The Manufacturing Process of Flat Bar: From Raw Material to Finished Product
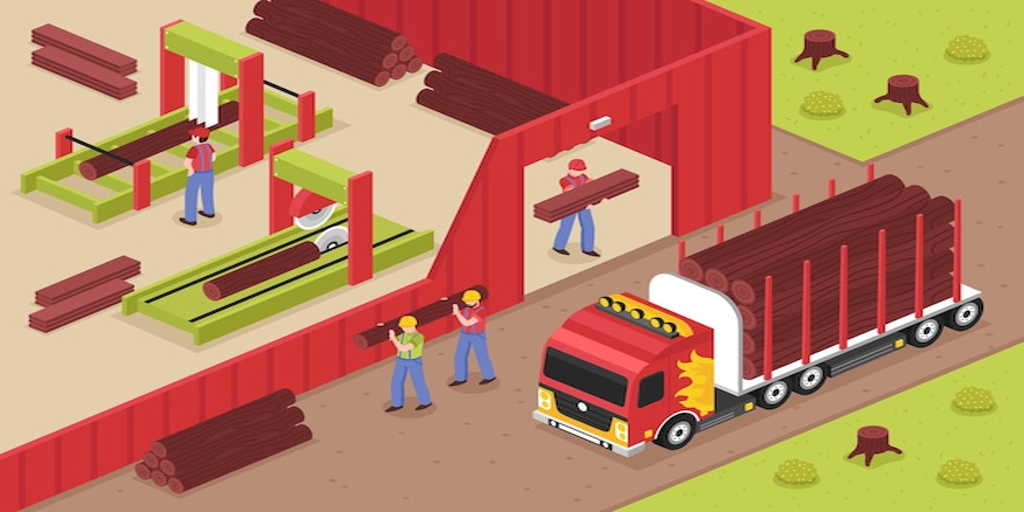
The journey of flat bar manufacturing is a fascinating blend of raw material transformation, advanced technology, and meticulous craftsmanship. Flat bars, often characterized by their rectangular shape and versatile applications, are essential components in various industries, including construction, automotive, and machinery. Understanding the manufacturing process not only highlights the complexity involved but also emphasizes the importance of quality and precision in producing these vital materials. In this article, we will explore the entire process, from raw material extraction to the final product, shedding light on each stage along the way.
Raw Material Acquisition
The foundation of flat bar production begins with sourcing high-quality raw materials. The primary components involved in this process are iron ore, coal, and limestone. Each of these materials plays a crucial role in the subsequent stages of manufacturing.
Iron Ore
Iron ore is the backbone of flat bar manufacturing, as it is the primary source of iron. The most commonly utilized varieties include hematite and magnetite. These ores are mined from extensive deposits and transported to steel mills, where they undergo processing to extract iron. The quality of iron ore significantly influences the properties of the final flat bar product, making it essential to select high-grade ores.
Coal
Coking coal is another vital ingredient in the production of flat bars. This specific type of coal is heated in a low-oxygen environment to produce coke, a carbon-rich material that generates the intense heat required for smelting iron ore. The coke serves as both a fuel and a reducing agent, facilitating the conversion of iron ore into molten iron.
Limestone
Limestone is added to the mix to eliminate impurities during the steel-making process. It acts as a flux, binding with unwanted elements such as sulfur and phosphorus, which can compromise the quality of the final product. The removal of these impurities is crucial for ensuring that the flat bars possess the desired mechanical properties.
The Coke Production Process
Following the acquisition of raw materials, the next step involves the transformation of coal into coke. This process is essential for generating the high temperatures needed in the blast furnace.
Heating Coal
Coke production begins with heating coking coal in a coke oven, where it is subjected to elevated temperatures in a low-oxygen environment. This process drives off volatile compounds, leaving behind a dense, carbon-rich material known as coke. The absence of oxygen prevents combustion, allowing the coke to maintain its integrity while generating significant heat.
Characteristics of Coke
Coke is a crucial component in the steel-making process, as it burns hotter and cleaner than regular coal. Its high carbon content makes it an excellent reducing agent, enabling the conversion of iron ore into molten iron in the subsequent stages of production. The quality of coke directly impacts the efficiency of the blast furnace and the quality of the resulting iron.
Blast Furnace Operation
The blast furnace is a towering structure that plays a pivotal role in the conversion of iron ore into molten iron. This process is where the raw materials come together to initiate the transformation into flat bar steel.
Layering Materials
Inside the blast furnace, layers of iron ore, coke, and limestone are introduced. The furnace is lined with heat-resistant bricks to withstand the extreme temperatures generated during the process. The arrangement of these materials is crucial for ensuring efficient reactions.
Air Injection
Hot air is blasted into the furnace from the bottom at temperatures ranging from 1,500 to 2,200 degrees Celsius. This high-temperature environment ignites the coke, producing carbon monoxide gas. The carbon monoxide reacts with the iron ore, reducing it to molten iron while forming a liquid slag that floats atop the molten metal.
Tapping Molten Iron
As the iron ore melts, the impurities rise to the surface, forming slag. The purified molten iron, known as pig iron, collects at the bottom of the furnace and is tapped off. Although pig iron is rich in carbon and impurities, it serves as the primary feedstock for the next stage of the manufacturing process.
