater strength but may compromise flexibility.
- Production Efficiency: Selecting the right coil thickness can streamline production processes. Thinner coils may require less energy to manipulate, while thicker coils might necessitate more robust machinery.
- Cost Implications: The choice of coil thickness can also impact material costs. Thicker coils may be more expensive, but they could reduce the need for additional processing steps, ultimately saving money.
Typical Coil Thickness Ranges
Coils are manufactured in various thicknesses, typically ranging from 0.2 mm to over 10 mm. The selection of coil thickness should be aligned with the specific requirements of the project, including:
- Application Requirements: Different applications demand different thicknesses. For example, automotive components often utilize thinner coils for weight reduction, while structural applications may require thicker materials for enhanced strength.
- Material Type: The type of metal also plays a role in determining the appropriate thickness. For instance, high-strength steel may be used in thinner gauges without sacrificing performance.
The Role of Coil-Fed Processing
Coil-fed processing is a method that utilizes coiled metal strips instead of pre-cut sheets, offering several advantages in terms of efficiency and waste reduction.
Benefits of Coil-Fed Processing
- Reduced Waste: Coil-fed systems produce less scrap compared to traditional sheet-fed methods. This reduction in waste can lead to significant cost savings over time.
- Continuous Production: By utilizing coils, manufacturers can maintain a continuous flow of production, minimizing downtime associated with sheet changes.
- Flexibility: Coil-fed systems can be easily adjusted to accommodate various thicknesses and widths, providing versatility in production.
Considerations for Implementing Coil-Fed Systems
When transitioning to coil-fed processing, it is essential to consider:
- Equipment Requirements: Ensure that the machinery is compatible with coil-fed systems. This may involve upgrading existing equipment or investing in new technology.
- Training and Skills: Operators must be trained to work with coil-fed systems, as they may differ from traditional methods in terms of setup and operation.
Selecting the Right Materials
Choosing the appropriate materials is critical for maximizing efficiency in metal fabrication. The selection of metal types and thicknesses can significantly influence the outcome of projects.
Material Properties to Consider
- Strength: The chosen material must meet the required strength specifications for the application. High-strength materials may allow for thinner gauges without compromising performance.
- Corrosion Resistance: In environments where corrosion is a concern, selecting materials with inherent resistance can prolong the lifespan of the final product.
- Aesthetic Qualities: For applications where appearance matters, consider materials that can be finished or coated to enhance visual appeal.
Collaborative Material Selection
Engaging in early discussions with suppliers can facilitate better material selection. This collaboration ensures that the chosen materials align with both production capabilities and design requirements.
Optimizing Tooling and Equipment
The efficiency of metal fabrication processes is heavily influenced by the tooling and machinery used. Proper maintenance and selection of equipment can enhance productivity.
Importance of Well-Maintained Tools
- Quality Assurance: Tools that are regularly maintained ensure consistent quality in the finished products. Dull or damaged tools can lead to defects and increased scrap rates.
- Downtime Reduction: Well-maintained equipment is less likely to fail, reducing unplanned downtime and keeping production schedules on track.
Evaluating Equipment Condition
Before committing to a vendor, it is advisable to inspect their equipment. Key aspects to review include:
- Preventive Maintenance Records: Ensure that the vendor follows a rigorous maintenance schedule to keep equipment in optimal condition.
- Capability Documentation: Request documentation that demonstrates the vendor’s ability to produce parts consistently and accurately.
Assessing Part Complexity
The complexity of the parts being fabricated can significantly influence the choice of coil thickness and processing methods.
Understanding Complexity in Design
- Design Specifications: More intricate designs may require specialized tooling and equipment, which can affect production speed and costs.
- Tolerance Levels: Tighter tolerances can complicate the fabrication process. It may be beneficial to loosen tolerances where possible to enhance manufacturability.
Balancing Complexity and Efficiency
When designing parts, consider the following:
- Simplicity: Strive for designs that minimize complexity without sacrificing functionality. This can lead to faster production and lower costs.
- Prototyping: Utilize prototyping to test designs before committing to full-scale production. This can help identify potential issues early in the process.
Managing Tolerances Effectively
Tolerances play a crucial role in the metal fabrication process. Proper management of tolerances can enhance efficiency and reduce costs.
The Impact of Tight Tolerances
- Increased Costs: Setting overly tight tolerances can lead to higher tooling costs, extended development times, and the need for premium materials.
- Tool Wear and Tear: Tight tolerances can lead to accelerated wear on tooling, necessitating more frequent replacements and repairs.
Strategies for Tolerance Management
- Functional Tolerances: Focus on functional tolerances that align with the end-use of the product rather than blanket tolerances that may be unnecessarily stringent.
- Collaboration with Vendors: Engage with vendors to determine the most appropriate tolerances for specific parts, balancing precision with manufacturability.
Leveraging Technology in Metal Fabrication
Advancements in technology continue to shape the landscape of metal fabrication, offering new opportunities for enhancing efficiency.
Automation and Robotics
- Increased Speed: Automated systems can significantly speed up production processes, allowing for higher output rates.
- Consistency: Automation reduces the variability associated with human operators, leading to more consistent quality in the finished products.
Advanced Software Solutions
Utilizing software for design and production planning can streamline operations. Key benefits include:
- Enhanced Design Capabilities: Advanced software can facilitate complex design processes, allowing for greater creativity and innovation.
- Efficient Production Scheduling: Software solutions can optimize production schedules, ensuring that resources are allocated effectively.
Continuous Improvement Practices
Implementing continuous improvement practices is essential for maintaining efficiency in metal fabrication.
The Role of Lean Manufacturing
- Waste Reduction: Lean principles focus on minimizing waste in all forms, from materials to time. This can lead to significant cost savings and improved productivity.
- Employee Involvement: Engaging employees in continuous improvement efforts fosters a culture of innovation and accountability.
Regular Performance Evaluations
Conducting regular evaluations of production processes can identify areas for improvement. Key metrics to assess include:
- Cycle Times: Monitor cycle times to identify bottlenecks and areas for optimization.
- Quality Control: Implement robust quality control measures to catch defects early in the production process.
Conclusion
Maximizing productivity in metal fabrication hinges on a comprehensive understanding of coil thickness and its implications for the production process. By selecting the appropriate materials, optimizing tooling and equipment, managing tolerances effectively, and leveraging technology, manufacturers can enhance efficiency and reduce costs. Embracing continuous improvement practices further solidifies a commitment to excellence in metal fabrication, ensuring that companies remain competitive in an ever-evolving industry.
This article provides a comprehensive overview of how to maximize productivity in metal fabrication through proper coil thickness selection and related practices. If you have any specific requests for additional sections or modifications, feel free to ask!