Understanding Steel Gauge: What Does It Mean?
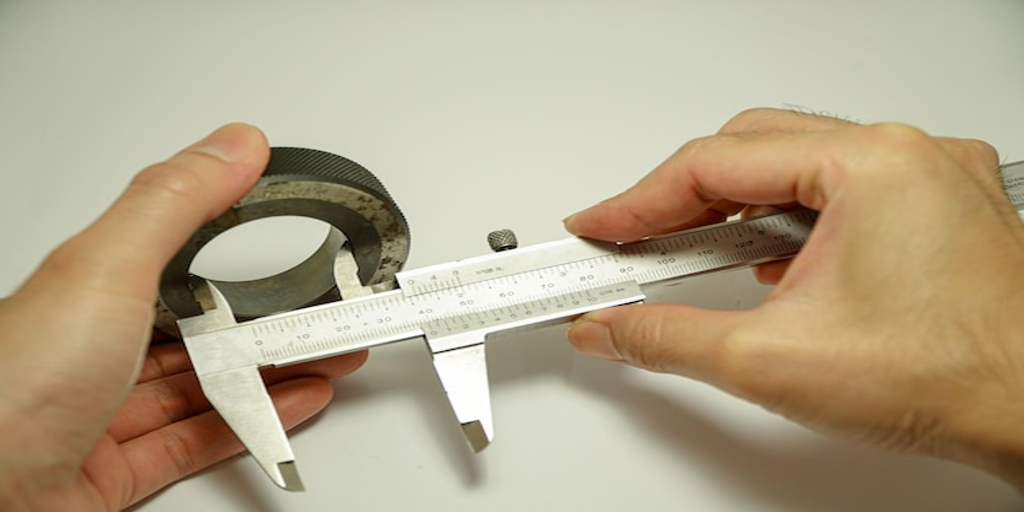
When exploring the world of metalworking and manufacturing, one term that often surfaces is “steel gauge.” While it might seem like a straightforward concept at first glance, understanding steel gauge measurements is crucial for anyone involved in projects that require metal sheets, tubes, or other structural components. This article delves deep into the intricacies of steel gauge measurements, their historical context, practical applications, and how to choose the right gauge for your specific needs.
What is Steel Gauge?
Steel gauge refers to a standardized method of measuring the thickness of metal sheets, wires, and other products. Unlike conventional measurements such as inches or millimeters, the gauge system operates on a numerical scale where a higher gauge number signifies a thinner material. For example, a 14-gauge steel sheet is thicker than a 16-gauge sheet. This measurement system is widely used in industries ranging from construction to automotive manufacturing, providing a consistent way to specify metal thickness.
The Inverse Relationship of Gauge Numbers
The gauge system operates on an inverse relationship: as the gauge number increases, the thickness of the material decreases. This can be somewhat counterintuitive, especially for those accustomed to traditional measurement systems. Understanding this relationship is essential for selecting the appropriate material for any given application, ensuring that the final product meets both functional and aesthetic requirements.
Historical Context of Gauge Measurements
The origins of the gauge system can be traced back to the British iron wire industry during the Industrial Revolution. At that time, there was no universal standard for measuring the thickness of metal. Workers would refer to the number of times a wire was drawn to determine its diameter, leading to the establishment of the gauge system. This historical context is important as it highlights the evolution of measurement systems and their continued relevance in modern manufacturing.
Why Use Gauge Instead of Traditional Measurements?
One of the primary reasons the gauge system is favored over traditional measurements is its simplicity and consistency. The gauge system provides a universal standard that manufacturers and suppliers can rely on, facilitating communication across various industries. Instead of specifying a thickness in decimal inches or millimeters, users can simply refer to the gauge number, streamlining the ordering and production processes.
Advantages of Using Gauge Measurements
- Standardization: Gauge measurements provide a consistent framework for specifying metal thickness, reducing confusion and errors in communication.
- Ease of Use: The gauge system simplifies the process of identifying the appropriate material for a project, making it easier for engineers and fabricators to make quick decisions.
- Widely Accepted: The gauge system is recognized and used globally, making it easier to source materials from different suppliers without worrying about measurement discrepancies.
Selecting the Right Steel Gauge
Choosing the appropriate steel gauge for a project depends on various factors, including the intended application, required strength, and flexibility of the material. Thicker materials provide greater strength but may lack the flexibility needed for certain designs. Conversely, thinner materials are more malleable but may not withstand heavy loads or harsh environments.
Key Considerations for Gauge Selection
- Application Requirements: Determine the specific needs of your project, including load-bearing capabilities and environmental conditions.
- Material Properties: Understand the characteristics of the material you are working with, including its tensile strength, ductility, and corrosion resistance.
- Design Specifications: Consider the design of the final product, including any bends, curves, or joints that may require specific gauge thicknesses.
Common Applications and Recommended Gauges
- Structural Components: For load-bearing applications, lower gauge numbers (thicker materials) are typically recommended.
- Flexible Designs: Higher gauge numbers (thinner materials) are suitable for components that require bending or shaping.
- Specialized Uses: Certain applications, such as cabinets for storing flammable materials, may have specific gauge requirements for safety and compliance.