Basic Oxygen Steelmaking (BOS)
Once the pig iron is obtained, it undergoes the basic oxygen steelmaking process to refine it into steel suitable for flat bar production. This stage is critical for reducing carbon content and enhancing the material’s properties.
Oxygen Injection
In the basic oxygen furnace, molten pig iron is poured in, and pure oxygen is injected at high pressure. This reaction generates carbon dioxide, effectively lowering the carbon content of the iron. The precise control of oxygen flow and timing is essential to achieve the desired carbon levels for various steel grades.
Flux Addition
To aid in the removal of impurities, fluxes such as limestone are introduced into the furnace. As the flux reacts with the carbon and impurities, it forms slag, which is subsequently removed. This refining process results in high-quality liquid steel with significantly reduced carbon content compared to pig iron.
Alloying Elements
At this stage, alloying elements such as manganese, chromium, or nickel can be added to tailor the steel’s properties. These additions enhance characteristics like strength, corrosion resistance, and ductility, allowing for the production of various steel grades, including stainless steel.
Casting the Steel
Once the steel has been refined, it is ready for casting into the desired shapes. This process is crucial for determining the final dimensions and characteristics of the flat bars.
Mould Preparation
The molten steel is poured into moulds to create slabs, billets, or blooms, depending on the intended application. Modern steel plants often utilize continuous casting methods, where the molten steel is continuously poured into a water-cooled mould, allowing it to solidify as it moves downward.
Continuous Casting Process
In continuous casting, the steel solidifies in a controlled environment, resulting in long strands of steel that can be cut to the required length. This method enhances efficiency and reduces waste compared to traditional casting methods, which involve pouring steel into individual ingots.
Forming and Shaping
After casting, the solidified steel needs to undergo further shaping to achieve the final flat bar dimensions. This process typically involves hot and cold rolling.
Hot Rolling
Hot rolling is conducted by heating the steel above its recrystallization temperature and passing it through large rollers. This method allows for the production of flat bars with varying thicknesses and widths, making it suitable for applications such as beams, sheets, and structural components.
Cold Rolling
In some cases, cold rolling is employed, where the steel is processed at room temperature. This technique results in a smoother surface finish and more precise dimensions, making it ideal for applications requiring high-quality aesthetics and tolerances.
Surface Treatment and Finishing
Once the flat bars have been shaped, they undergo a series of finishing processes to enhance their quality and prepare them for various applications.
Pickling
One of the initial steps in surface treatment is pickling, where the steel is soaked in an acid solution to remove surface impurities such as rust or scale. This process ensures that the steel has a clean surface, which is essential for subsequent treatments.
Galvanization
To protect the steel from corrosion, galvanization may be applied. This involves coating the flat bars with a layer of zinc, providing a barrier against rust and extending the material’s lifespan, especially in outdoor or harsh environments.
Heat Treatment
Heat treatment processes, such as quenching and tempering, are employed to enhance the mechanical properties of the flat bars. These treatments improve strength, ductility, and toughness, ensuring that the final product meets the required specifications for its intended use.
Quality Control and Testing
Before the flat bars are dispatched for use, they undergo rigorous quality control testing to ensure they meet industry standards and specifications.
Mechanical Testing
Common mechanical tests include tensile testing, which measures the material’s strength, and hardness testing, which assesses resistance to indentation. These tests help verify that the flat bars possess the necessary properties for their intended applications.
Dimensional Tolerances
Dimensional accuracy is crucial in flat bar manufacturing. Quality control measures ensure that the bars meet specified tolerances for width, thickness, and length. This attention to detail is vital for ensuring compatibility with other components in construction and manufacturing processes.
Non-Destructive Testing
Non-destructive testing methods, such as ultrasonic testing, are employed to detect internal flaws or cracks in the steel. These techniques help identify potential issues without compromising the integrity of the flat bars, ensuring that only high-quality products reach the market.
Applications of Flat Bars
Flat bars are versatile materials used across various industries, thanks to their unique properties and characteristics. Their applications range from structural components to specialized tools.
Construction Industry
In the construction sector, flat bars serve as essential structural elements in buildings, bridges, and other infrastructure projects. Their strength and durability make them ideal for use in frames, supports, and reinforcements.
Automotive Manufacturing
Flat bars are also widely utilized in the automotive industry, where they are employed in the production of vehicle frames, chassis components, and various mechanical parts. Their ability to withstand significant loads and stresses makes them suitable for critical applications in vehicles.
Machinery and Equipment
Flat bars find applications in the manufacturing of machinery and equipment, where they are used to create components such as brackets, frames, and supports. Their versatility allows for customization to meet specific design requirements.
Conclusion
The manufacturing process of flat bars is a sophisticated journey that begins with raw material extraction and culminates in the production of high-quality finished products. Each stage, from coke production to quality control testing, plays a vital role in ensuring that the final flat bars meet the necessary specifications for their intended applications. As industries continue to evolve, the demand for flat bars will remain strong, highlighting the importance of innovation and quality in the manufacturing process. Understanding this process not only enhances appreciation for the materials we use daily but also underscores the critical role that flat bars play in various sectors of the economy.
As we move forward, the ongoing advancements in steel manufacturing technology will likely lead to even greater efficiency and sustainability in the production of flat bars, ensuring their relevance in the future.