Understanding Gauge Charts
Gauge charts serve as valuable tools for determining the thickness of steel sheets based on gauge numbers. These charts outline the thickness in both inches and millimeters, providing a quick reference for fabricators and manufacturers. Familiarizing yourself with these charts is essential for accurate material selection.
How to Read a Gauge Chart
- Locate the Gauge Number: Find the desired gauge number in the chart.
- Check the Corresponding Thickness: Look across the row to identify the associated thickness in inches and millimeters.
- Consider Material Type: Be aware that different materials may have different gauge thicknesses, so always refer to the appropriate chart for the specific metal you are working with.
Example of a Gauge Chart
Gauge Thickness (inches) Thickness (mm) 8 0.164 4.19 10 0.135 3.43 12 0.105 2.67 14 0.075 1.91 16 0.060 1.52 18 0.048 1.22 20 0.036 0.91 The Importance of Accurate Gauge Selection
Selecting the correct gauge for your project is crucial for ensuring durability, efficiency, and cost-effectiveness. The right thickness can significantly impact the performance and lifespan of the final product, making it essential to consider all factors before making a decision.
Durability and Strength
Using the appropriate gauge thickness ensures that the material can withstand the stresses and strains of its intended use. For instance, a construction project requiring high rigidity and strength will benefit from lower gauge materials, while applications involving intricate designs may necessitate higher gauge options for flexibility.
Economic Considerations
Thicker materials generally incur higher production and shipping costs. Therefore, it is wise to specify thinner materials wherever possible, especially for components that do not face significant stress or environmental challenges. This approach can lead to substantial cost savings without compromising quality.
Efficiency in Fabrication
Choosing the right gauge also plays a critical role in the efficiency of the fabrication process. Selecting materials that align with the project’s requirements minimizes waste and optimizes production timelines. This consideration is particularly important in high-volume manufacturing environments where efficiency is paramount.
Common Types of Steel Gauges
Various types of gauges are available for measuring steel thickness, each with its unique features and applications. Understanding these different types can help you select the best tool for your specific needs.
Caliper Gauges
Caliper gauges are commonly used for measuring the thickness of sheet metal and can be categorized into three main types:
- Vernier Caliper: This traditional tool allows for precise measurements, typically down to 0.02 millimeters or 0.001 inches. It is especially useful for measuring round objects like tubing.
- Dial Caliper: Similar to the vernier, the dial caliper uses a rotating dial to display measurements, offering the same level of accuracy.
- Digital Caliper: This modern alternative employs electronic sensors to provide instant readings in both metric and imperial units, enhancing ease of use.
Ultrasonic Gauges
Ultrasonic thickness gauges utilize sound waves to measure material thickness. A small probe generates a sound pulse that travels through the material and returns to the device. The time taken for the pulse to travel back is used to calculate the thickness. This method is particularly effective for measuring materials that are difficult to access or where traditional tools may not be feasible.
Ferrous vs. Non-Ferrous Metals
Understanding the difference between ferrous and non-ferrous metals is essential when selecting the appropriate gauge. Each type of metal has distinct properties that influence its use in various applications.
Ferrous Metals
Ferrous metals, which contain iron, are known for their strength and durability. Common examples include:
- Carbon Steel: Widely used in construction and manufacturing, carbon steel is known for its high tensile strength.
- Cast Iron: Often used in heavy-duty applications, cast iron is renowned for its excellent wear resistance.
- Wrought Iron: This malleable metal is commonly used for decorative elements and structural applications.
Non-Ferrous Metals
Non-ferrous metals do not contain iron, making them more resistant to rust and corrosion. Examples include:
- Aluminum: Lightweight and malleable, aluminum is often used in aerospace and automotive applications.
- Copper: Known for its excellent conductivity, copper is widely used in electrical wiring and plumbing.
- Zinc: Frequently used for galvanizing steel to prevent corrosion, zinc is an essential material in construction.
Practical Applications of Steel Gauge in Various Industries
Steel gauge measurements play a vital role in numerous industries, each with its specific requirements and standards. Understanding these applications can help you make informed decisions when selecting materials for your projects.
Construction Industry
In the construction sector, steel gauge is critical for ensuring structural integrity. Load-bearing components such as beams and columns often require lower gauge materials for maximum strength. Additionally, regulations may dictate specific gauge requirements for safety and compliance, especially in high-risk environments.
Automotive Manufacturing
The automotive industry relies heavily on steel gauge measurements for various components, including frames, body panels, and exhaust systems. Thicker gauges are typically used for structural elements, while thinner gauges may be employed for non-load-bearing parts to reduce overall vehicle weight and improve fuel efficiency.
Aerospace Engineering
Aerospace applications demand precise engineering and material selection. Thinner gauges are often used in aircraft components to minimize weight without sacrificing strength. The use of high-strength, lightweight materials is essential for achieving optimal performance and fuel efficiency in aviation.
Conclusion
Understanding steel gauge measurements is crucial for anyone involved in metalworking or manufacturing. By grasping the significance of gauge numbers, the historical context of the measurement system, and the factors influencing gauge selection, you can make informed decisions that enhance the quality and performance of your projects. Whether you’re working in construction, automotive, or aerospace, the right steel gauge will ensure that your components meet the necessary standards for durability, efficiency, and cost-effectiveness. As you embark on your next project, remember the importance of selecting the appropriate gauge to achieve your desired outcomes.